Hex machine screw nuts, often found at the heart of countless mechanical and industrial applications, are a cornerstone in engineering due to their pivotal role in ensuring stability and strength in joined materials. Offering a blend of robustness and versatility, these components prove indispensable across numerous industries.
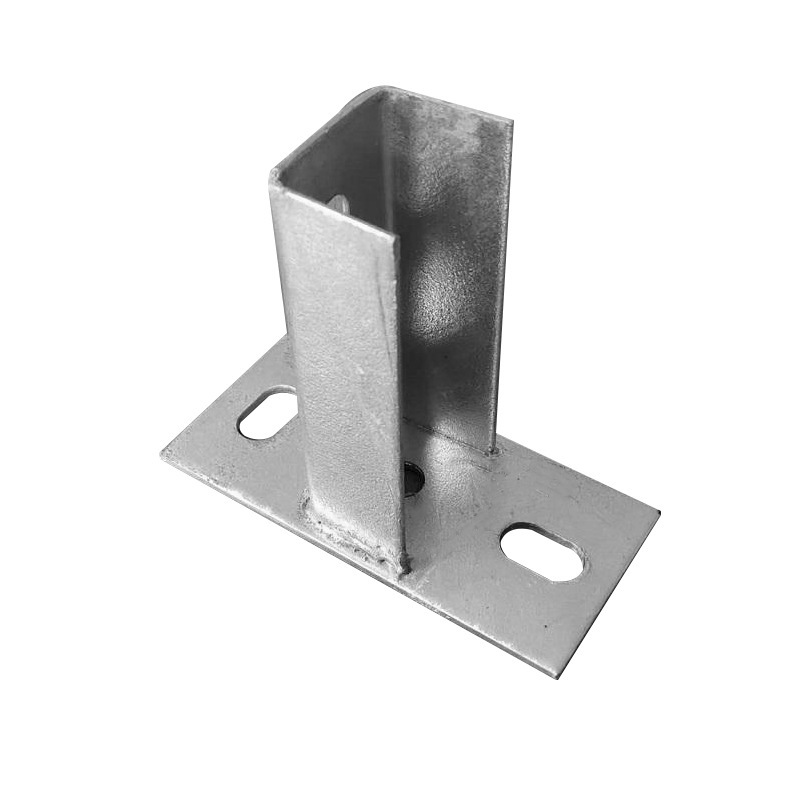
One of the defining characteristics of hex machine screw nuts is their distinctive hexagonal shape, which provides six flat sides. This geometry is not merely aesthetic; it allows the nut to be firmly gripped by a wrench or spanner, facilitating both application and removal. The hex shape enables more torque to be applied evenly when tightening, ensuring a secure hold without damaging the nut or the material it is attached to.
An expert in machinery will appreciate the material composition critical to the functionality of hex machine screw nuts. Commonly made from steel, brass, stainless steel, or nylon, each material offers distinct advantages. Steel nuts, for example, are prized for their strength and affordability. When corrosion resistance is paramount, stainless steel is the go-to material, making it ideal for outdoor or marine environments. Brass nuts offer excellent thermal conductivity and resistance to corrosion – a perfect choice for plumbing and electrical applications. Nylon nuts, on the other hand, provide a lightweight alternative when metallic solutions may cause interference or excess weight.
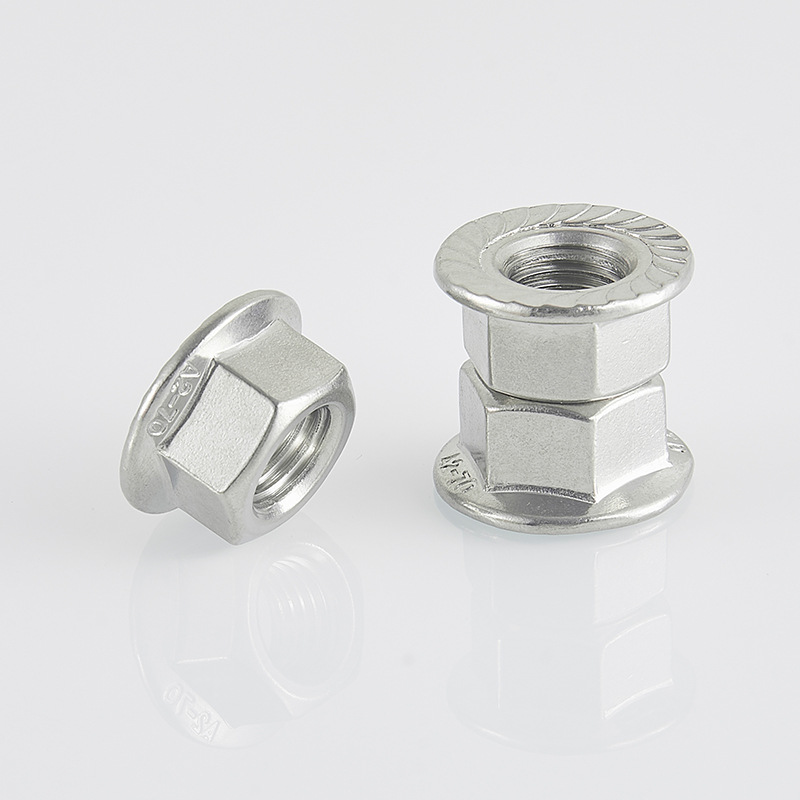
Through years of professional experience, engineers have come to understand that the threading of the nuts plays a significant role in its application. Threads on hex machine screw nuts are engineered to match their counterpart bolts, screws, or studs.
The precision of these threads is crucial; misalignment can compromise the structural integrity and result in mechanical failure. Thus, adherence to standardized thread pitches and diameters, such as those defined by the National Coarse (NC), National Fine (NF), and metric standards, ensures compatibility and reliable performance across various applications.
hex machine screw nut
In industries such as automotive manufacturing, construction, and aerospace, the expertise required to select the right hex machine screw nut is considerable. Each industry poses its own set of challenges in terms of environmental conditions, stress factors, and material compatibility. For instance, the aerospace sector demands nuts that not only possess high tensile strength but are also lightweight to accommodate flight weight restrictions. In contrast, construction applications prioritize corrosion resistance and ease of assembly, aligning with long-term durability goals.
Furthermore, the trustworthiness of a supplier or manufacturer contributing to the ecosystem of hex machine screw nuts cannot be understated. Reputable suppliers undergo rigorous quality assurance practices, ensuring each nut adheres to industry standards. This commitment to quality affords engineers the confidence that the components they are relying upon will perform as expected, even under the most demanding circumstances.
A significant trend impacting the evolution of hex machine screw nuts is the growing emphasis on sustainability. Industries are increasingly seeking solutions that minimize environmental impact while maintaining optimal performance. This has led to the innovation of eco-friendly coatings and processes during the manufacturing phases of these nuts, catering to the global push towards sustainable practices.
Ultimately, selecting the right hex machine screw nut involves more than just choosing any nut off the shelf. It requires a thorough understanding of materials, threading standards, industry requirements, and the performance credentials of suppliers. Engaging with experienced professionals who possess authoritative knowledge about these components can make a marked difference, ensuring that applications not only meet but exceed required safety and reliability standards. The benefits of this meticulous approach convey well beyond the immediate requirements, establishing a foundation of trust and continued innovation in mechanical design and application.