Metric stainless steel washers are critical components used across various industries, known for their durability, rust resistance, and strength. As any industry professional will confirm, choosing the right type of washer is crucial for long-term project success, especially in sectors where precision and resilience are necessary.
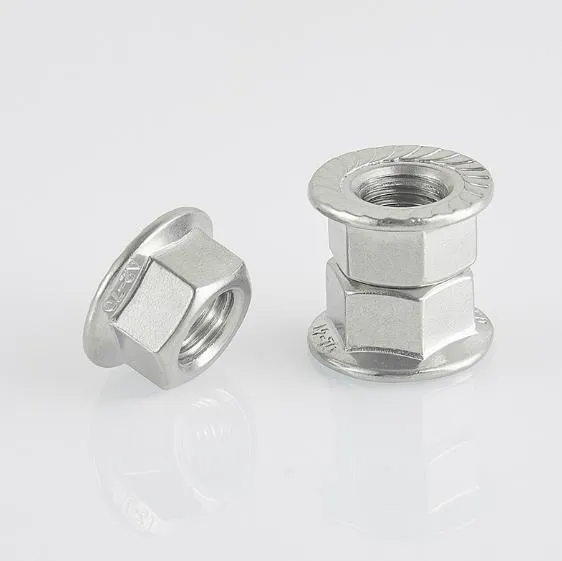
Manufacturers and engineers looking for reliable materials consistently turn to metric stainless steel washers due to their unique properties that address complex application needs. Let's delve into the reasons why these washers remain a preferred choice and explore real-life applications underscoring their significance.
Stainless steel washers come in several types of stainless steel, each of which offers different advantages.
The most commonly used types include 304 and 316 stainless steel. 304 stainless steel washers are incredibly popular due to their corrosion resistance in a wide array of environments. However, for more demanding applications, such as in marine conditions or chemical processing, 316 stainless steel washers offer superior protection against corrosion. This variety allows engineers to select exactly what is needed for specific tasks, ensuring longevity and safety.
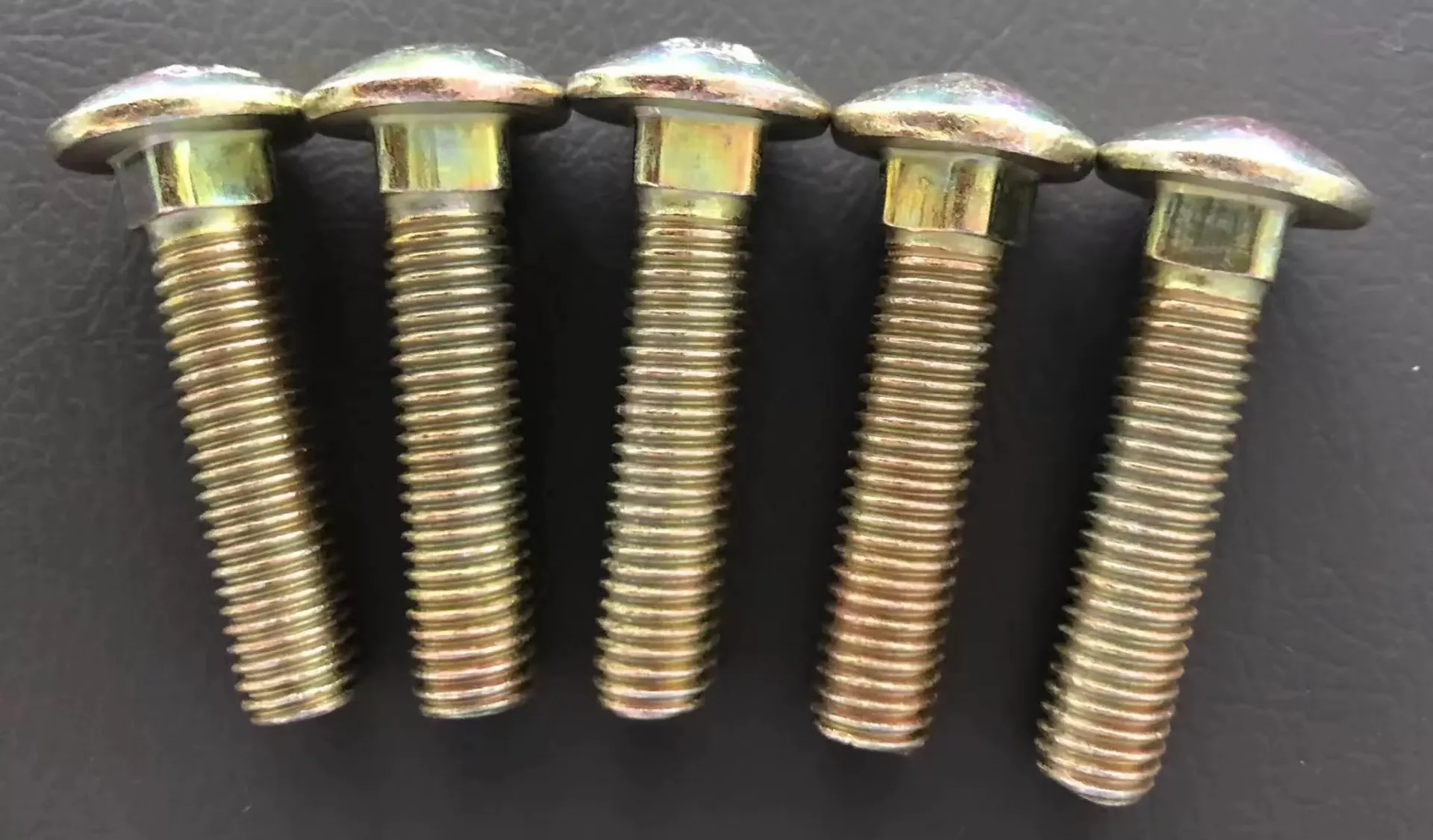
The strength of stainless steel washers means they can withstand significant pressure and force, qualities imperative for construction, manufacturing, and several engineering fields. These industries often deal with heavy machinery and structures where the failure of one component can lead to costly delays or hazards. Given their robust tensile strength, metric stainless steel washers help distribute loads evenly and prevent damage to surfaces by acting as a spacer or load distributor. Experts in structural engineering often emphasize this capability as a reason for their preference.
From automotive manufacturers to aerospace companies, stainless steel washers have presented a trusted solution. In the automotive industry, these washers are key in ensuring the safe and efficient operation of vehicles. For instance, they help in maintaining the integrity of joints subjected to frequent vibration and stress. Automotive engineers frequently share anecdotes about how switching to stainless steel washers resulted in significant improvements in vehicle durability and performance.
metric stainless steel washers
Beyond the technical aspects, metric stainless steel washers also serve as an economical choice in the long run. While the initial cost might be higher compared to inferior alternatives, the long-term savings are substantial when considering their reduced maintenance needs and longer lifespans. In many cases, companies who opted for cheaper materials found themselves facing unexpected repairs, replacements, and operational downtimes—a fact that industry veterans candidly discuss when advising on washer selection.
When it comes to installation and performance under various environmental conditions, stainless steel washers again prove their worth. They can handle extreme temperatures and are less likely to gall (a form of wear caused by adhesion between sliding surfaces), which is a common issue in many industries. This can be particularly advantageous in power generation applications or HVAC systems, where components are exposed to fluctuating temperatures and moist conditions.
Credibility in recommendations grows when real-world usability of stainless steel washers is documented by field professionals. Case studies often highlight that failures due to inferior materials were eliminated when stainless steel variants were used, contributing to fewer interruptions and better business continuity.
In conclusion, metric stainless steel washers are not merely small components; they are pivotal elements that bolster safety, reliability, and efficiency in countless applications. Engineers and industry professionals globally rely on them not only for the immediate benefits they offer but for the confidence that using a proven, trustworthy material brings. This choice reflects an understanding and appreciation of engineering excellence where quality, precision, and performance are non-negotiable.
To sum up, these washers are integral to ensuring seamless and efficient operational capabilities across myriad sectors, making them an invaluable asset in any well-planned engineering or manufacturing project.