Plain washers, often overshadowed by their more complex counterparts in the world of fasteners, play a pivotal yet understated role in countless applications across various industries. Known to many by the DIN standard, these seemingly simple components are anything but trivial. Their unassuming design masks a host of features that lend them to providing durability, stability, and reliability in both everyday and heavy-duty uses.
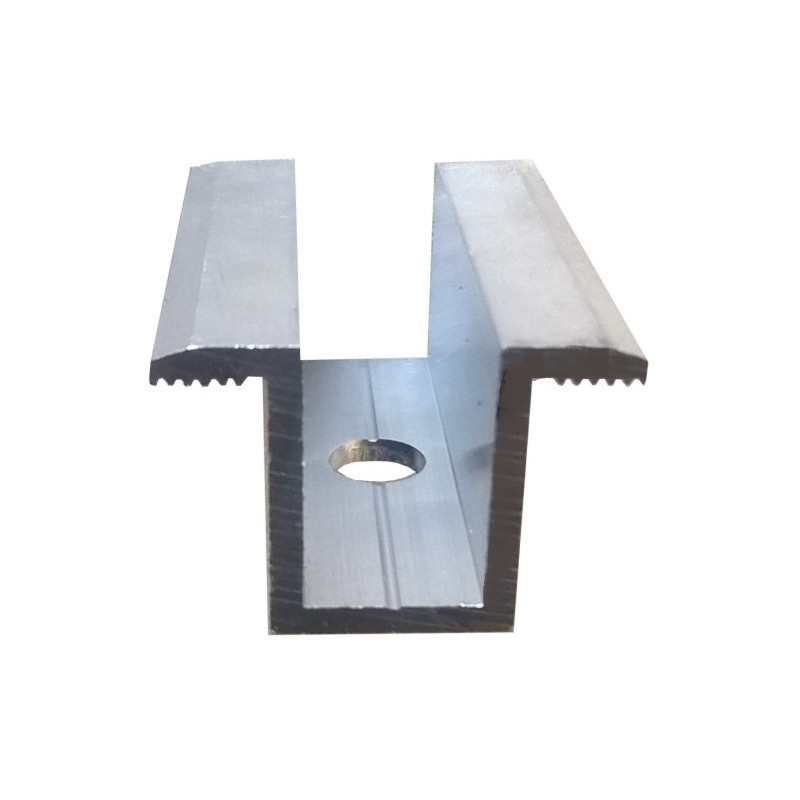
The DIN standard, a widely recognized system originating from Germany, stands as a benchmark for quality and uniformity in the manufacturing world. Ensuring that plain washers conform to this standard guarantees a level of sophistication and reliability that industries, ranging from automotive to construction, rely upon. One might wonder what sets these washers apart from others in the toolkit, so let's delve into what makes plain washers DIN an essential component.
At their core, plain washers serve a very specific purpose they distribute the load of a threaded fastener, such as a bolt or a nut, more evenly over a surface area. This functionality is crucial in preventing damage to the materials being joined as well as ensuring that the fastener achieves a more secure fit. Without the mediating presence of a plain washer, a fastener might dig into softer materials, causing deformation or even failure of the entire assembly.
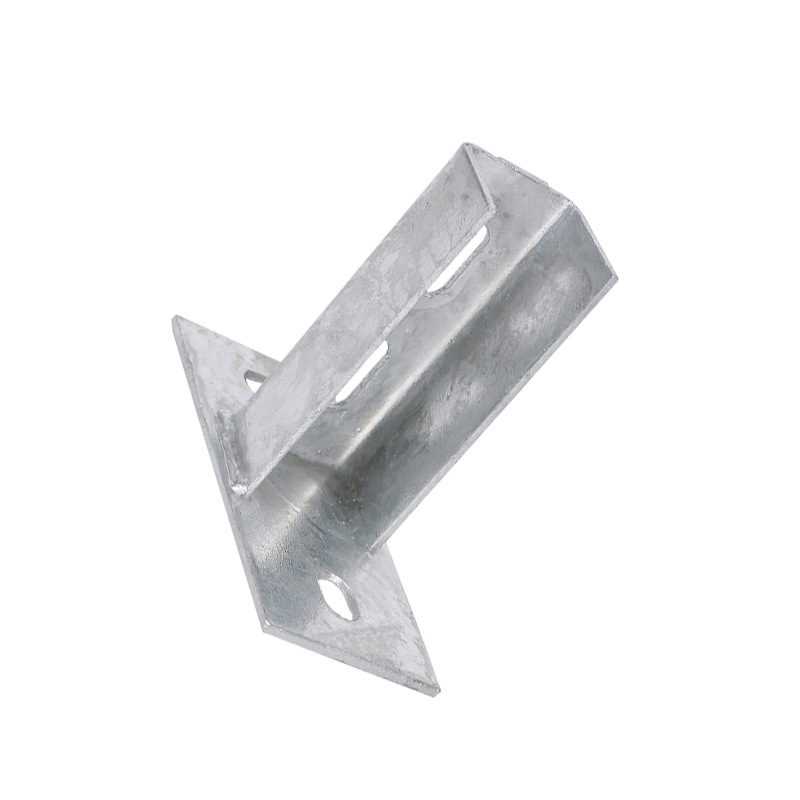
Experience has shown that the strategic use of plain washers can significantly extend the lifespan of mechanical assemblies. For instance, in the automotive industry, where vibrations and thermal expansions are constant, plain washers are indispensable. They provide a buffer that absorbs some of the vibrations and expansions, preserving the integrity of fastened joints. Real-world application tests have shown a marked improvement in the longevity and reliability of assemblies that incorporate DIN standard plain washers compared to those that do not.
plain washer din
From an expertise perspective, choosing the right type of plain washer involves understanding the specific attributes of your application, such as the type of load and environmental conditions. For high-temperature environments, for instance, washers made of specific alloys or materials resistant to thermal degradation are recommended. Similarly, in corrosive environments, stainless steel plain washers or those with special coatings are necessary to prevent rust and maintain structural integrity. Engineers and product designers often rely on the highly detailed specifications provided by the DIN standards to select the correct washer type, ensuring optimal performance.
In terms of authoritativeness, DIN standard washers command respect globally due to their rigorous testing and consistently high quality. The DIN certification process involves numerous mechanical and chemical tests that verify a washer's load-bearing properties, resistance to wear, and environmental tolerance. This level of scrutiny provides end-users with the confidence that when they see a washer labeled plain washer DIN, they are using a product that adheres to the highest standards of manufacturing excellence.
Trustworthiness emanates not only from adherence to the stringent DIN standards but also from the track record of the manufacturers who produce these washers. Leading companies in the market have decades of experience and invest in continuous research and development to improve their products' performance. Additionally, quality control measures ensure that every lot produced can be traced back for accountability, should any issues arise.
This transparency enhances trust among consumers and professionals alike.
In conclusion, plain washers DIN are more than just pieces of metal with a hole in the center; they are crucial components that integrate seamlessly into the products we rely on every day. Their role in enhancing the performance, safety, and durability of mechanical assemblies cannot be overstated. By choosing DIN standard plain washers, industry professionals ensure they adhere to a legacy of precision and reliability while addressing modern engineering challenges. As more industries recognize the inherent value in these components, plain washers continue to assert their importance across a variety of applications, standing firm as the unsung heroes of the mechanical world.