Self-Piercing Sheet Metal Screws A Comprehensive Guide
In the realm of mechanical engineering and construction, self-piercing sheet metal screws have emerged as a game-changer. These innovative fasteners offer a quick and efficient solution for joining metal sheets without the need for pre-drilling or additional holes. This article delves into the intricacies of self-piercing sheet metal screws, their applications, benefits, and best practices for their use.
What Are Self-Piercing Sheet Metal Screws?
As the name suggests, self-piercing sheet metal screws are designed to penetrate metal sheets without the need for a pre-existing hole. They consist of a sharp point that is capable of piercing the material upon insertion, followed by a thread that secures the joint. These screws are typically made from high-strength steel and are available in a range of sizes and materials to suit different applications.
Applications of Self-Piercing Sheet Metal Screws
Self-piercing sheet metal screws find widespread application in a variety of industries, including automotive, aerospace, construction, and appliance manufacturing. They are commonly used to join metal sheets in the production of body panels, hoods, trunk lids, and other automotive components. In the aerospace industry, these screws are utilized in the assembly of aircraft fuselage and wing sections. Construction applications include the fastening of metal roofing and siding, while appliance manufacturers rely on them to assemble refrigerators, washing machines, and other large appliances.
Benefits of Using Self-Piercing Sheet Metal Screws
The use of self-piercing sheet metal screws offers several advantages over traditional methods of metal joining. Firstly, they eliminate the need for pre-drilling, which saves time and labor costs. Secondly, the process of self-piercing generates minimal scrap material, resulting in cost savings and reduced waste. Additionally, these screws provide a strong and reliable bond between metal sheets, making them ideal for applications where strength and durability are paramount.
Best Practices for Using Self-Piercing Sheet Metal Screws
When using self-piercing sheet metal screws, it is essential to follow best practices to ensure optimal performance and longevity of the joints
Best Practices for Using Self-Piercing Sheet Metal Screws
When using self-piercing sheet metal screws, it is essential to follow best practices to ensure optimal performance and longevity of the joints
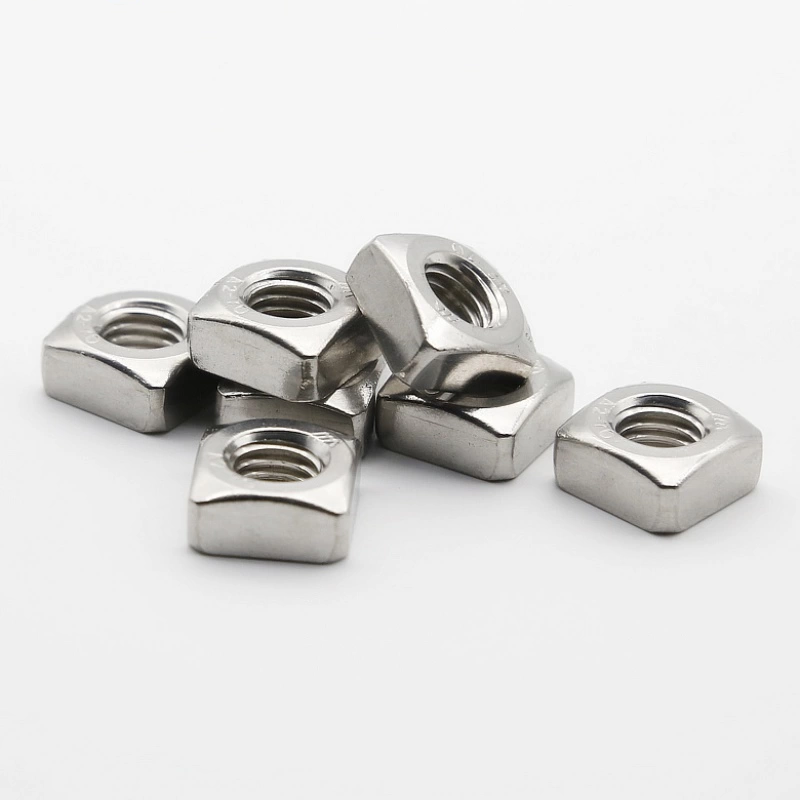
Best Practices for Using Self-Piercing Sheet Metal Screws
When using self-piercing sheet metal screws, it is essential to follow best practices to ensure optimal performance and longevity of the joints
Best Practices for Using Self-Piercing Sheet Metal Screws
When using self-piercing sheet metal screws, it is essential to follow best practices to ensure optimal performance and longevity of the joints
self piercing sheet metal screws. Here are some tips to consider
1. Choose the right screw Select a screw with the appropriate size, thread pitch, and material to match the properties of the metal sheets being joined.
2. Prepare the surfaces Ensure that the metal sheets are clean and free of any contaminants before attempting to pierce them.
3. Use the correct torque Apply the recommended torque when installing the screws to avoid over-tightening or stripping the threads.
4. Monitor the process Keep an eye on the piercing and threading process to ensure that the screws are installed correctly and that the metal sheets are not damaged.
5. Inspect the joints Regularly inspect the joints for signs of wear or damage and replace any screws that show signs of failure.
In conclusion, self-piercing sheet metal screws represent a significant advancement in the field of metal joining. Their ability to join metal sheets quickly and efficiently, coupled with their strong and reliable performance, make them an attractive option for a wide range of applications. By following best practices for their use, engineers and manufacturers can maximize the benefits of these innovative fasteners and achieve superior results in their projects.