The 16mm flange nut is a vital component in numerous industrial and mechanical applications, bringing precision, stability, and reliability to a wide array of projects. This small yet mighty item is designed to fulfill specific needs in the fastening and securing domain, making understanding its applications, manufacturing, and utility essential for both professionals and enthusiasts.
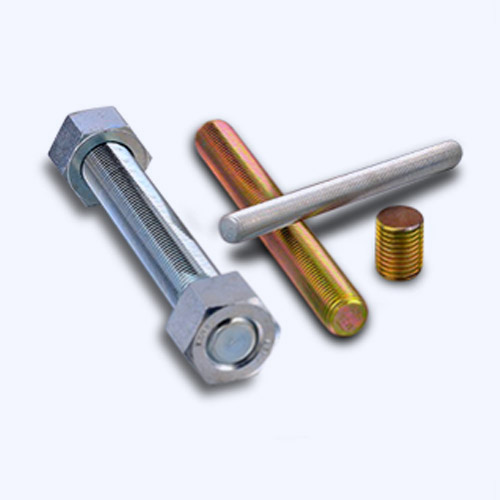
Flange nuts, in general, are distinct due to the flange that extends from the nut’s bottom. This unique design slickly distributes the clamping load over a wider area, which reduces the risk of damage to the parts being secured and simultaneously enhances their grip strength. Specifically, the 16mm variant of the flange nut plays a crucial role in industries such as automotive, construction, and manufacturing due to its remarkable specifications that cater to high-stress environments.
One cannot overlook the exceptional experience professionals gain when utilizing a 16mm flange nut in automotive settings. Here, they are often used to securely fasten components such as axles or exhaust systems, where maintaining structural integrity is paramount. Mechanics appreciate the flange nut's ability to remain secure even amidst intense vibrations, showcasing its durability and ensuring safety on the road.
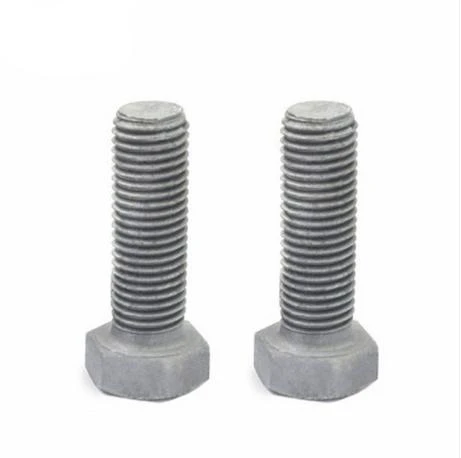
From an expertise standpoint, understanding the materials that comprise the 16mm flange nut can inform its selection for specific applications. Typically, these nuts are manufactured from high-grade steel or stainless steel, sometimes with a coating of zinc or phosphates to enhance corrosion resistance. This material choice reflects an in-depth knowledge of the environments these nuts will likely endure, providing them with an edge in resistance against rust and wear, thus prolonging their lifespan and effectiveness.
16mm flange nut
The authority of the 16mm flange nut within the fastening domain can be attributed to its regulatory compliance and meticulous standards in manufacturing. They are often produced in accordance with DIN or ISO standards, which delineate precise dimensions, tolerances, and mechanical properties ensuring uniformity and reliability. For engineers and designers, this guarantees that the flange nuts they employ will seamlessly integrate with other standardized components, fostering efficiency and adherence to safety standards in project execution.
A critical aspect that underscores the trustworthiness of a 16mm flange nut is the multitude of quality assurance tests it undergoes during production. Tensile strength, hardness, and fatigue endurance tests are just a few of the rigorous evaluations performed to verify the nut's capability to withstand multiple stressors.
Consumers can rest assured that the flange nut will perform reliably, reducing the likelihood of unforeseen failures.
In terms of real-world applications, consider a 16mm flange nut being deployed in a high-pressure piping system in a chemical plant. In such a scenario, the nut's role extends beyond mere fastening; it contributes to maintaining the integrity of the pipeline system. Here, any compromise in securing can lead to catastrophic leaks or system failures. Hence, reliability under these circumstances isn’t just an advantage — it’s a necessity.
In conclusion, the 16mm flange nut is indispensable due to its robustness and engineered precision. With its tendency to evenly distribute loads and prevent loosening, it stands out in terms of performance across various sectors. By offering insights into its applications, materials, and the rigorous standards it meets, this overview underscores how knowledgeable professionals leverage the capabilities of this humble component to achieve long-lasting, safe, and efficient results. This comprehensive understanding equips engineers, mechanics, and DIY enthusiasts alike with the confidence to deploy 16mm flange nuts in even the most challenging settings.