Finding the right components for construction and mechanical projects is crucial for ensuring longevity and efficiency. The M12 thick washer, while seemingly a simple hardware item, plays a vital role in various applications. Its importance stems from its design and material properties, each optimized for handling substantial loads and pressures that occur in fastened joints.
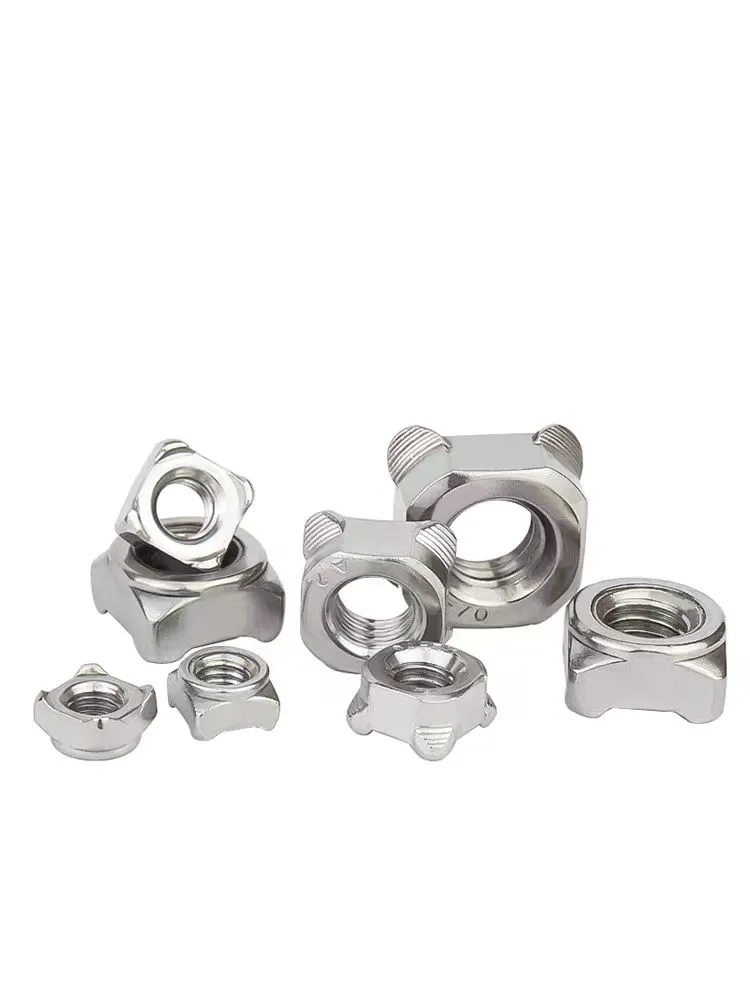
An M12 thick washer is not just a piece of metal with a hole in the middle; it is engineered for specific functions. Its primary purpose is to distribute the load evenly across surfaces when pressure is applied via a bolt or a nut. In heavy-duty applications where integrity and safety are paramount, the M12 thick washer prevents damage to the clamped material, mitigating wear and tear by absorbing vibrations.
Why choose an M12 thick washer over standard variations? The answer lies in its thickness, which offers broader weight distribution, reducing the risk of structural damage. This characteristic makes it indispensable in sectors such as construction, automotive, and machinery manufacturing, where it helps maintain the integrity of assemblies under dynamic stress conditions.
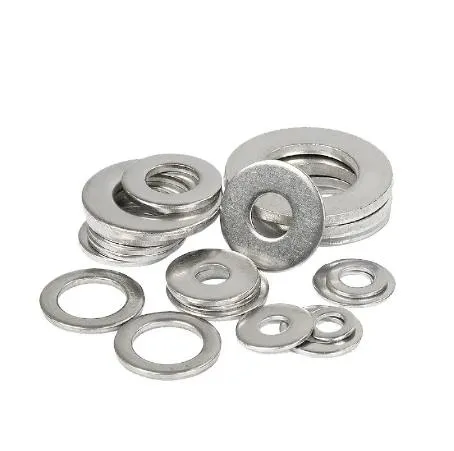
The versatility of M12 thick washers is enhanced by their range of materials. Stainless steel versions provide corrosion resistance, making them ideal for outdoor or high-moisture environments. For heavy machinery, high-tensile steel variants can withstand extreme force, extending the lifespan of the machinery and reducing maintenance costs. Meanwhile, plastic washers cater to industries where insulation and non-conductiveness are necessary, such as electronics.
m12 thick washer
Selecting the right material and design of an M12 thick washer is crucial. A professional evaluation of the application environment and load expectations is often necessary. Consulting with a structural engineer or a mechanical expert aids in choosing a washer that ensures safety and efficiency. By prioritizing expert guidance, businesses can avoid common pitfalls such as underperformance of materials under stress or environmental degradation from inappropriate metal choices.
In real-world settings, successful implementation of M12 thick washers can be seen. In the construction of high-rise buildings, they are used to affix structural bolts to foundational beams. The thick design ensures that even under high tensile stress, the washer maintains its shape and function, preventing the loosening of connections that could lead to structural failures. Additionally, in automobile manufacturing, they enhance performance by ensuring that the bolts holding critical engine components don’t shear off under vibration, thereby maintaining engine integrity and boosting vehicle longevity.
Trust in the quality of M12 thick washers should be paramount. Reliable suppliers provide washers that adhere to industry standards such as ISO and DIN. Always verify certifications and the reputation of manufacturers. A trusted supplier will offer comprehensive documentation of material properties and standards compliance, ensuring that the components are tested for diverse applications.
In conclusion, the M12 thick washer is more than just a functional component; it is a strategic choice that embodies engineering precision and reliability. Understanding its roles and specifications can significantly impact the efficiency and safety of an assembly in which it is used. Whether it's safeguarding against mechanical failure in complex machinery or contributing to the stability of a towering structure, the importance of choosing the right M12 thick washer cannot be overstated. Informed decisions backed by professional advice and quality assurance are essential to harnessing the full potential of this seemingly simple, yet indomitably crucial hardware component.