When inspecting the realm of fasteners, particularly washers, the M20 washer stands out, specifically for its role in construction, machinery, and various industrial applications. Uncovering the intriguing details around an M20 washer, especially regarding its outer diameter (OD), reveals layers of complexity and precision required to meet stringent standards. This washer isn't just a trivial element; it is pivotal in ensuring the stability and security of structures it fortifies.
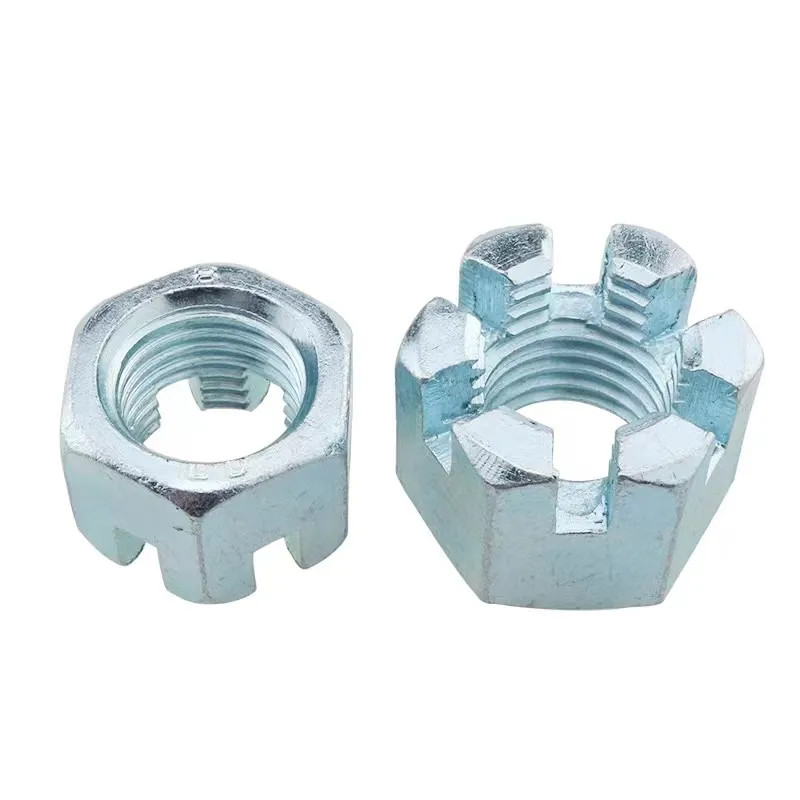
The M20 washer, famed for its compatibility with M20 bolts and nuts, serves as a crucial component designed to distribute load, minimize wear, and provide spacing when necessary. Its typical applications range from heavy-duty engineering projects to automotive industries, where precision is non-negotiable. The term M20 identifies the nominal metric diameter of the corresponding bolt thread, meaning the washer complements bolts with a diameter of 20 millimeters. Therefore, comprehending the outer diameter of an M20 washer is vital, as it plays a key role in its compatibility and performance.
Determining the optimal OD for an M20 washer involves recognizing the balance between its intended load distribution and the need for structural integrity. Standard specifications dictate that an M20 washer generally possesses an OD of 37 to 48 millimeters, with variations existing to suit specific applications. The outer diameter directly impacts the washer's ability to distribute pressure and prevents damage to the surface material. Engineers often lean towards washers with larger ODs when the goal is to spread load over a larger area, thereby reducing stress concentrations.
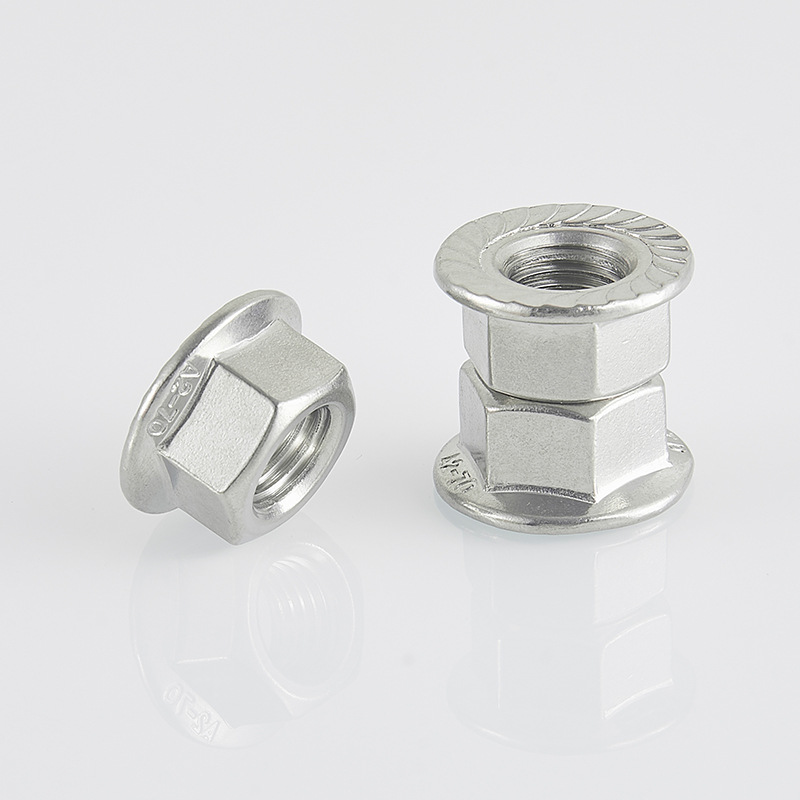
Material selection for an M20 washer is another pillar supporting its application efficacy. Commonly, materials range from galvanized steel, stainless steel, to high-strength alloys, each serving particular environments and requirements. A stainless steel washer, for example, offers superior corrosion resistance, making it ideal for outdoor or marine applications. Each material adheres to defined industry standards, ensuring durability, resilience against environmental conditions, and compliance with safety protocols. Expertise in materials science is essential to select the right washer that aligns with the environmental and mechanical demands of the project.
m20 washer od
Field experience reveals that a failure in selecting the appropriate OD and material can lead to significant mechanical failures. Considerations must account for dynamic loads, environmental exposure, and assembly conditions. An improperly sized washer can lead to uneven load distribution, leading to potential warping or slippage of the fastened materials. This emphasizes the importance of consulting design manuals and processing standards such as DIN, ISO, or ASTM, which delineate specifications for dimensions, mechanical properties, and testing methods for washers.
With technological advancement, the design and manufacturing of washers, like the M20 with specific OD, have become more sophisticated. Computer-aided design (CAD) and finite element analysis (FEA) allow engineers to simulate how washers will perform under various load conditions, optimizing efficiency and effectiveness before the production phase. Such innovations save time, reduce costs, and ensure precision, contributing to the trustworthiness and reliability of these components in critical applications.
Finally, aligning with global sustainability trends, manufacturers are exploring environmentally friendly processes and materials in washer production. Strategies such as using recyclable materials, reducing energy consumption during manufacturing, and enhancing the durability of products ensure that the M20 washer remains a staple in eco-conscious engineering solutions.
The intricacies of the M20 washer, particularly in terms of its OD, are not to be underestimated. Its role, although seemingly small, is indispensable in the grand scheme of engineering and construction. Understanding its specifications, material properties, and application can not only prevent structural failures but also enhance performance and longevity. The journey of mastering washers bridges practical experience with authoritative knowledge, ensuring these fundamental components continue to support the bedrock of modern industry efficiently and reliably.