The importance of choosing the right metric bolts cannot be overstated, particularly for industries and projects that demand precision and reliability. From automotive applications to heavy machinery, metric bolts provide an essential function that can greatly affect the structural integrity and operational efficiency of an assembly. Here’s a comprehensive exploration into the world of metric bolts, emphasizing practical experience, professional expertise, authoritative guidelines, and trustworthy practices to help you make informed choices.
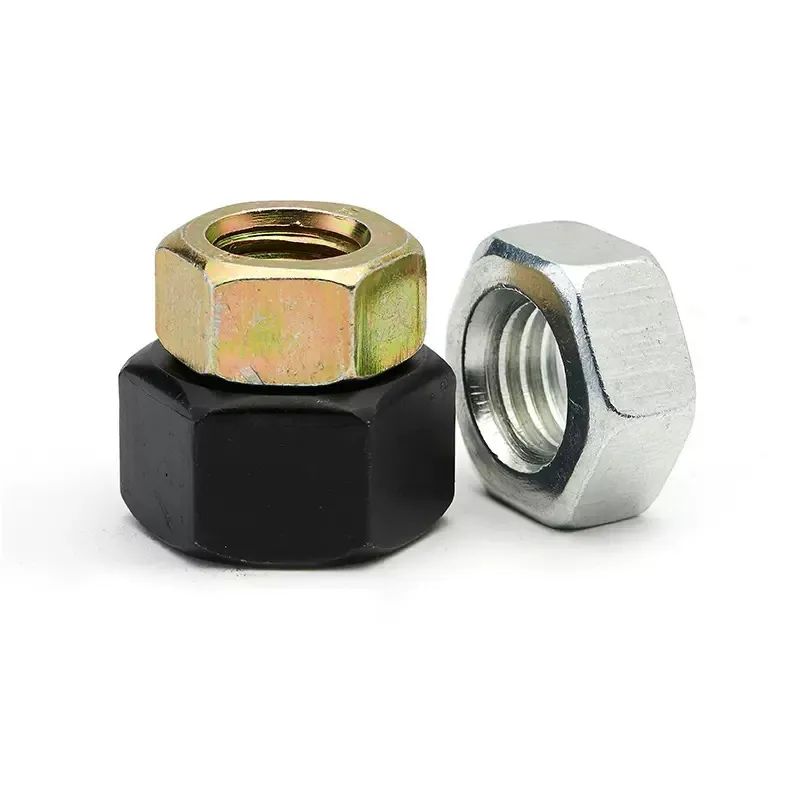
Understanding Metric Bolts An Overview
Metric bolts, commonly used in global engineering projects, abide by international standards often set by ISO (International Organization for Standardization). Unlike their SAE (Society of Automotive Engineers) counterparts, which are measured in inches, metric bolts use millimeters, facilitating interchangeability and compatibility on a global scale. This makes them the go-to choice for multinational operations where consistency is crucial.
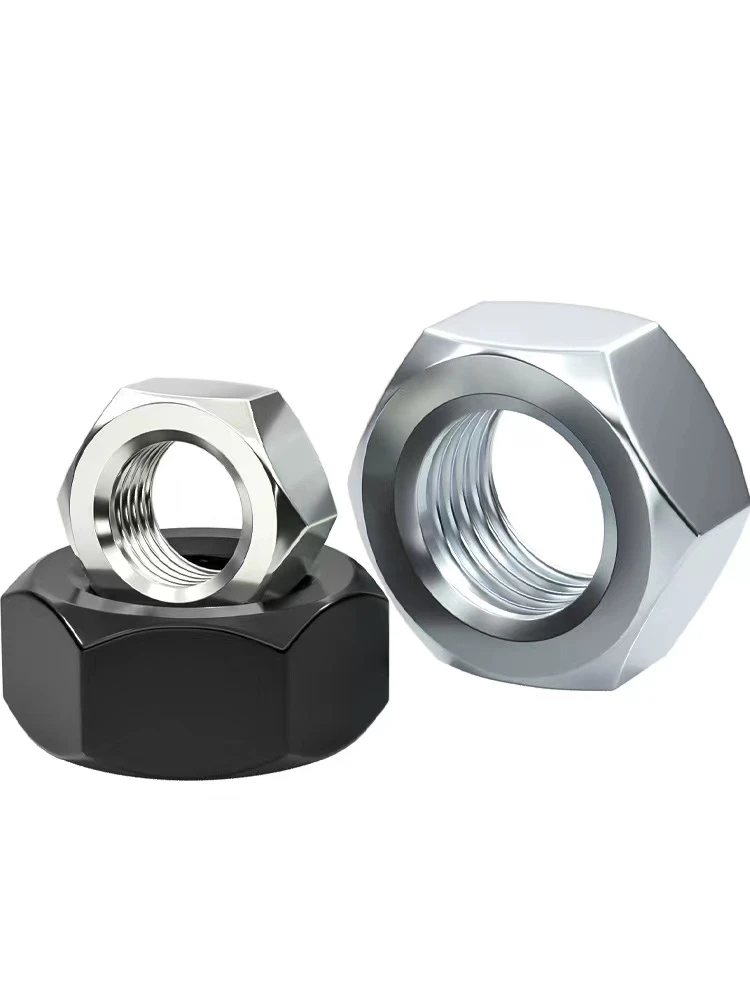
Key Attributes of Metric Bolts
1. Material Composition Choosing metric bolts often starts with selecting the right material. Common options include stainless steel for corrosion resistance, carbon steel for high strength, and alloys for specific requirements in extreme environments. Each material has distinct properties, and selecting the right one can prevent premature failure of the bolt under operational stresses.
2. Thread Pitch and Tolerance Metric bolts are characterized by their thread pitch, which determines the tightness and precision of the fit. Coarse threads are ideal for rapid assembly and disassembly, while fine threads provide superior holding power under vibration. Understanding these differences ensures that the chosen bolts meet the specific demands of the application.
3. Strength Class and Grading Every metric bolt falls into a strength class, such as 8.8, 10.9, or 12.9, signifying its ability to withstand tension and shear forces. Choosing the appropriate grade ensures that the fastener can support the intended load without risking structural compromise. The higher the class, the greater the bolt’s tensile strength.
Applications and Best Practices
Metric bolts are utilized across various sectors—from automotive to construction, aerospace, and beyond. Their design allows for uniform stress distribution and reliable performance under vibrating conditions. When applied correctly, they increase the safety, lifespan, and effectiveness of mechanical assemblies.
1. Automotive Industry In this sector, metric bolts maintain the integrity of engines, transmissions, and suspension systems. Using bolts of improper classification can lead to catastrophic failures, hence the exact specifications according to manufacturer guidelines should be followed meticulously.
2. Construction For structural assemblies requiring long-term durability, metric bolts are chosen for their high resistance to environmental factors. It is crucial for professionals to verify compatibility with building regulations and engineering specifications to prevent any legal or structural fiascos.
metric bolts
3. Machinery and Equipment In heavy equipment, metric bolts need to withstand repeated load cycles without deforming. This requires an assessment of material fatigue properties and regular inspection cycles to ensure ongoing safety.
Authoritative Guidelines and Industry Standards
Industry standards for metric bolts, such as ISO 898 for mechanical properties and ISO 3506 for stainless steel bolts, provide a reliable framework to benchmark quality and compatibility. Adhering to such comprehensive guidelines guarantees not just performance, but also ensures compliance with safety and quality certifications—a critical requirement in many regulated industries.
Building Trust Through Quality Control
Confidence in metric bolt selection is reinforced by adherence to strict quality control processes. These include
1. Traceability Ensuring that each batch of bolts can be traced back to its production line allows for accountability and consistency in quality.
2. Testing and Inspection Rigorous testing under simulated stress conditions exposes potential weaknesses before implementation. Inspections are crucial at every stage from manufacturing to delivery.
3. Supplier Verification Establishing relationships with reputable suppliers who meet international standards like ISO 9001 ensures a consistent supply of reliable fasteners.
Conclusion
Selecting the right metric bolt is not simply a matter of matching size and thread; it is a strategic decision that impacts the integrity and safety of the entire project. By comprehending their specifications, material properties, and adhering to rigorous standards, one can leverage metric bolts for maximum efficacy and reliability in any application. Trusting expert recommendations and empirical evidence ensures that every fastener contributes to the overarching goal of maintaining high standards of safety and performance.