In the realm of precision engineering and mechanical assemblies, the significance of seemingly minor components like M3 shim washers cannot be overstated. These small yet mighty components are fundamental in ensuring the flawless performance of complex machinery and electronic devices. Drawing upon years of industry experience, this article delves into the nuanced world of M3 shim washers, exploring their applications, selection criteria, and critical role in enhancing mechanical reliability.
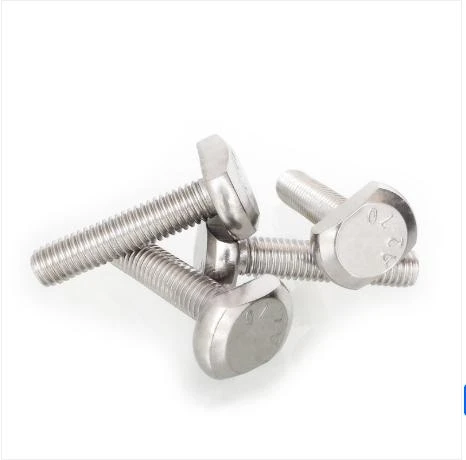
M3 shim washers are thin, disc-like components typically made from stainless steel, brass, or a variety of plastic materials. Their primary function is to fill small gaps or spaces between machine parts, ensuring precise alignment and reducing wear. The unique characteristics of M3 shim washers, such as their ability to withstand various environmental conditions, make them indispensable in high-precision industries like aerospace, automotive, and electronics.
Expertise in the proper application of M3 shim washers begins with a deep understanding of their diverse uses. They are often employed in situations where tolerance management is critical. For instance, in the assembly of electronic circuit boards, M3 shim washers can be used to maintain exact spacing between components, ensuring optimal circuit performance and preventing potential short circuits. In high-performance engines, they provide the necessary clearance adjustments, enhancing fuel efficiency and engine longevity.
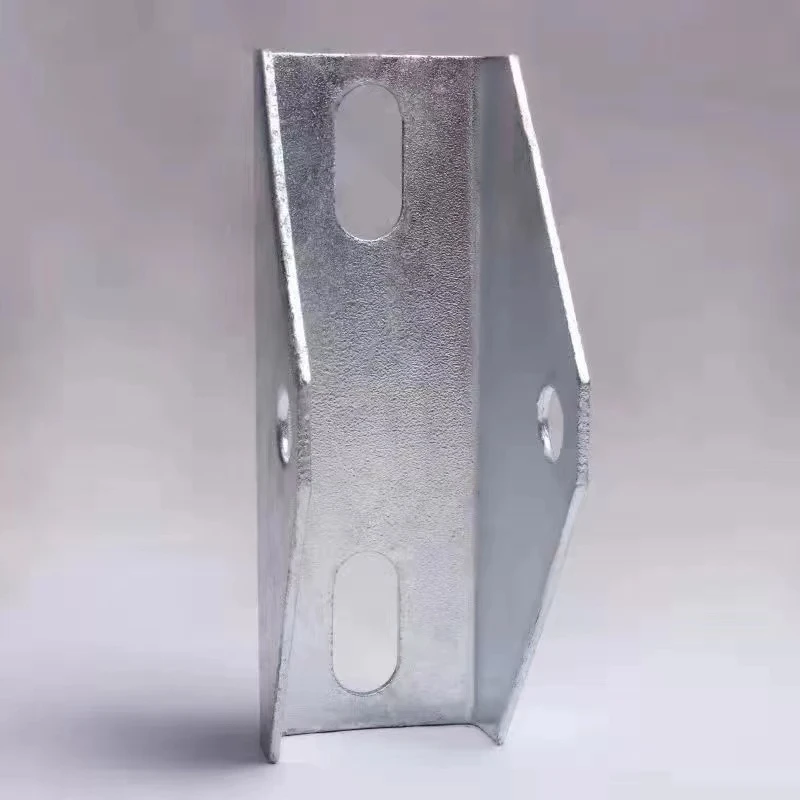
Selecting the appropriate M3 shim washer involves consideration of several factors, which is where professional insight becomes invaluable. Material selection is a crucial aspect; stainless steel shim washers are preferred in applications requiring durability and resistance to rust and corrosion, whereas plastic options might be chosen for their non-conductive properties in electrical assemblies. Thickness is another pivotal consideration; washers typically range from fractions of a millimeter to several millimeters, depending on the specific requirements of the task at hand.
Equally vital is the precision of the washer. M3 shim washers must conform to stringent manufacturing standards to ensure they meet the exact specifications needed for high-precision tasks. Variations as small as a micron can influence the performance of sensitive machinery, so sourcing these components from reputable manufacturers is of utmost importance. This is where the credibility of a supplier can be assessed based on their adherence to international standards and reputation in the market.
m3 shim washers
In terms of demonstrating authoritativeness, it's essential to reference industry standards and guidelines, as these underscore the collective expertise surrounding M3 shim washers. Standards such as ISO 9001 for quality management systems emphasize the importance of rigorous testing and quality assurance processes in the production of these components.
Building trustworthiness, particularly in sectors demanding high precision, involves documenting case studies and real-world applications where M3 shim washers have been pivotal in overcoming engineering challenges. Whether it's a documented improvement in mechanical stability in automotive transmissions or enhanced thermal regulation in electronics, these examples provide tangible proof of the washers' efficacy.
Additionally, sharing insights from industry experts—engineers, product designers, and quality assurance professionals—adds depth to the discussion on M3 shim washers. Their endorsements and insights help communicate the washers' value proposition, enlightening potential customers and decision-makers about the strategic advantages afforded by these small components.
In conclusion, the integration of M3 shim washers in precision applications represents a blend of technical expertise, meticulous selection, and high manufacturing standards. As vital components within complex mechanical and electronic systems, their role extends beyond mere spacing to encompass a range of functionalities that enhance the durability, efficiency, and reliability of assembly operations. Ensuring that these washers are sourced from reputable suppliers, selected with precision, and applied with expert knowledge will significantly contribute to the success and longevity of sophisticated engineering projects.