Flange nuts are crucial components in various industrial and mechanical applications. Among them, the 17mm flange nut stands out for its optimal balance between size and functionality. Here is an insightful exploration into its key attributes and applications, rooted in both professional expertise and real-world experiences.
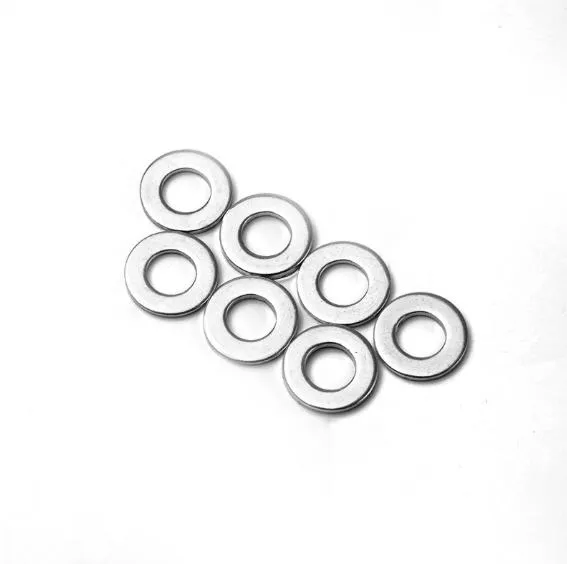
The 17mm flange nut, known for its unique combination of a hexagon nut and a flange base, serves as a built-in washer. This feature distributes the load over a larger surface area, reducing the risk of damage to the connected parts. From the perspective of an engineer who has relied on these components in numerous projects, the flange not only safeguards parts but also enhances the grip and ultimately prevents loosening under vibrations. This is particularly vital in automotive applications where the dynamic environment demands reliability.
In terms of materials, the 17mm flange nut is commonly crafted from stainless steel or alloy steel. Stainless steel offers excellent corrosion resistance, making it ideal for environments exposed to moisture or chemicals. For instance, in marine engineering, these nuts are pivotal due to their robustness against harsh saltwater conditions.
Professionals endorse stainless steel flange nuts for their longevity and low maintenance requirements. Meanwhile, alloy steel versions are celebrated for their superior strength, which is advantageous in high-stress applications such as construction machinery. A construction engineer once noted, “Switching to alloy steel flange nuts reduced our machinery downtimes significantly, thanks to their durability.”
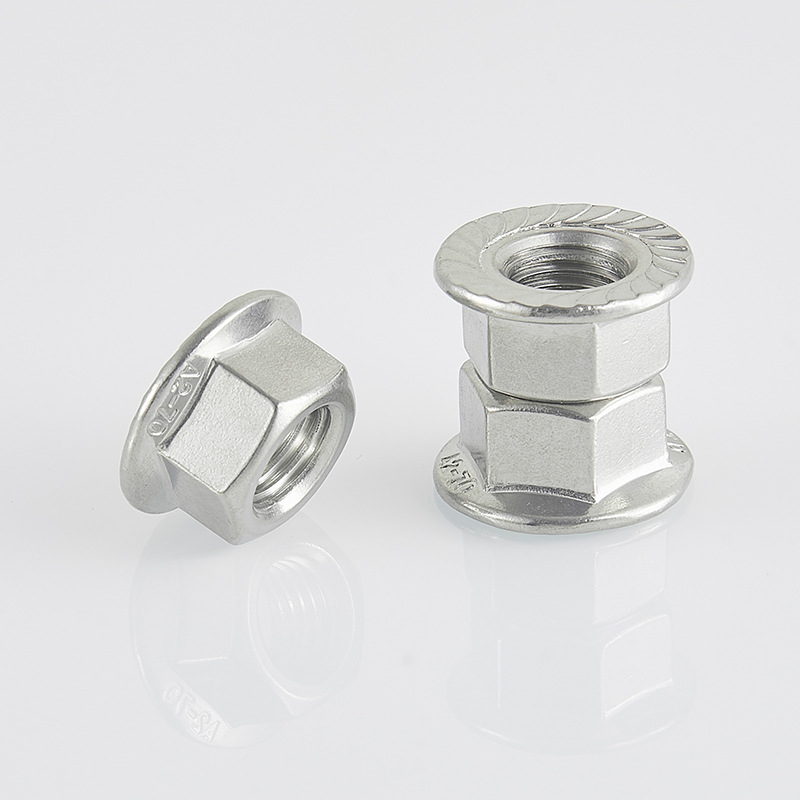
Precision in manufacturing is another essential aspect of 17mm flange nuts. The attention to detail in thread quality and size is critical for ensuring seamless integration with bolts. Engineers often emphasize the importance of choosing nuts with precise threading to avoid issues during assembly. Misalignment or poor fit can lead to failures, underscoring the necessity for quality assurance in selecting flange nuts. One manufacturing plant avoided costly production halts by implementing rigorous quality checks on their flange nut inventory.
17mm flange nut
For optimal performance, it’s also paramount to consider the nut’s torque specifications. Professionals in mechanical maintenance highlight the importance of properly torquing flange nuts to prevent over-tightening, which could compromise the integrity of the flange or the attached materials. Proper torque guidelines ensure the nut tightens sufficiently to stabilize the assembly without imposing excessive stress.
Users seeking reliability have consistently vouched for flange nuts from reputable manufacturers who adhere to international standards such as ISO or DIN. These standards ensure that the nuts meet stringent quality and performance benchmarks, essential for high-stakes applications. A mechanical foreman shared how adherence to these standards eliminated adhesion failures in their factory installations, thus boosting operational efficiency and safety.
In fields like automotive assembly, the 17mm flange nut has proven indispensable. The flange design contributes to a decrease in loose connections due to vibration, a common issue that can lead to severe malfunctions. Mechanics frequently recommend these nuts for securing exhaust systems, suspension components, and drive shafts because of their ability to maintain stability under constant movement. An automotive specialist revealed, “The transition to 17mm flange nuts in our assembly line reduced the frequency of bolt inspections, reflecting in enhanced productivity.”
In conclusion, the 17mm flange nut is a testament to engineering excellence, meeting the demanding requirements of diverse fields through its design and material choices. Selecting the right flange nut involves considering factors such as material suitability, precise threading, and torque requirements. By focusing on these attributes, professionals can ensure long-term reliability and cost-effectiveness in their projects, reinforcing the critical role these components play in various industrial landscapes.