In the realm of industrial manufacturing, the importance of small components is often overlooked, yet they form the backbone of countless machinery and structures.
Custom made steel washers are a prime example of this critical, yet understated, segment. These small but mighty components can dramatically influence the performance, durability, and safety of the machines and structures they support. The nuances of creating and using custom made steel washers are pivotal to the reliability of major industries, requiring a deep understanding of both the materials and the machining processes involved.
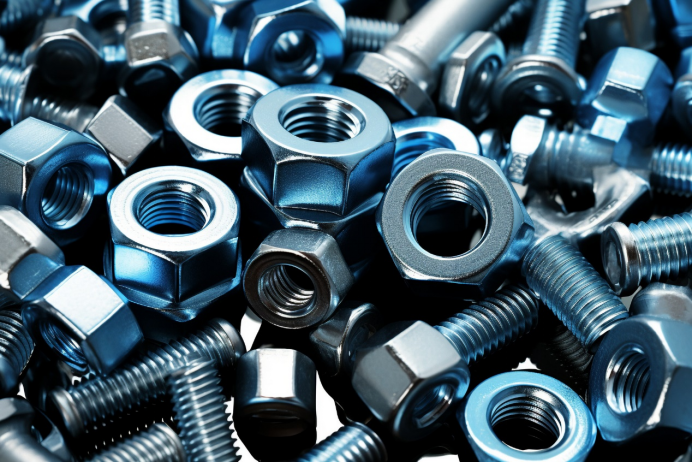
Custom washers differ from their standard counterparts due to their tailored thickness, diameter, and metal composition which address specific engineering demands. While standard washers might suffice for general purposes, custom made versions are essential for specialized applications. For example, these washers play crucial roles in automotive engineering, construction, and aerospace industries, where precision and resilience are non-negotiable.
The material choice for custom washers is critical and is influenced by the washer’s operational environment. Steel, renowned for its strength, versatility, and resistance to extreme conditions, is a preferred material. However, the type of steel selected—whether it’s stainless, carbon, or alloy steel—adds a level of complexity that requires engineering finesse. Stainless steel, albeit more expensive, is generally chosen for environments where corrosion resistance is paramount. Contrarily, carbon steel might be chosen for its superior load-bearing capabilities, provided corrosion isn’t a primary concern.
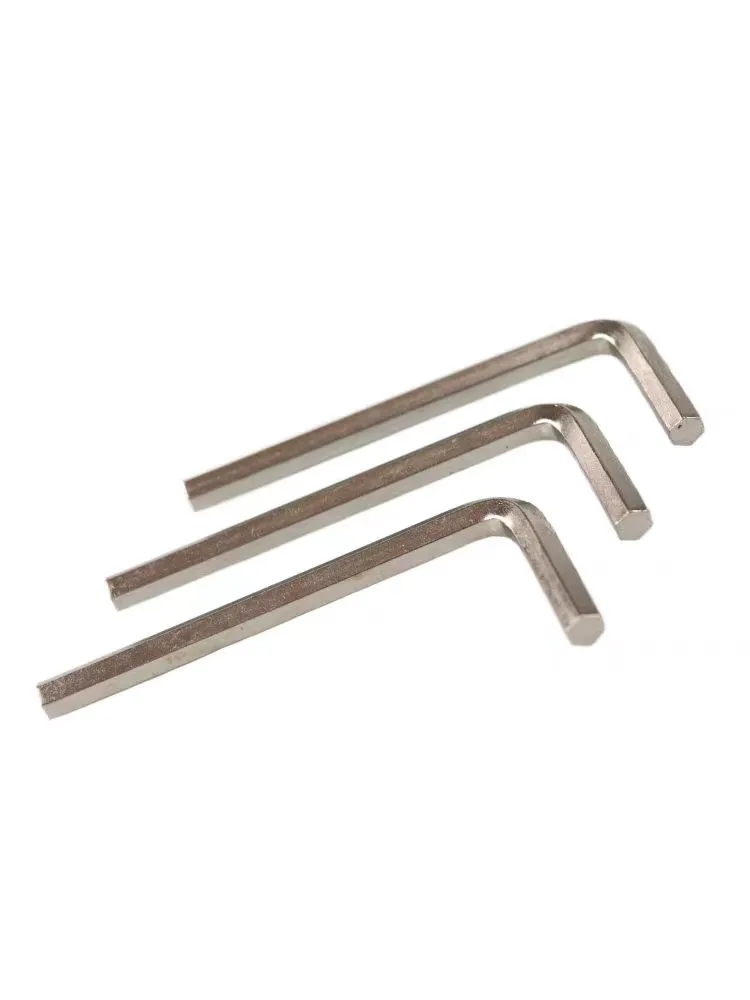
No two operations requiring custom washers are identical, making the expertise of experienced engineers invaluable. Their authoritative knowledge ensures that each custom specification meets stringent performance and safety standards. For instance, in high-stress mechanical systems, a miscalculation in washer thickness could lead to mechanical failure, emphasizing the importance of precision in customization.
Innovation in manufacturing technologies has played a substantial role in elevating the quality and adaptability of custom washers. CNC machining, laser cutting, and advanced forging techniques allow for greater precision and a broader range of customization than ever before. These technologies reduce human error and material wastage, enabling manufacturers to uphold high standards of quality—a crucial factor in maintaining trustworthiness among clientele.
custom made steel washers
Additionally, real-world experience underscores the importance of testing and quality assurance. Through rigorous stress tests and simulations, manufacturers can predict how a custom washer will perform under various conditions. It’s a process that bolsters the trust placed in these components and highlights the manufacturer’s commitment to delivering trustworthy products.
For engineers and procurement specialists, understanding the breadth of applications for custom made steel washers can streamline the decision-making process. Their applications aren’t confined to traditional uses; with innovations, even industries like renewable energy are finding value in these components. In turbines and solar panel installations, custom washers are essential for ensuring components are secure and optimally aligned.
Lastly, the procurement of custom made steel washers demands a thorough evaluation of a manufacturer’s capability, reputation, and adherence to international standards. A manufacturer’s track record in delivering precise and durable products speaks volumes about their expertise and reliability. Before engagement, verifying certifications and past client experiences can prevent potential pitfalls, assuring that the supplied components will meet demanding operational requirements.
Thus, the journey of a custom made steel washer from conception to application is a testament to human ingenuity and meticulous craftsmanship. In an industry where every component counts, opting for custom solutions not only optimizes performance but also fosters a culture of innovation and excellence. With the right combination of expertise, advanced technology, and commitment to quality, custom made steel washers will continue to support and advance diverse industrial applications worldwide.