Navigating the complexities of selecting appropriate metric flange nuts requires a keen understanding of both the product itself and the applications it is suited for. In an industry driven by precision engineering and secure fastening solutions, metric flange nuts have emerged as indispensable components across various sectors.
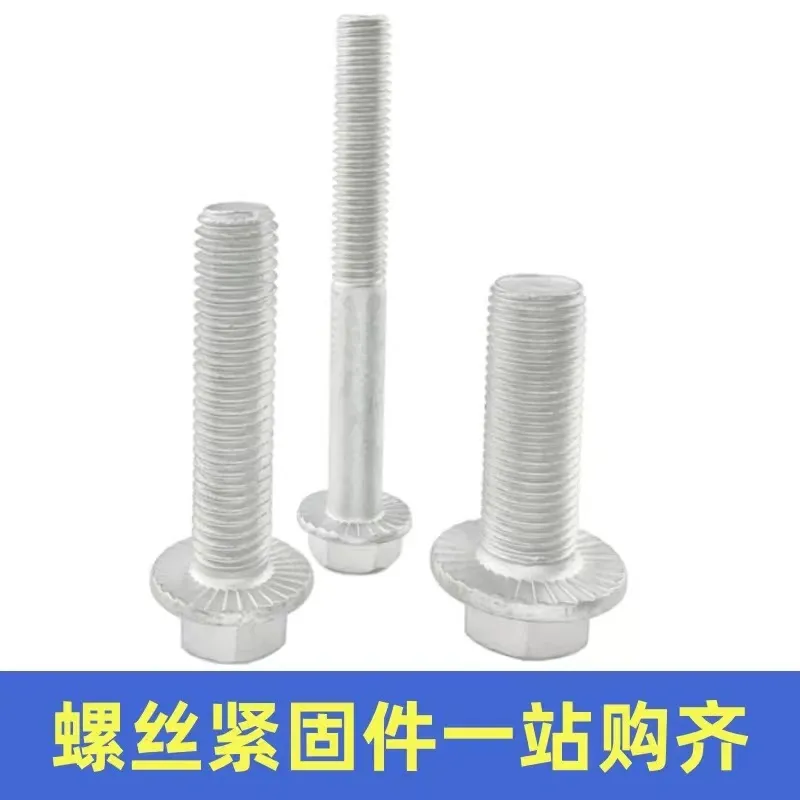
A metric flange nut, primarily distinguished by its wide flange at one end, serves a dual purpose it distributes the pressure of the nut over the part being secured, reducing the risk of damage, and it provides a stable base that helps to prevent the nut from loosening. This multifunctional approach underscores the importance of these components in applications demanding reliability and durability.
The expertise with metric flange nuts lies in their material composition and design specifications. Usually manufactured from carbon steel, stainless steel, or brass, each variant offers different advantages. Carbon steel options are known for their strength, making them a go-to choice in heavy-duty applications. Stainless steel variants, on the other hand, provide superior resistance to corrosion, making them ideal for use in environments exposed to moisture or harsh chemicals. Brass flange nuts, often used in applications requiring electrical conductivity, offer a balance of strength and corrosion resistance.
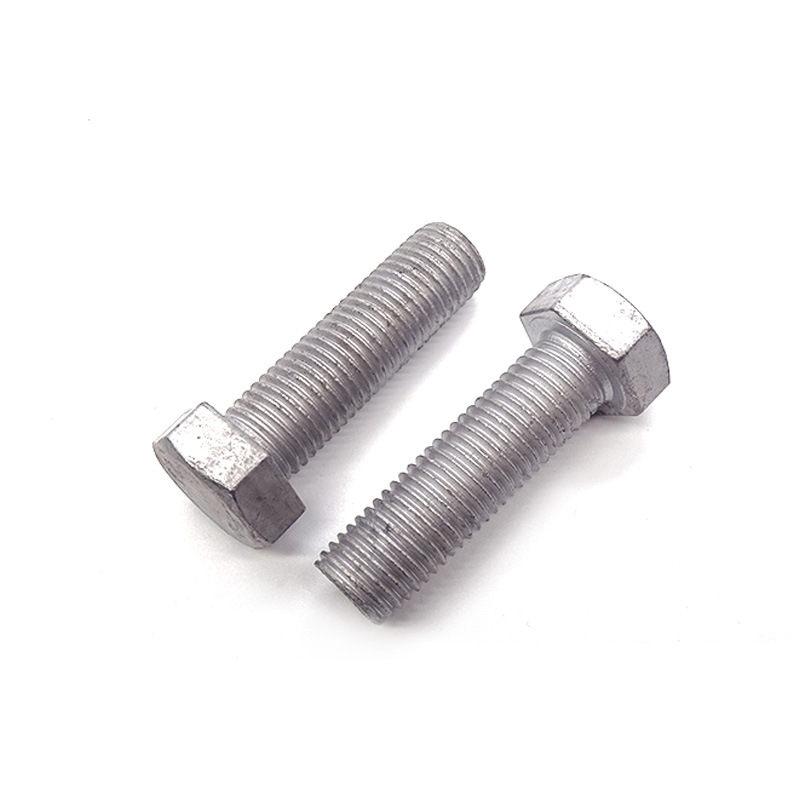
Industry professionals rely on these nuts for a multitude of reasons. The flange itself helps in equal load distribution, which minimizes potential damage to the connected surfaces. This characteristic is particularly crucial in the automotive and aerospace industries, where vibration can pose significant challenges. By choosing the appropriate material and size of the flange nut, manufacturers ensure the integrity of their builds, contributing to a longer lifecycle for their products.
In terms of authoritativeness, the metric flange nut comes recommended by engineers and technicians due to its integrated design which reduces the need for separate washers. The incorporation of the flange into the nut’s body simplifies assembly processes and decreases the time required for installation. In high-volume manufacturing settings, this translates into significant cost savings and increases operational efficiency, a testament to the strategic advantage of using metric flange nuts.
metric flange nuts
The trustworthiness of metric flange nuts further extends into their standards and testing. Often produced in compliance with ISO (International Organization for Standardization) norms, these nuts are subject to stringent quality checks ensuring that they can sustain the specified loads and resist environmental stressors. This compliance reassures engineers and procurement specialists about their choice, knowing the product meets global standards of quality and performance.
Real-world experience affirms the versatility of metric flange nuts. In mechanical assemblies, they are often chosen for their ease of use and reliability. A mechanic working in automotive repair might note the time saved due to the lack of loose washers, which simplifies the process of securing composite materials. Similarly, in industrial machinery maintenance, the robustness of these nuts allows for quicker, less frequent replacements, driving down downtime and maintenance costs.
The continued research and development in the field of fastener technology promise innovations that might further enhance the usability and performance of metric flange nuts. As industries evolve, maintaining high craftsmanship quality while adhering to standards becomes more imperative, leading to even broader applications across emerging markets.
In conclusion, selecting the right metric flange nut involves understanding the specific application requirements, material advantages, and the operational benefits they promise. Their proven track record in high-demand environments sets a benchmark for reliability, making them a staple in any engineer's toolkit.