Weld nuts, essential components in various manufacturing processes, offer remarkable versatility and reliability. These specially designed nuts are used in numerous applications, from automotive to construction, and are known for their ability to be permanently affixed to a workpiece through welded attachments. Their significance is often highlighted by experts in the field of engineering and manufacturing, who attest to their durability and efficiency in fastening applications.
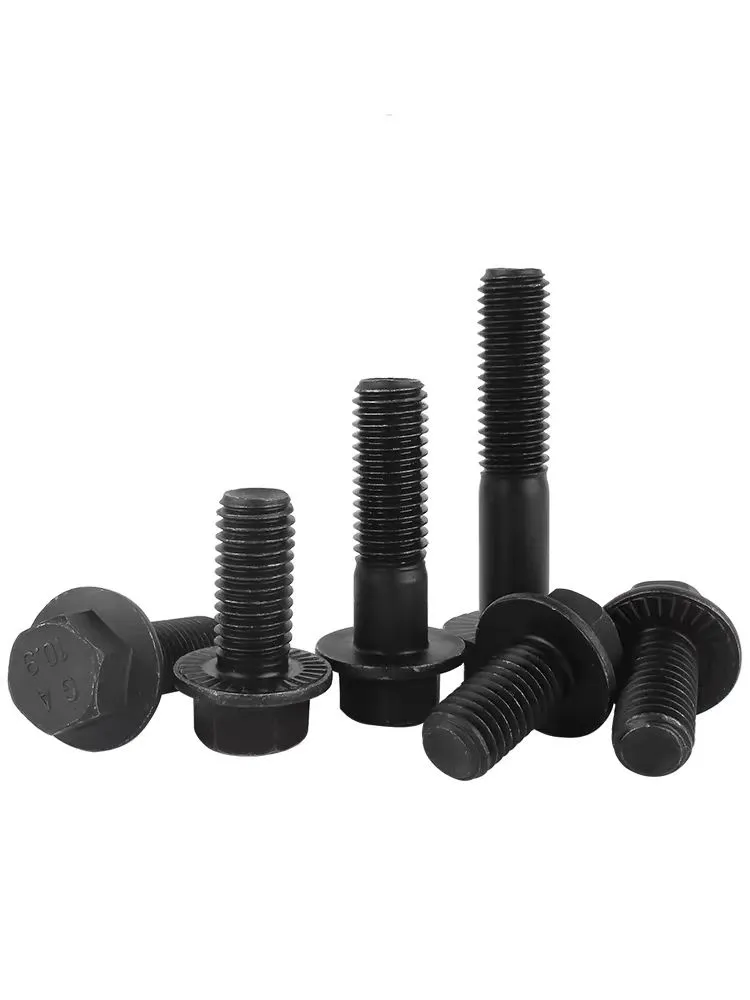
From an experience standpoint, weld nuts offer nuanced advantages to professionals who handle projects requiring strong and reliable joining solutions. For instance, in the automotive industry, weld nuts are employed to ensure secure mounting points for car components. Veteran engineers and mechanics appreciate how these nuts withstand vibrations and the rigorous stresses of everyday vehicle operation. The consistency and permanence provided by weld nuts surpass what traditional fasteners can achieve, providing an assurance that the assembly remains intact over time.
Expertise in the field reveals that weld nuts are available in various styles and materials, catering to different environmental and project-specific requirements. Experts often recommend steel or stainless steel variants for their excellent tensile strength and corrosion resistance, ensuring longevity even in harsh conditions. Moreover, selecting the right style of weld nut—be it hex, round, or flange—can significantly enhance the success of a project. For example, flange weld nuts are commonly used where a wider base is required to distribute load over a larger surface area, minimizing the risk of material fatigue.
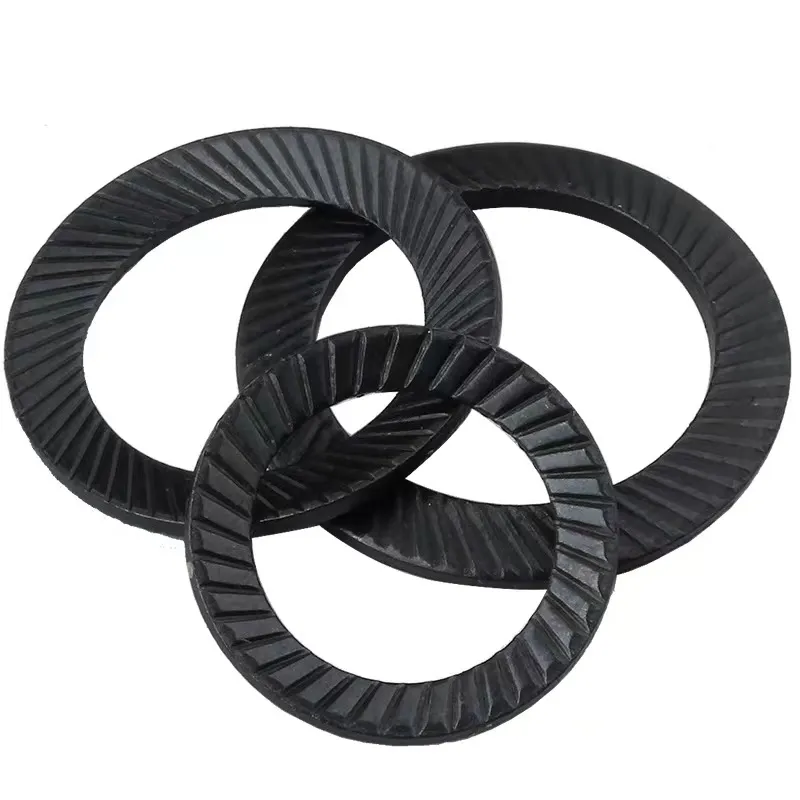
Authoritative sources in manufacturing engineering emphasize the critical nature of proper installation techniques when using weld nuts. A misstep in the welding process can compromise the integrity of the joint, leading to potential project failures.
Thus, adherence to precise welding standards is crucial. Organizations and industry bodies continually update guidelines to incorporate advancements in welding technologies, ensuring that practitioners have access to the most current and effective practices.
weld nuts
Trustworthiness in discussions around weld nuts stems from rigorous testing and quality assurance processes that these components undergo before reaching the market. Certified weld nuts often conform to international standards such as ISO or SAE, providing users with confidence in their performance. Manufacturers undergo strict quality control, subjecting weld nuts to tests that simulate real-world stresses and environmental conditions, further establishing their reliability.
The trend towards sustainable and eco-friendly manufacturing processes also sees weld nuts playing a significant role. By enabling disassembly and recycling of components at the end of life, projects that incorporate weld nuts can significantly reduce environmental impact. This sustainable aspect appeals to conscientious manufacturers looking to minimize their ecological footprint while maintaining top-notch quality in their products.
Real-world experiences, expert recommendations, and adherence to authoritative practices collectively underline the importance of weld nuts in manufacturing. From enhancing the structural integrity of projects to offering environmentally responsible solutions, weld nuts are an indispensable element of modern engineering. By understanding their application, selecting appropriate materials and styles, and following industry best practices, professionals can effectively leverage weld nuts to achieve superior results, reinforcing their status as reliable and essential components in the world of fastening.