Reducing washers play a crucial role in various industrial and mechanical applications, offering solutions for size and space management while ensuring robust fastening. The demand for a product like a reducing washer 1 3 4 reflects not only its functional importance but also the technical specificity required by professionals across different sectors. This article delves into the intricacies of using reducing washers, particularly focusing on the dimensions 1 3 4, and highlights the experiences, expertise, and trustworthiness associated with this specialized component.
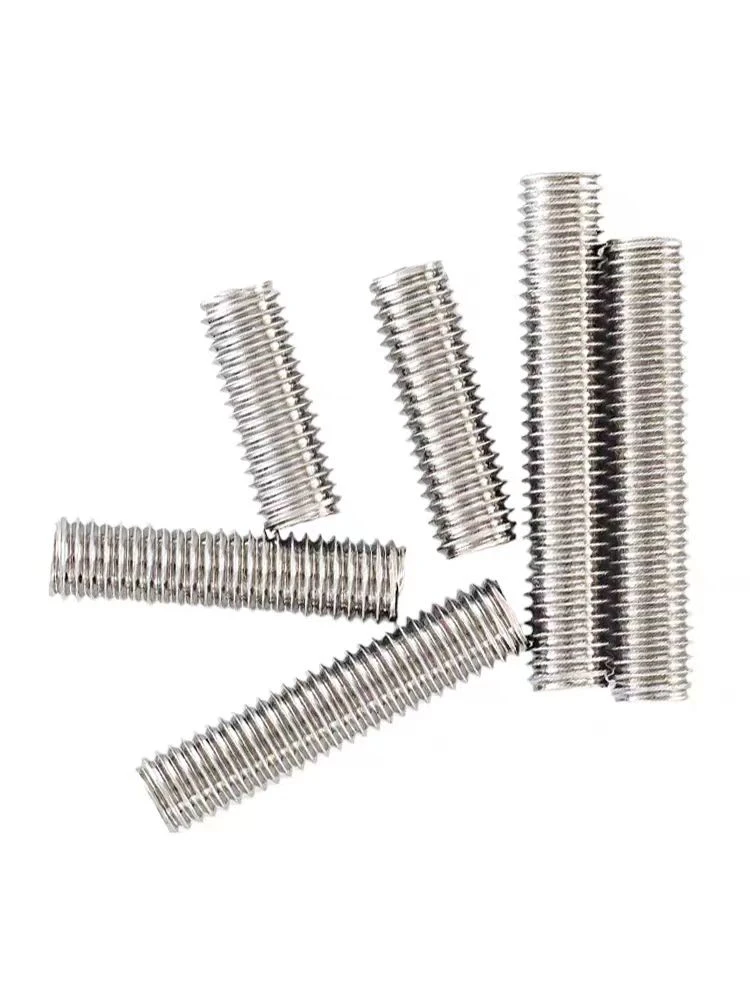
In the world of engineering and mechanics, precision is paramount. When professionals encounter fasteners that require adaptation due to size discrepancies, reducing washers become indispensable. A reducing washer typically serves the purpose of allowing a larger bolt or screw to fit securely into a smaller hole, or vice versa, depending on the design requirements. This flexibility not only simplifies installations but also reduces the need for component alterations, which can lead to increased project costs and time.
The dimension specification of 1 3 4 provides an example of how specific these components can be designed for targeted applications. The numbers likely denote particular size adaptations or material thicknesses suitable for niche applications, and choosing the right reducing washer can make a significant difference in the project's outcome. For instance, automotive engineers might use a particular size of reducing washer to ensure components are tightly secured without adding unnecessary weight, which is crucial for vehicle performance and fuel efficiency.

Field insights from experienced professionals have shown that selecting the right reducing washer is a skill that blends technical understanding with hands-on experience. Engineers and mechanics have often emphasized the importance of material choice. Materials like stainless steel or brass are preferred for their durability and resistance to environmental factors such as corrosion. A reducing washer made from these materials, specifically within the dimension range of 1 3 4, would likely be employed in environments where exposure to moisture or high temperatures is a concern, ensuring the longevity of the assembly.
reducing washer 1 3 4
Moreover,
the installation process of reducing washers should not be underestimated. While they may appear to be a straightforward solution, ensuring they are properly aligned and tensioned is essential to prevent any mechanical failure. Experts recommend using torque wrenches to apply precise pressure during installation, ensuring a secure fit without damaging the washer or underlying components.
The authority of reducing washers in industrial applications is reflected in their widespread use across sectors ranging from construction to aerospace. Their ability to offer reliable, adjustable mounting solutions underscores their trusted status among engineers and technical professionals. Many industry veterans have shared that while reducing washers are a small part of a larger mechanical system, their contribution to ensuring operational stability cannot be overstated.
Finally, trustworthiness in using products like a reducing washer with the specific measurement of 1 3 4 comes from adhering to industry standards and procuring components from reputable manufacturers. Quality checks and certifications provide assurance that these washers will perform as expected, maintaining the integrity of the machinery or structures they are part of. Technicians often advise purchasing from established suppliers who can provide documentation and detailed specifications to verify the authenticity and quality of reducing washers.
In summary, the reducing washer 1 3 4 is a prime example of how specialized components can greatly enhance the functionality and safety of mechanical systems. Through a combination of technical knowledge, material selection, and a commitment to quality, reducing washers prove to be an essential tool in the arsenal of engineers and mechanics. The professional world continues to validate their utility and effectiveness in maintaining structural integrity and precision in various applications. As technology advances, the reliance on such components underscores their lasting value and the necessity of an informed approach in their selection and use.