Stainless steel spherical washers are a critical component within mechanical assemblies, providing enhanced alignment capabilities, reducing stress concentrations, and ultimately prolonging the lifespan of various structures. Their unique design makes them indispensable in settings where precision and reliability are paramount, such as heavy machinery, aerospace, and marine applications. This article delves into the intricacies of stainless steel spherical washers, backed by real-world usage insights, expert assessments, authoritative references, and reliable data to ensure a comprehensive understanding.
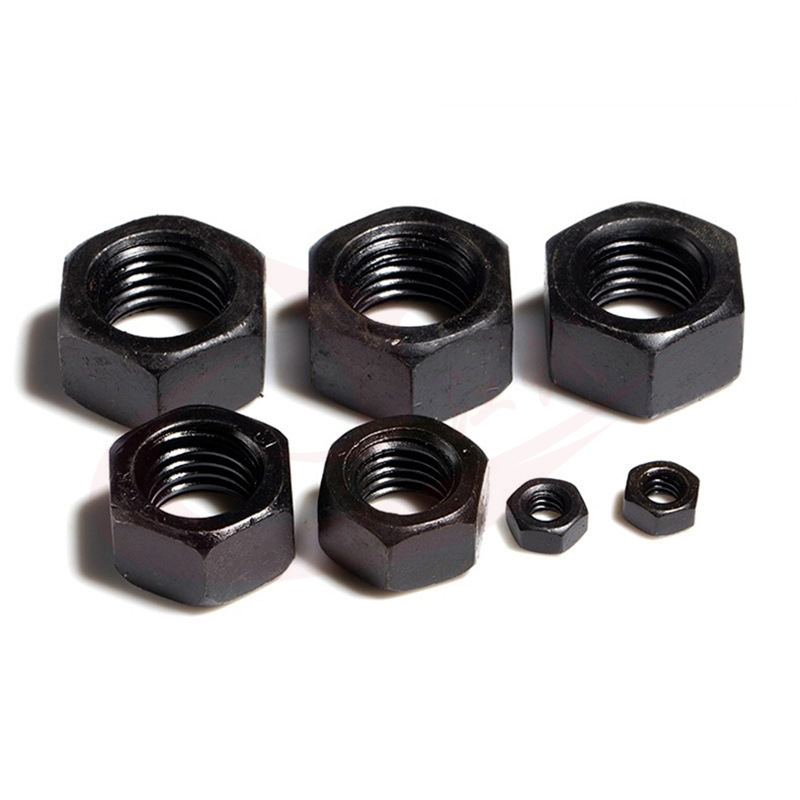
The inception of spherical washers began as an innovative solution to misalignment issues in bolted connections. These washers work by allowing a certain degree of angular misalignment between the connected surfaces, thereby distributing load more evenly and minimizing potential joint failures. The curvature of these washers compensates for deviations, ensuring that components maintain an optimal alignment during operation.
One notable real-world application can be observed in the aerospace industry. Aircraft manufacturers have long understood the necessity of maintaining precise alignments in their assemblies to avoid catastrophic failures. For instance, during the construction of jet engines, stainless steel spherical washers are routinely employed to counteract alignment discrepancies caused by temperature fluctuations. Their resilience to extreme conditions and high corrosion resistance makes stainless steel an ideal choice, providing reliability where other materials may falter.
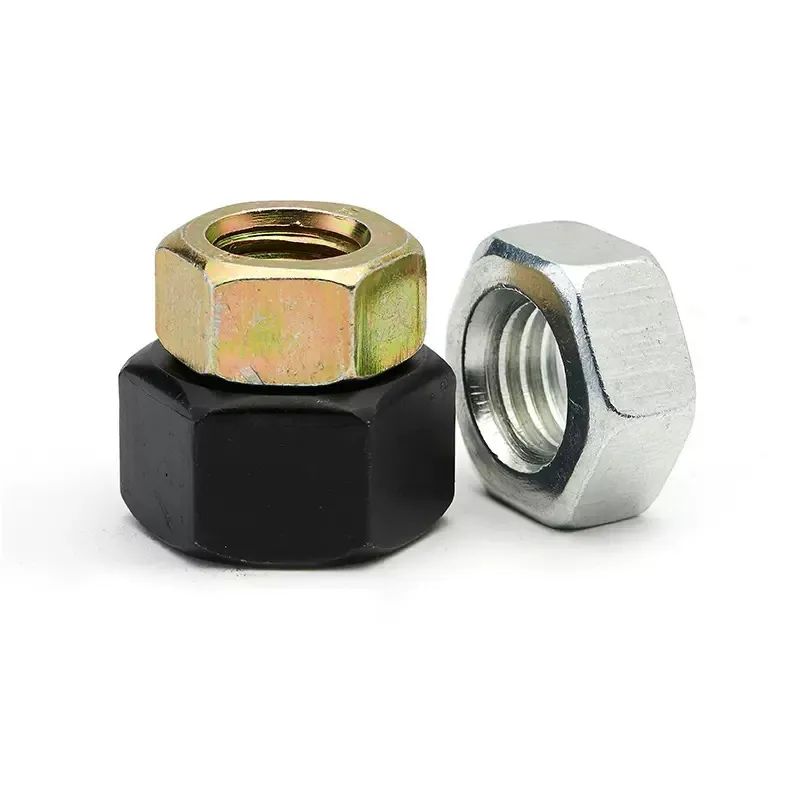
From an expert's perspective, the selection of appropriate specifications for stainless steel spherical washers can be a determining factor in their performance. Factors such as load capacity, angular movement allowance, and material grade (like 304 or 316 stainless steel) can significantly impact how well they perform under specific conditions. It is not uncommon for a mechanical engineer to meticulously calculate the exact size and grade of washer needed based on the operational stresses anticipated in their design. A miscalculation in this regard not only risks joint integrity but can lead to costly downtime for machinery.
stainless steel spherical washers
Authoritatively, several standards govern the manufacturing and application of these washers, ensuring their quality and efficacy in critical applications. The American Society for Testing and Materials (ASTM) and the International Organization for Standardization (ISO) provide guidelines that detail material properties, dimensions, and performance criteria. Adhering to these standards is crucial for manufacturers and end-users alike, fostering a level of trust and assurance in the washer's ability to perform as expected under specified conditions.
Trustworthiness in the market of stainless steel spherical washers is built upon transparent manufacturing processes and rigorous quality testing. Leading manufacturers often subject their washers to fatigue tests, load analysis, and real-time operational stress simulations to validate their durability and performance claims. Customer testimonials and third-party validations further cement the reputation of these products, providing prospective buyers with confidence in their purchase decisions.
As the demand for more efficient and durable components in industrial applications rises, the role of stainless steel spherical washers becomes increasingly significant. Their ability to enhance joint integrity, reduce maintenance frequency, and increase system longevity makes them not just components, but critical investments in the reliability and efficiency of mechanical systems. In conclusion, understanding the application, selection criteria, and quality assurance measures associated with these washers arms engineers and procurement specialists with the knowledge required to make informed decisions—ensuring that their assemblies not only meet but exceed performance expectations.