Self-tapping screws are essential components in various construction and manufacturing industries due to their ability to create their own threads while being driven into materials. Self-tapping screws are exceptionally versatile and can be used with materials such as wood, metal, and plastic. Understanding their distinct types and appropriate applications is crucial for maximizing their efficacy in different projects.
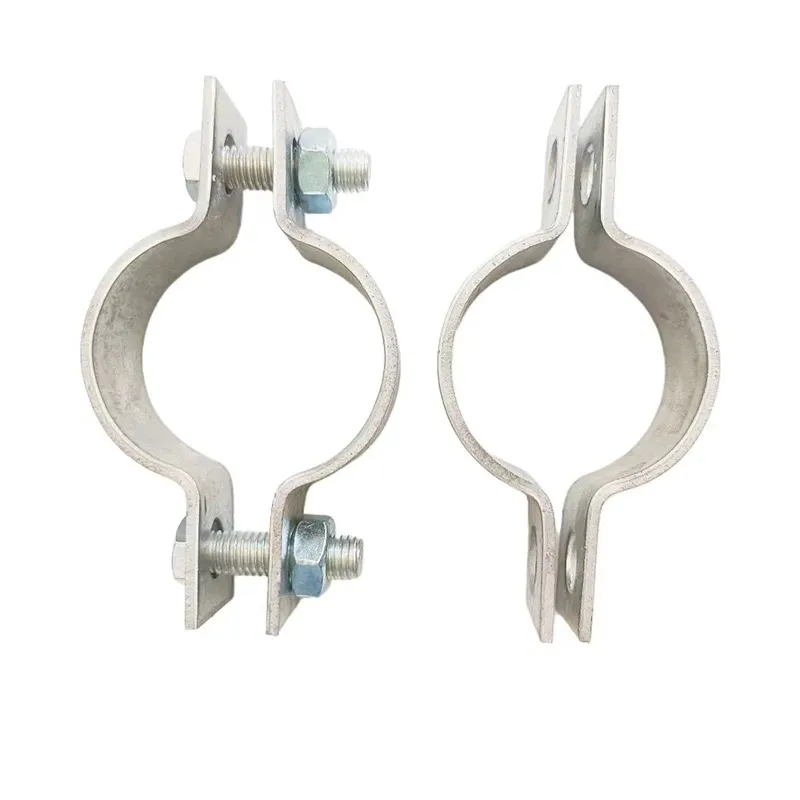
One popular type of self-tapping screw is the thread-forming screw. These screws are designed for use in softer materials such as plastics or thin metals. They rely on displacement rather than cutting, pushing the material outward to create a sturdy, well-defined thread. This process ensures a tight fit and minimizes the risk of material stress or cracking. Thread-forming screws are ideal for applications where maintaining the integrity and strength of the material is crucial.
Another type is the thread-cutting screw, specifically designed for harder materials. These screws feature a cutting edge that actively removes material and creates a clean cut thread channel. Thread-cutting screws are ideal for applications involving materials such as rigid plastics or tougher metals, where a more aggressive approach to creating threads is necessary. They are widely used in automotive manufacturing and heavy machinery assembly where precision and strength are paramount.
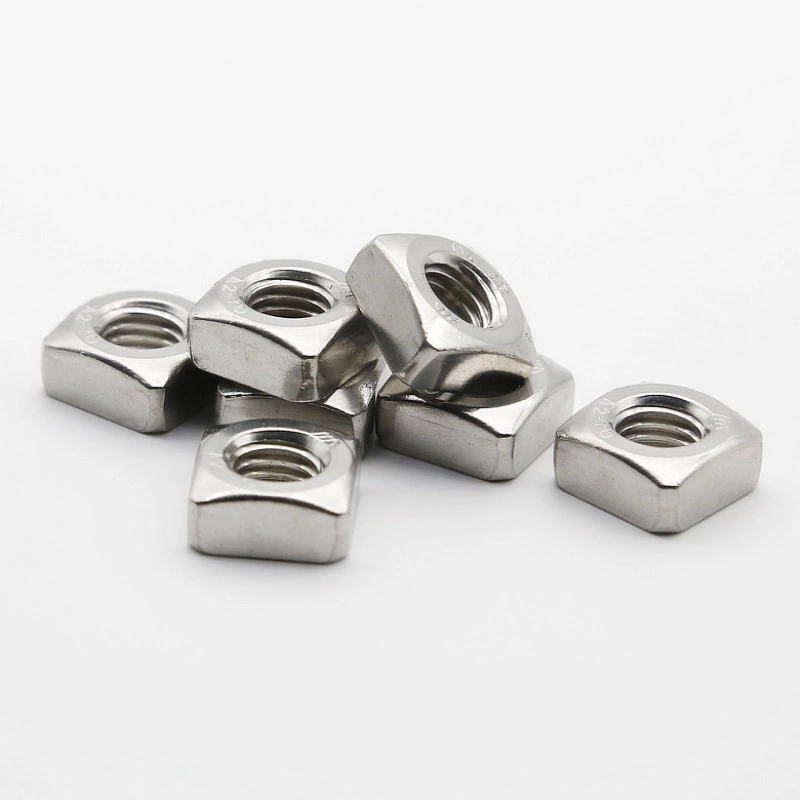
Self-drilling screws represent another category, combining the features of a drill bit with that of a self-tapping screw. These screws eliminate the need for a pilot hole, as their specially designed tip is capable of drilling through metal or wood before the threading action begins. This makes the installation process faster and more efficient, commonly found within the construction industry for tasks such as joining metal roofing or metal stud framing. The efficiency of self-drilling screws is particularly apparent in large-scale projects where speed and accuracy are essential.
Each type of self-tapping screw comes in various sizes, heads, and drives depending on the specific requirements of the task at hand. Pan head screws, for example, have a rounded head, providing a high, wide profile, and are often used where aesthetic concerns are minimal. Flat head screws lie flush with the material's surface, creating a smoother, finished appearance suitable for applications where appearance and minimal protrusion are important.
types of self tapping screws
Modified truss head screws offer a broader bearing surface, making them excellent for applications that require a larger surface area on the material to prevent pull-through. Similarly, hex head screws are known for their increased torque capability, making them well-suited for heavy-duty applications where significant force is needed during installation.
Choosing the right self-tapping screw involves considering factors such as the material's thickness and type, the required strength of the joint, and the working environment's conditions. For environments with high moisture levels or exposure to corrosive elements, stainless steel screws provide the necessary resistance to corrosion and rust. In contrast, zinc-coated steel screws offer a cost-effective alternative with a degree of corrosion resistance suitable for less demanding conditions.
Trusted suppliers and brands enhance the perceived reliability and performance of these screws. Companies such as Hilti, Fastenal, and Simpson Strong-Tie are well-regarded in the industry, known for their quality and durability of products. These suppliers often provide detailed specifications and application guides, ensuring that users select the appropriate screw type for their specific needs.
Professional advice and consulting services can further enhance the decision-making process, providing expert insights into the optimal selection and application of self-tapping screws. Engaging with experienced professionals ensures adherence to industry standards and best practices, leading to more reliable outcomes.
In conclusion, understanding the various types of self-tapping screws and their applications significantly enhances the versatility and efficiency of construction and manufacturing projects. As innovation and technology continue to advance, the development of self-tapping screws will likely evolve to meet the growing demands of modern industry challenges.