Disc springs, also known as Belleville washers, are vital components widely embraced across various industries, particularly in applications requiring reliable load bearing with minimal movement or gaps. Among the numerous standards governing these components, DIN 2093 is perhaps one of the most well-regarded, emphasizing strict guidelines on the shapes, materials, and dimensions of disc springs to ensure top-tier performance and quality.

At the core of the DIN 2093 disc spring's importance lies its ability to accommodate large loads within a compact area, making them indispensable in engineering disciplines where space and weight are constrained. This feature is particularly beneficial in automotive, aerospace, and industrial manufacturing, where efficiency and reliability are paramount. These small yet mighty springs play crucial roles in clutch and brake systems, safety valve systems, and bearing preloading to name a few.
Professionals in the engineering sector favor DIN 2093 springs not just for their mechanical attributes but also for their adherence to precision manufacturing standards. The consistency that these standards offer is mirrored in the springs’ longevity and performance reliability. Manufactured typically from high-grade materials such as spring steel (51CrV4), these springs offer exceptional resistance to environmental factors and mechanical stress, essential for maintaining functionality even in demanding conditions.
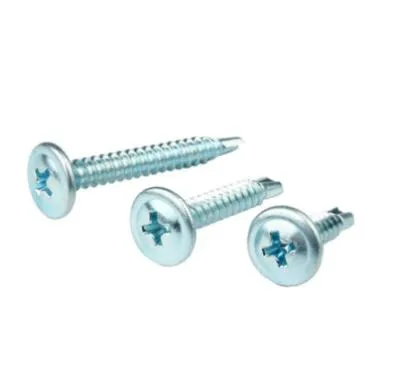
One of the standout qualities of DIN 2093 disc springs is their fatigue life. The design and heat treatment processes ensure that these springs can withstand repetitive stress without succumbing to fatigue failure. It is this durability that underlines their use in life-sustaining applications such as in the medical field or in safety equipment. A well-implemented maintenance regime further extends their life, reflecting hundreds of thousands of cycles under substantial load without failure.
To tap the most out of a DIN 2093 disc spring, precise installation is crucial. Assembling these springs correctly ensures that maximum force distribution is achieved uniformly, which is critical in applications where even slight deviations can result in catastrophic system failures. Some of the best practices include ensuring alignment during installation and employing the correct stack configurations to either increase force or deflection characteristics.
din 2093 disc spring
Expert recommendations also suggest regular performance evaluations of these springs to detect early signs of wear or failure. Moreover, when replacement is needed, opting for springs that adhere strictly to DIN 2093 standards is non-negotiable. This guarantees performance compatibility and spares the costly risk of system inefficiencies or failures.
From the perspective of expertise and authority, engineers and industry professionals alike commend the DIN 2093 standards for setting a high benchmark in mechanical quality and performance. Research indicates that springs adhering to these standards outperform their non-standard counterparts in terms of repeatability, efficiency, and lifespan. This has prompted many industry-leading companies to integrate these springs into their machinery and product designs.
Furthermore, the integrity and trustworthiness of manufacturers is a facet that cannot be overlooked. Partnering with manufacturers recognized for strict compliance with international quality standards ensures access to genuine, high-performance disc springs. Industry leaders often provide comprehensive support in terms of technical data, installation guidance, and after-sales service, which is instrumental in building long-term professional relationships founded on trust and quality assurance.
In conclusion, DISC 2093 disc springs are not mere components but fundamental elements that contribute significantly to the operational efficacy of various critical applications. Their precision design, backed by rigorous standards, integrates seamlessly into complex systems, providing engineers with reliable solutions that cater to both current operational needs and future advancements. As industries continue to evolve and demand even more robust solutions, the crucial role of these standardized components in driving reliability and performance is set to expand further.