Stainless flange nuts are an indispensable component in many industrial applications, providing both security and stability in various mechanical assemblies. Their unique design and properties make them a preferred choice for professionals seeking reliability and efficiency.
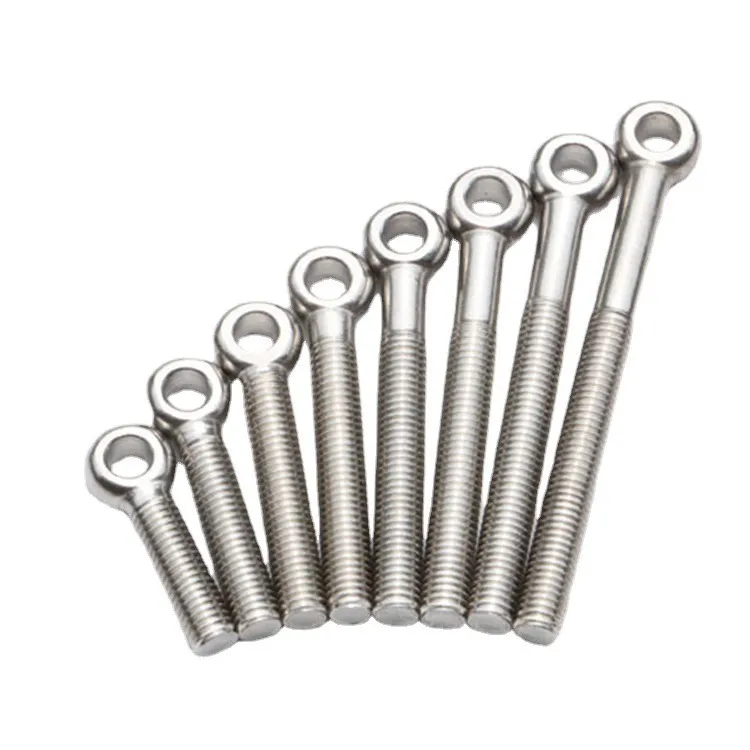
To understand the appeal of stainless flange nuts, one must acknowledge their construction. Made predominantly from stainless steel, these nuts are resistant to corrosion, an essential feature for any hardware constantly exposed to moisture, chemicals, or fluctuations in temperature. This characteristic makes them ideal for environments where rust and material degradation could compromise structural integrity.
The flange design adds to their functionality. The flange serves as an integrated washer, and this extension helps distribute the pressure extended by the nut over a larger surface area. This distribution prevents damage to the attached fixture while ensuring a firm and enduring hold. For tradespeople and engineers, this means a more straightforward installation process that minimizes the need for additional washers, thus saving time and resources.
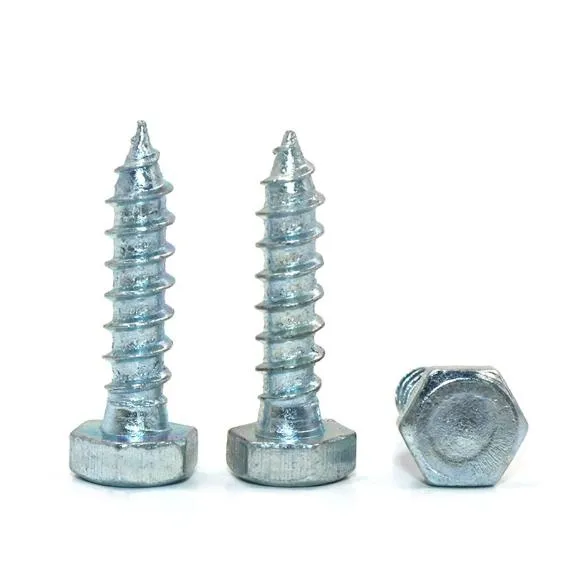
One common application is in the automotive industry. Vehicles contend with constant vibrations and harsh elements, making the anti-loosening qualities of stainless flange nuts invaluable. Their ability to maintain tight connections under duress is vital for maintaining safe and efficient automotive operations. Moreover, their aesthetic appeal due to the polished finish of stainless steel ensures they blend seamlessly, or even enhance, the design aesthetics of vehicles.
In construction, these nuts are utilized to join heavy beams and girders. Here, the reliability and strength of stainless flange nuts are trusted to secure significant weight loads and resist the natural corrosion-inducing elements at construction sites. The strength they offer cannot be overstated in an industry where safety and precision are paramount.
Beyond industry, DIY enthusiasts also appreciate the practical benefits of stainless flange nuts. For home improvement tasks requiring a secure fastening solution, these nuts offer an ideal blend of durability and ease of use. Their straightforward installation process appeals to hobbyists who may not have professional-grade tools accessible.
stainless flange nuts
From a technical standpoint, the specifications of stainless flange nuts, including thread sizes and dimensions, are standardized. Compliance with such standards ensures compatibility across different projects and industries, positioning these nuts as a versatile choice in mechanical workflows.
When sourcing stainless flange nuts, it's crucial for professionals to consider the grades of stainless steel available. The grades influence the mechanical properties; for example, 304 and 316 are popular for their superb corrosion resistance and strength. The choice of grade should align with the specific environmental and mechanical demands of the application.
Furthermore, when selecting a supplier for stainless flange nuts, credibility and reliability are vital. A credible supplier will ensure the nuts meet or exceed industry standards and provide timely delivery to keep projects on schedule. Professionals should seek suppliers with a history of exemplary customer service and positive reviews in the industry. Warranty and certification are additional factors that enhance trust in the product offered.
To ensure the effectiveness of stainless flange nuts in their applications, routine maintenance and inspection can prevent loosening over time, thereby extending the lifespan of the assembly. This proactive approach can prevent costly repairs and maintain the overall efficiency of the systems in which these components have been installed.
In summary, stainless flange nuts are not merely a fastening solution; they epitomize durability, reliability, and efficiency across various sectors. From industrial engines to home renovation projects, their application showcases their necessity and versatility. Understanding their functionality, selecting the appropriate grade, and choosing a trusted supplier are critical steps in leveraging their full potential in ensuring the structural success of any project.