Spring washers and plain washers are vital elements in the realm of fasteners, playing crucial roles in ensuring durability and reliability in various applications. Understanding their distinct functionalities can significantly impact the performance and longevity of mechanical assemblies.
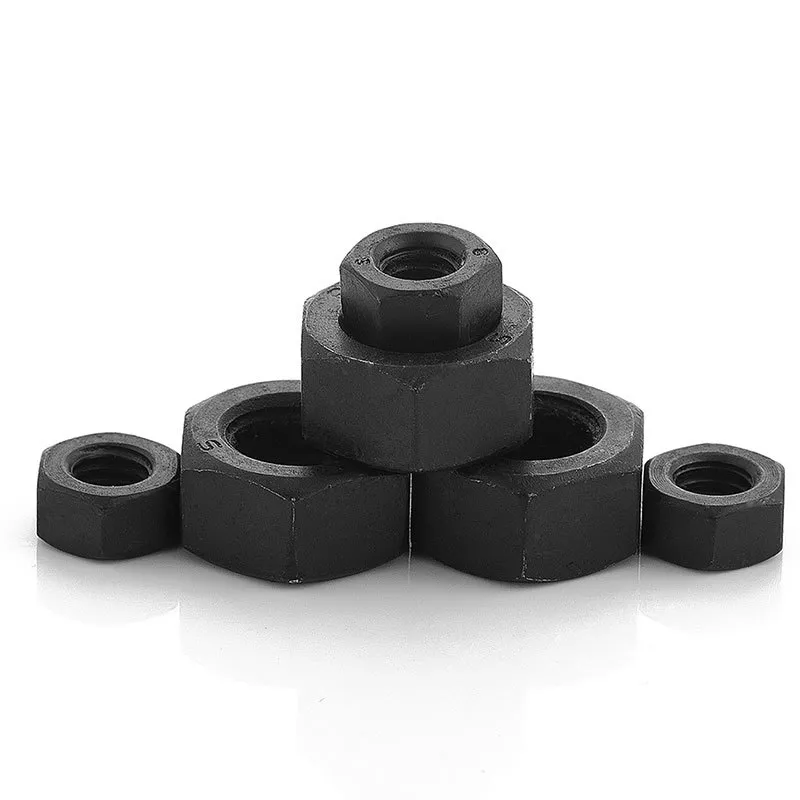
Spring washers, sometimes known as disc springs, are specially designed to exert a load or maintain a desired amount of tension in various assemblies. These washers are typically made of materials with elastic properties, such as high-carbon steel or stainless steel, allowing them to compress under load and then return to their original thickness when the load is removed. This characteristic makes them highly suitable for applications where a tight fastening is essential, and loosening due to vibrations or thermal expansion-contraption cycles could lead to significant issues.
One of the most notable types of spring washers is the Belleville washer, known for its conical shape that provides an axial load even with limited space. These washers are ideal for use in applications with dynamic loads or where bolt tension might fluctuate. Wave washers, another variant of spring washers, are beneficial in absorbing shock and providing a preload between surfaces. They work excellently in applications where space constraints necessitate a low-profile washer that can still deliver the required amount of compression load.
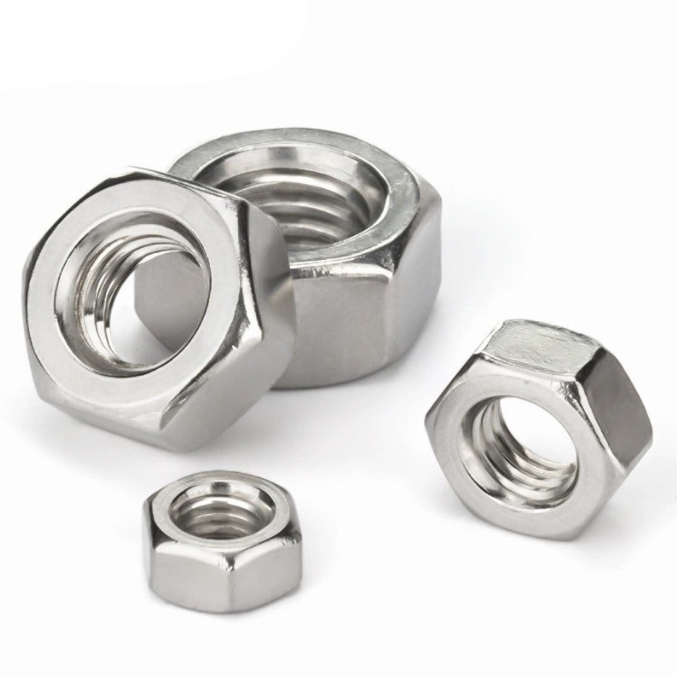
Plain washers, on the other hand, are the unsung heroes of the fastening world, often more straightforward but no less critical. These flat, disc-shaped components serve mainly to distribute the load of a threaded fastener, like a bolt or nut. By spreading the load, they protect the surface of the joint from damage, which could occur if the fastener were tightened directly against it. Additionally, they provide a smooth surface for the fastener to turn against, reducing the chances of loosening due to friction.
Choosing between spring washers and plain washers depends largely on the specific needs of the project. For instance, in environments subjected to vibration, the locking capability of spring washers can prevent severe damage and costly maintenance. In contrast, in assemblies where a broad distribution of force is required to protect delicate surfaces, plain washers are indispensable.
spring washer plain washer
The credibility and performance guarantees of these components are often backed by rigorous standards set by authoritative bodies. For instance, the American Society of Mechanical Engineers (ASME) and the International Organization for Standardization (ISO) provide comprehensive guidelines ensuring that washers meet certain mechanical and material requirements. Adhering to these standards is imperative, not just for quality assurance but also for maintaining trustworthiness in engineering practices.
Moreover, the importance of expertise when selecting materials for these washers cannot be overstated. Factors like corrosion resistance, tensile strength, and fatigue life are key considerations that should align with the application's requirements. For example, stainless steel spring washers are preferable in humid or corrosive environments due to their enhanced resistance to rust and wear. Similarly, in high-temperature applications, materials like Inconel may be chosen for their superior ability to withstand thermal stresses.
Real-world experiences demonstrate the profound impact that the right washer can have on assembly integrity. For instance, in automotive applications, using the correct spring washer can prevent parts from loosening due to engine vibrations, significantly enhancing vehicle safety and performance. In electronics, where space is often at a premium, wave washers can offer efficient load distribution without compromising on assembly compactness.
In conclusion, both spring washers and plain washers serve distinct, but equally important roles in securing fastener assemblies. Their appropriate selection, based on robust expertise and standardized guidelines, ensures both enhanced product performance and reliability. This understanding not only empowers engineers and designers with the confidence needed to tackle complex design challenges but also assures consumers of the durability and safety of the products they depend on. By embracing the nuanced roles of these components, industries can optimize their mechanical systems for peak efficiency and longevity.