Securing quality and performance in any assembly process requires a meticulous choice of components, and the M10 flange nut stands out as a staple in precision fastening solutions. While this essential component might seem mundane to the casual observer, its role is indispensable in various industries ranging from automotive to construction. Understanding the unique advantages that mark the M10 flange nut apart is crucial for any professional seeking to ensure reliability and durability in their work.
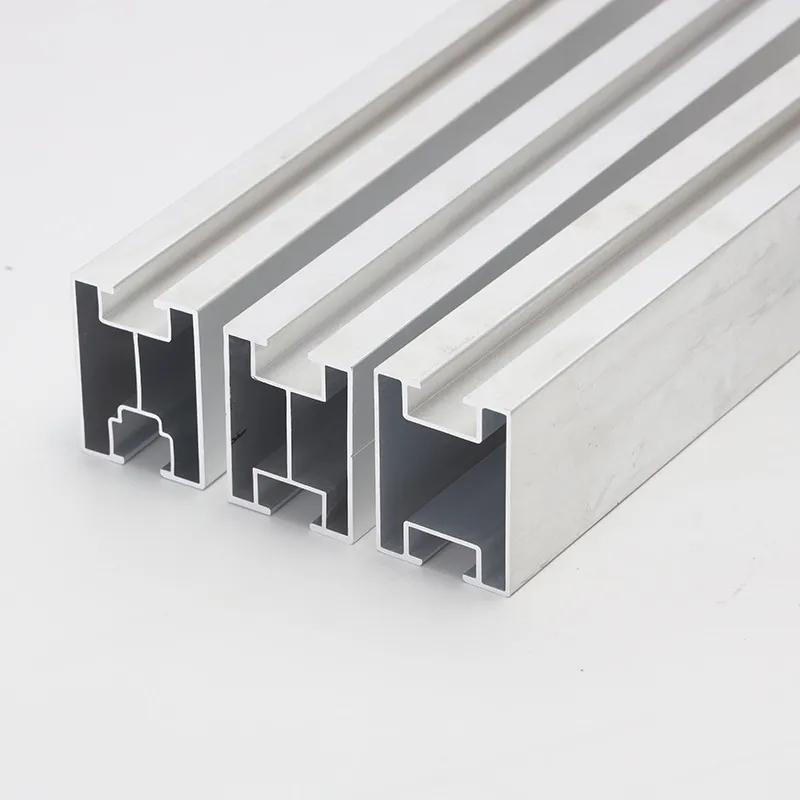
Crafted to deliver an optimal balance of security and ease-of-installation, the M10 flange nut is distinguished by its integrated washer-like flange which spreads the load. This design eliminates the need for additional washers, simplifying assembly processes and reducing the risk of over-tightening. The broad flange area provides a greater bearing surface, allowing it to deliver a more even distribution of pressure across the bolted joint. This feature not only enhances the component’s load-bearing capacity but also minimizes the potential for damage to the material under stress.
For industry insiders, the material composition of the M10 flange nut is a testament to its engineering excellence. Often manufactured from high-grade steel alloys, these flange nuts exhibit exceptional resistance to wear and corrosion. This durability is further augmented by finishes such as zinc plating or galvanization, making them ideal for both indoor and outdoor applications where exposure to varying environmental conditions is expected. Such robustness ensures that maintenance requirements are limited, providing long-term cost savings.
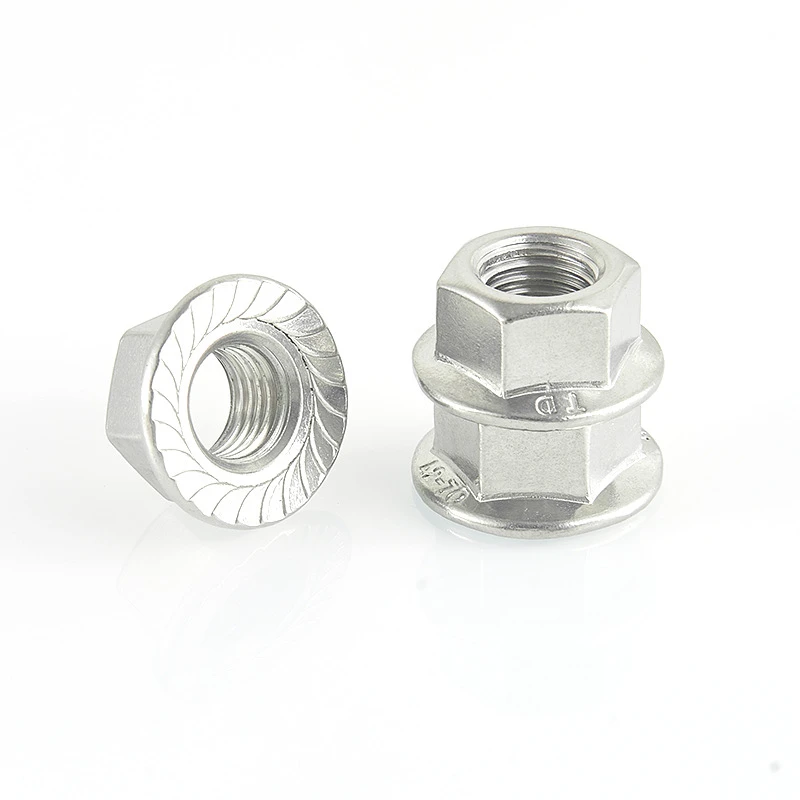
In applications requiring repeat assembly and disassembly, the self-locking characteristics of some M10 flange nuts stand as a significant advantage. These variants incorporate a nylon insert that grips the bolt thread tightly, ensuring a secure fit that resists vibration and prevents loosening over time. This makes them particularly suitable for use in machinery and vehicles subject to constant motion or agitation.
m10 flange nut
Professionals who prioritize both efficiency and cost-effectiveness in their projects appreciate the versatility of the M10 flange nut. Whether opting for hexagonal, serrated, or non-serrated versions, these fasteners are designed to accommodate a range of sizes and loads. Especially in the context of automotive repairs or large-scale construction projects, having access to a reliable stock of M10 flange nuts can mean the difference between a seamless operation and costly downtime.
Despite their relative simplicity,
not all M10 flange nuts are created equal. Choosing nuts that adhere to high manufacturing standards (such as ISO or DIN specifications) ensures consistent performance and safety. Industry experts recommend sourcing these components from reputable suppliers who can provide detailed material certifications and traceability data—key factors in maintaining quality assurance across projects.
As industry standards continue to evolve, the integration of smart materials and advanced manufacturing techniques are poised to enhance the capabilities of the M10 flange nut even further. Innovations such as weight-reducing alloys or eco-friendly coatings are gradually making their way into mainstream use, promising even greater efficiency and sustainability in fastening solutions.
Ultimately, the M10 flange nut serves as more than just a fastener; it is a pivotal element in the structural integrity of countless modern-day creations. For engineers and construction professionals alike, understanding its properties and applications is an investment in both product excellence and peace of mind. From its role in minimizing material fatigue to its capacity to simplify assembly processes, the M10 flange nut exemplifies how small components can have an outsized influence on the quality and success of industrial endeavors.