In the world of engineering and mechanical applications, the M14 spring washer stands out as a crucial component designed to improve assembly efficiency and enhance the longevity of devices. Typically used in securing joints, its innovative design and specific material properties underscore its indispensable role in maintaining tension and preventing loosening from vibration and torque.
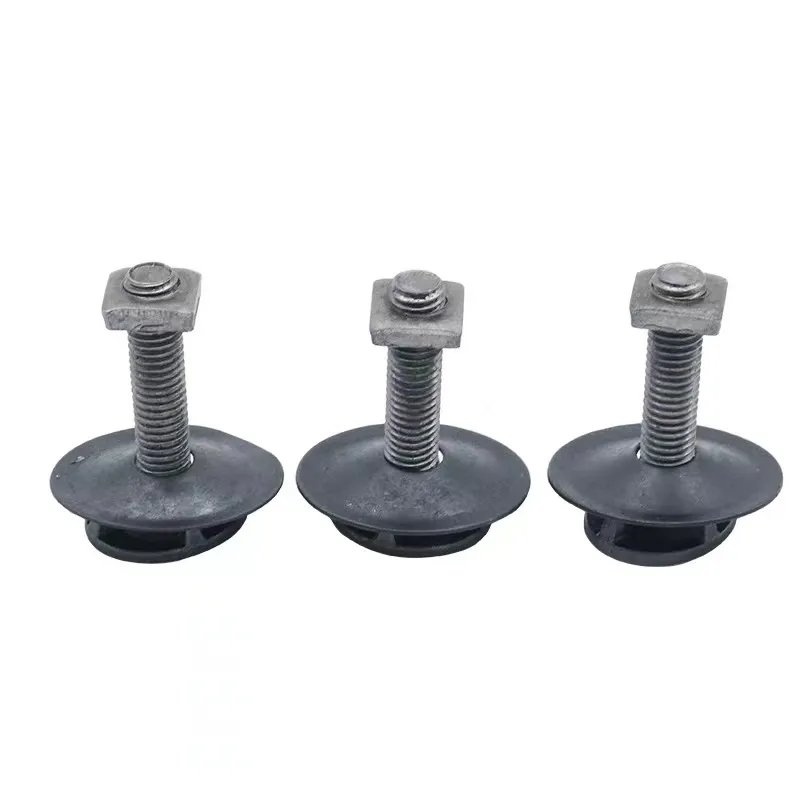
Spring washers, often referred to as disc springs, serve multiple purposes in machinery settings. The M14 spring washer, with its distinct specifications, caters to a wide array of uses across different industries such as automotive manufacturing, aerospace engineering, and construction. With an outer diameter typically around 27mm, this type of washer is specifically designed to fit snugly in M14 bolt systems. The choice of material is equally significant, with high-carbon steel and stainless steel being common. These materials provide the requisite strength and resistance against corrosion, ensuring that the spring washer delivers optimal performance even in harsh environments.
Experience with the M14 spring washer reveals its profound impact on the durability and reliability of mechanical assemblies. Professionals in mechanical engineering attest to the spring washer’s ability to mitigate axial loads effectively. By absorbing the stress and strain caused by the tightened bolts or nuts, the M14 spring washer minimizes potential damage that might occur due to continuous vibration or shock. This practical application translates into extended equipment life and reduced maintenance costs, which is especially beneficial in industrial settings where machinery downtime equates to substantial losses.
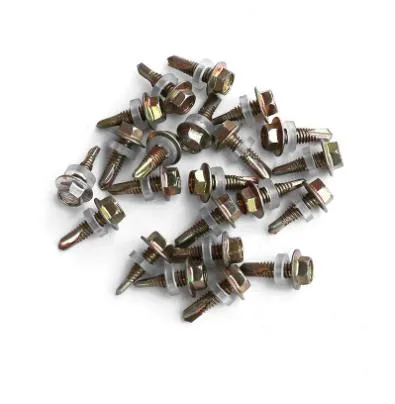
From an expertise standpoint, selecting an M14 spring washer requires an understanding of the specific application requirements. Engineers must consider key factors such as load bearing capacity, environmental conditions, and compatibility with other components in the assembly. For instance, in high-vibration environments like engine assemblies or bridges, the washer’s preload capacities can significantly contribute to the prevention of loosening, thus maintaining the structural integrity. Additionally, expertise in installation practices ensures that the washer is properly applied for maximum efficiency, maintaining a balance between tension and flexibility.
m14 spring washer
Authoritativeness in the use of M14 spring washers is backed by numerous standards that guide their manufacturing and application. International standards such as ISO 9001 or DIN 127 provide specifications that ensure the quality and uniformity of these components. Adherence to these standards by manufacturers underscores the reliability of the spring washers, providing a level of assurance to consumers about their efficiency and safety. The engineering community’s reliance on these standardized components reflects their endorsement of the product’s capability to deliver consistent results.
Trustworthiness plays a pivotal role when integrating M14 spring washers into mechanical designs. Over the years, these washers have garnered a reputation for enhancing joint security and reliability, which engineers and designers depend on heavily. Testing and quality assurance processes are vital to uphold this trust, as rigorous trials simulate the extreme conditions that the washers might encounter. This testing ensures that the final product not only meets but exceeds performance expectations, providing peace of mind for end-users.
The multifaceted utility of M14 spring washers emphasizes their significance in modern mechanical engineering. As industries continue to push the boundaries of technology and innovation, the demand for reliable components like the spring washer increases. Whether it’s preventing bolt loosening in a car engine or maintaining the structural integrity of an industrial machine, the M14 spring washer proves invaluable. Ultimately, its combination of practical application, expert-endorsed functionality, compliant quality standards, and proven reliability make it an essential component, driving both productivity and safety in various mechanical contexts.