Weldable washers have been an integral component in various industries, offering both practicality and innovation. These small yet indispensable items secure fastenings, ensuring structural integrity and offering solutions where traditional washers might not suffice. Having spent over a decade in the metal fabrication industry, I have witnessed firsthand the versatility and essential nature of weldable washers in a multitude of applications.
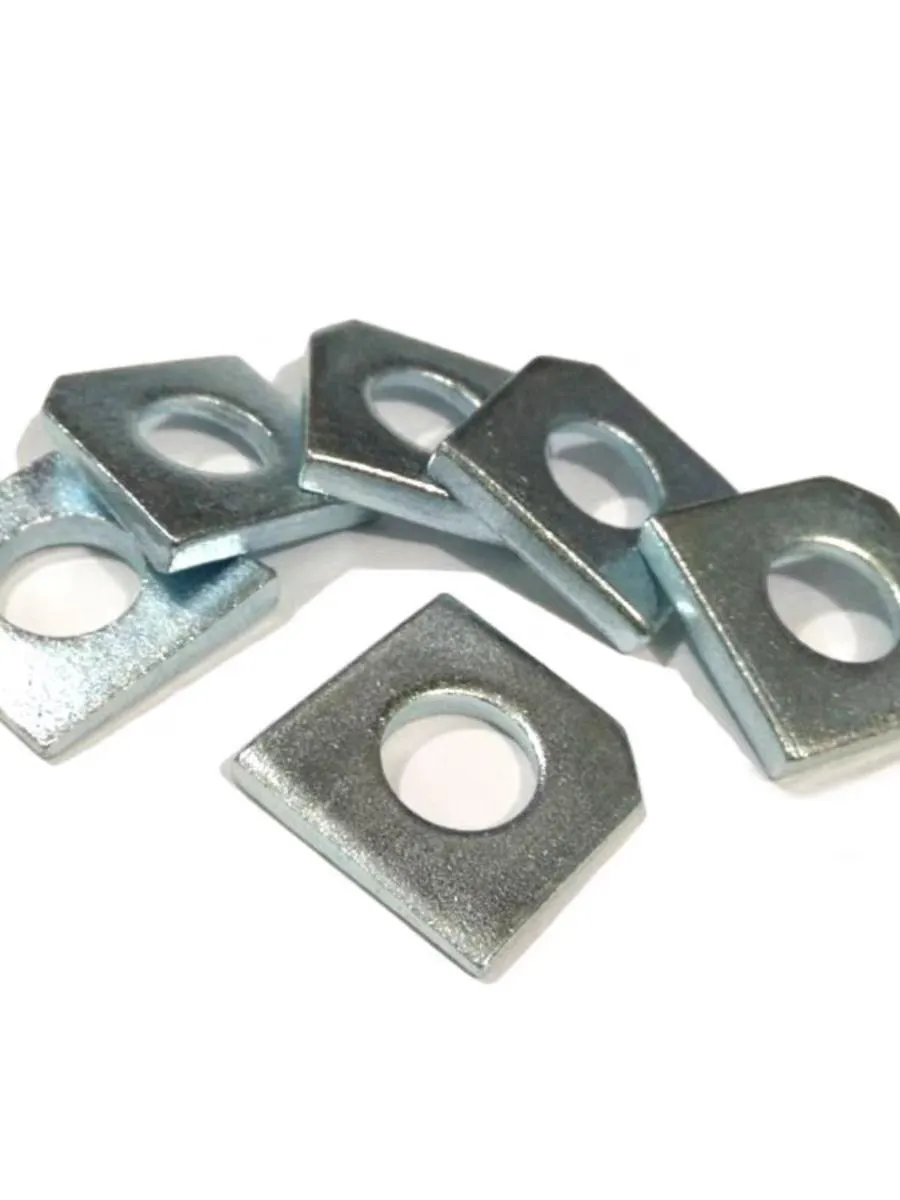
Originally crafted from the need to provide durable fastening solutions in complex assemblies, weldable washers are designed to integrate seamlessly into metal structures. Their ability to be permanently affixed through welding allows for a more reliable fastening solution, especially in applications subject to vibration or movement. This is particularly beneficial in automotive and aerospace industries where stability and security are paramount.
One of the defining advantages of weldable washers is their contribution to enhancing joint strength. Unlike typical washers that depend solely on the tension of the bolt, weldable washers actively participate in distributing load forces across a broader surface area. This added distribution mitigates potential stress points that could lead to material fatigue over time, a critical consideration in high-stress environments.
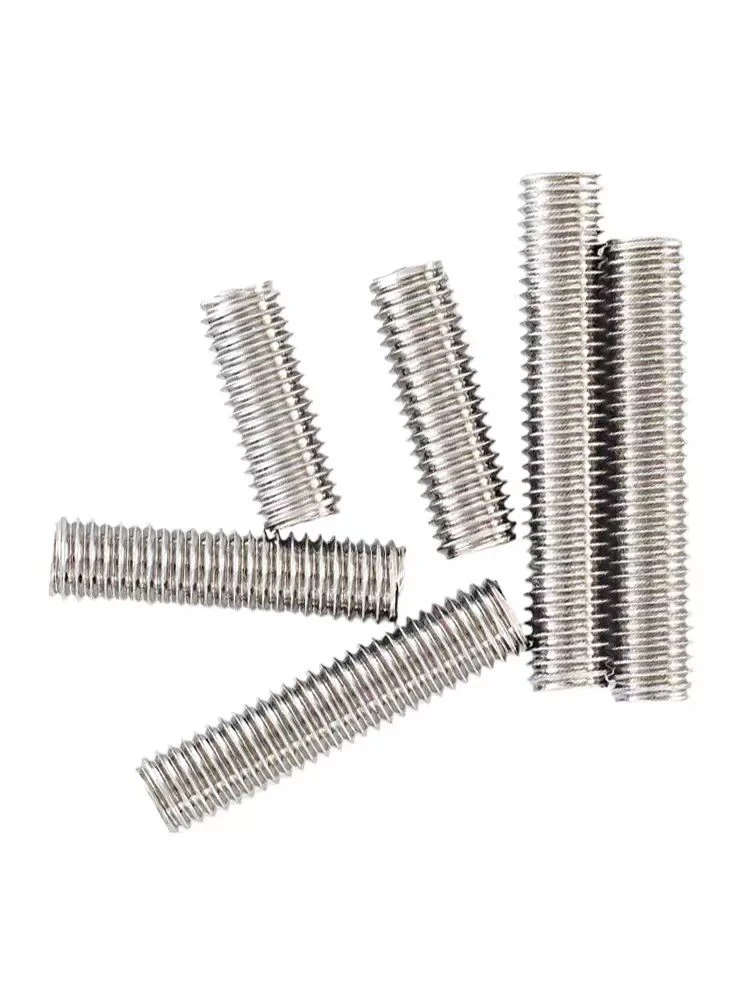
From an engineering perspective, weldable washers offer a unique blend of ease of use and robust performance. Their installation is straightforward; once positioned, they can be welded directly to the structural component, ensuring a permanent, vibration-resistant fix. This process eliminates the need for additional fasteners, reducing both weight and installation time—a crucial factor in industries like aerospace where every gram counts.
Materials science has played a significant role in the evolution of weldable washers. Often constructed from stainless steel or carbon steel, these washers are engineered to withstand corrosion and extreme temperatures, providing longevity and reliability under harsh conditions. Furthermore, advancements in metallurgical processes have allowed for customization, with manufacturers able to produce washers in various dimensions and specifications to meet specific application needs.
weldable washers
Addressing the need for sustainability, many manufacturers are now looking into recyclable materials and eco-friendly production methods for weldable washers. This shift not only decreases the carbon footprint but also aligns with global initiatives towards greener manufacturing processes.
In terms of expertise,
installing a weldable washer requires precise execution. The welding process must be performed by skilled professionals to ensure that the washer maintains its structural integrity and functionality. Poorly executed installations can lead to weld failures, compromising the entire assembly. Therefore, proper training and experience are essential to harness the full benefits of these components.
Authoritativeness in the field of weldable washers is often demonstrated by manufacturers with a longstanding presence in the market. Companies that have invested in research and development tend to offer products that outperform generic alternatives. These manufacturers often provide detailed technical data and support, aiding engineers and designers in making informed decisions.
The trustworthiness of a weldable washer is largely determined by its track record in rigorous applications. Customer testimonials and case studies serve as valuable resources, offering insights into real-world performance and reliability. For those considering incorporating weldable washers into their designs, liaising with industry professionals and consulting case studies can offer reassurance on their decision.
In summary, weldable washers represent a fusion of practical design and engineering innovation. Their contribution to load distribution, reduction of stress points, and reliable performance makes them indispensable across various demanding sectors. With continual advancements in materials and a shift towards sustainable manufacturing, weldable washers are set to remain at the forefront of fastening technology, supporting the evolving needs of modern industry.