MS spring washers, often underrated, are pivotal components in various mechanical assemblies, ensuring that fasteners remain secure under dynamic loads and conditions. Their ability to maintain tension and provide a cushion of sorts makes them indispensable in many industrial applications. Understanding their evolution, usage, and benefits is crucial for engineers, designers, and procurement specialists.
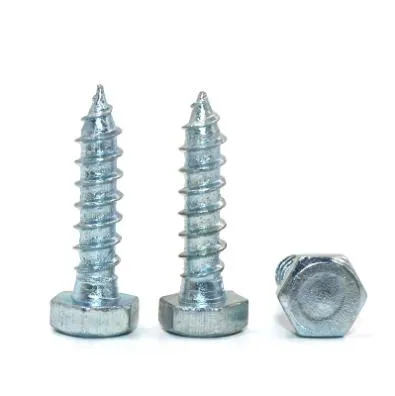
The inception of spring washers dates back decades and has seen significant advancements, primarily in materials and design. Today, MS spring washers, made from medium-strength alloy steel, are favored for their versatility and performance in high-stress applications. Their unique design, which features a slightly conical shape, enables the washers to exert a uniform spring force. This attribute is critical in applications where vibration and thermal expansion could potentially loosen fasteners.
One of the most significant advantages of MS spring washers is their ability to absorb and distribute energy. When a load is applied to a fastener, these washers compress slightly, creating a spring force. This force acts in the opposite direction of the load, countering vibration efforts and preventing loosening. The self-tensioning property is invaluable in sectors like automotive and aerospace, where components are subjected to varying stress levels and environmental conditions.
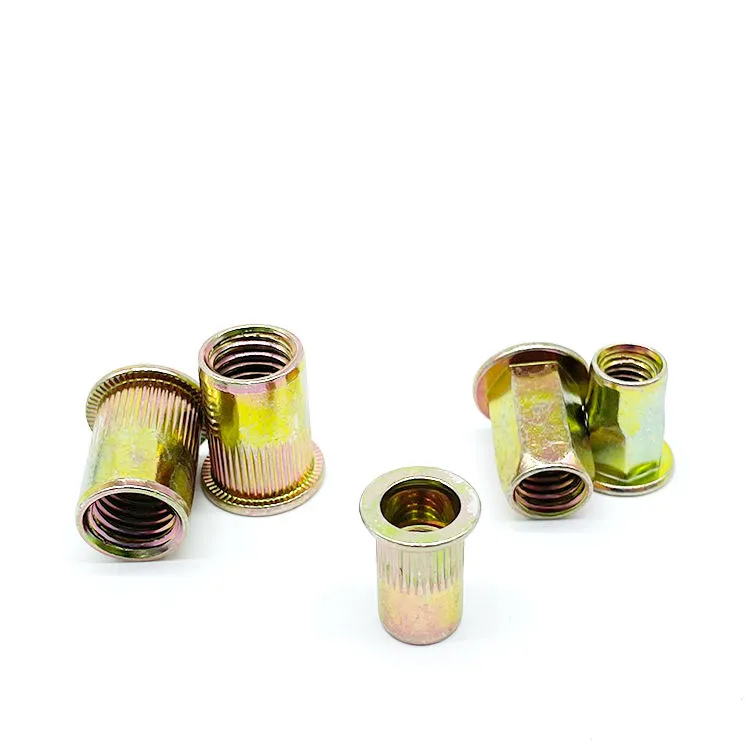
In terms of professional expertise, it's essential to consider the application requirements before selecting a spring washer. Factors such as load-bearing capacity, environmental conditions, and the nature of the materials in contact should guide the choice of washer specifications. Engineers often employ finite element analysis (FEA) to simulate different stress scenarios, ensuring the washer's design and material can withstand operational demands.
Authoritative research underscores the importance of using the correct type of spring washer. For instance, in the automotive industry, where components must endure fluctuating temperatures and constant motion, MS spring washers have been proven effective in maintaining structural integrity and safety. Their resiliency and strength significantly contribute to reducing maintenance costs and preventing catastrophic mechanical failures.
ms spring washer
Trustworthiness in the domain of spring washers is established through adherence to industry standards and rigorous testing. ISO and ASTM provide guidelines that ensure spring washers meet specific mechanical and chemical properties. Reputable manufacturers adhere to these guidelines, conducting repeated quality checks and stress tests on their products. For this reason, partnering with established manufacturers when sourcing spring washers is crucial for maintaining quality assurance.
Moreover, real-world case studies provide substantial evidence of MS spring washers’ effectiveness. In an example from the renewable energy sector, wind turbines utilize these washers extensively. The harsh environmental conditions, combined with constant movement, necessitate a reliable locking mechanism for fasteners. The success in using MS spring washers in such a demanding application speaks volumes about their capability and reliability.
For procurement specialists, understanding the supply chain and potential manufacturers is critical. A transparent supply chain, traceability, and a track record of compliance with industry standards enhance trust and reliability. Sourcing from ISO-certified manufacturers not only ensures quality but also provides a safety net in terms of accountability and support.
In closing, MS spring washers, though simple in design, play a complex role in ensuring the stability and longevity of mechanical assemblies. Their evolution reflects advancements in engineering and material science, while their application across various industries highlights their indispensability. Making informed decisions based on product expertise, professional advice, and authoritative guidelines ensures optimal performance and product longevity.
Ultimately, leveraging these components to their fullest requires a solid understanding of their capabilities and limitations, ensuring that engineering designs achieve desired outcomes while maintaining efficiency and safety. Embracing the complexity of MS spring washers is critical in a world where reliability and precision are paramount.