In the realm of construction and DIY projects, the type of screws used can significantly impact the longevity and stability of a project. Among the myriad of options, hot dipped galvanized screws stand out for their exceptional durability and resistance to corrosion. These screws are considered essential in environments where moisture is prevalent, or where structures must endure rigorous weather conditions. This article delves into the practical benefits, production process, and applications of these robust fasteners, providing expert insight and proof of their superiority.
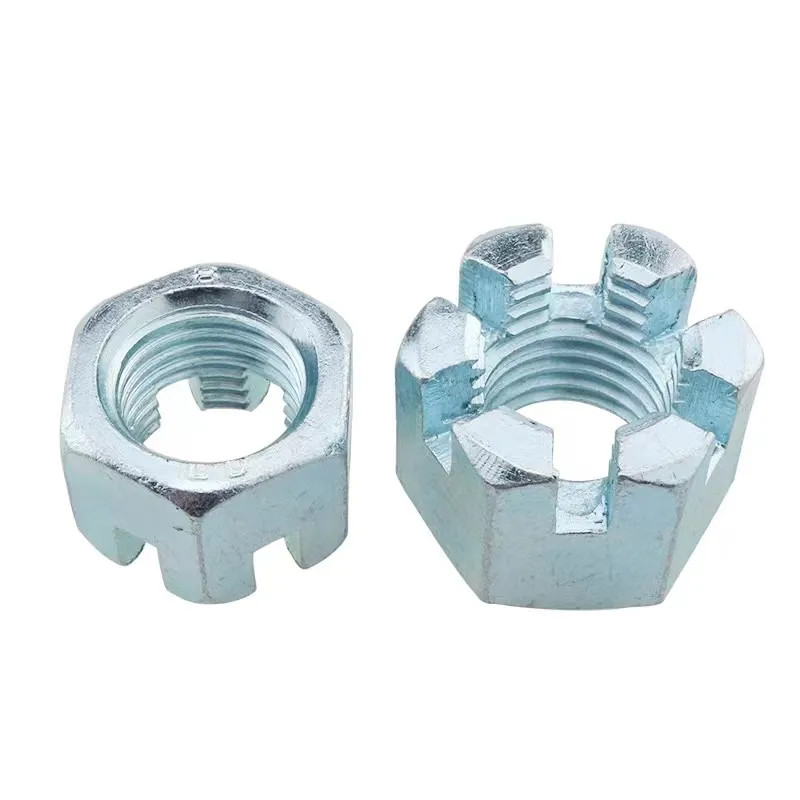
Hot dipped galvanized screws undergo a unique metallurgical bonding process that coats them with a thick layer of zinc. This process, known as hot dip galvanizing, involves immersing the screws into molten zinc at temperatures of around 450 degrees Celsius. The result is a sturdy, bonded finish that not only shields the screw from corrosive elements but also extends its functional lifespan. This protective layer is far thicker compared to that of screws coated with paint or electroplating, thereby significantly enhancing the screw's rust resistance.
One of the most significant advantages of utilizing hot dipped galvanized screws is their superior performance in harsh outdoor environments. Buildings, fences, and decks exposed to the elements benefit extensively from these screws, as they ensure structural integrity by preventing rust-related weaknesses. This resistance to corrosion leads to a decrease in the frequency and necessity of replacing the fasteners, consequently reducing maintenance costs and ensuring safety over time.
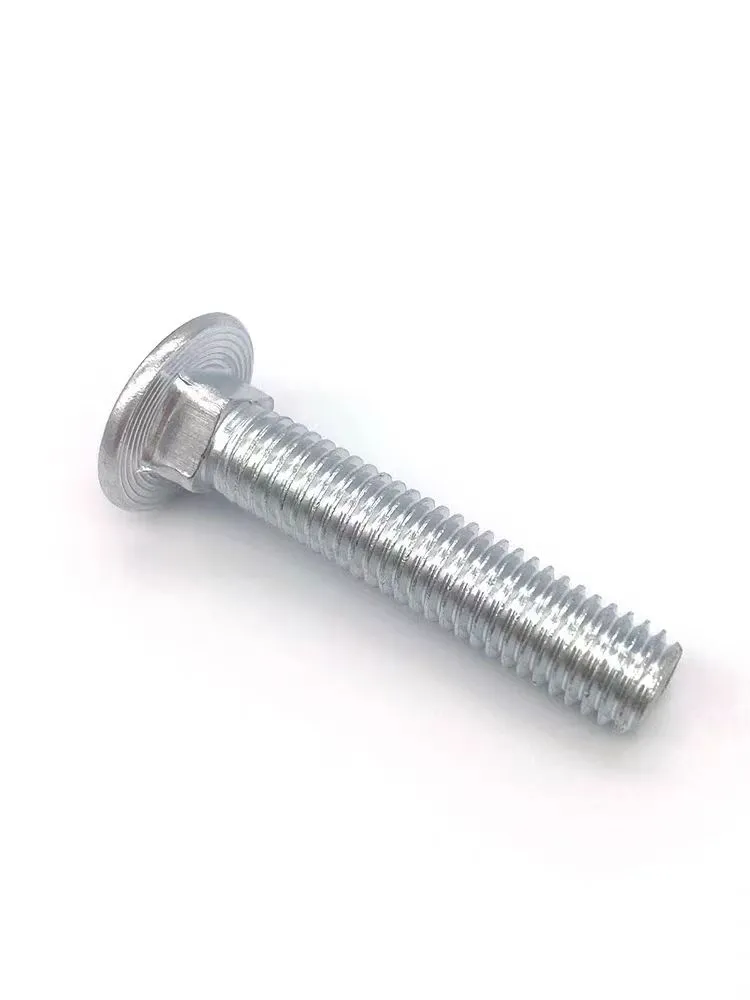
Professionals and seasoned DIY enthusiasts often emphasize the importance of choosing the right fastener for the job. Poor choices can lead to project failures, unexpected costs, and unsafe structures.
Hot dipped galvanized screws's industry reputation stems from their reliability in nature's most unyielding conditions. They are trusted by construction professionals to meet rigorous standards and requirements, guaranteeing stability and durability in construction projects.
hot dipped galvanized screws
From an expert perspective, the application of these screws is vast. They are ideal for use in marine environments, agricultural applications, and for securing outdoor furniture. Their robust nature is suitable for attaching wooden, metal, and composite structures, making them a versatile component in any toolkit. Indeed, hot dipped galvanized screws should be a go-to option when looking for materials that combine strength with corrosion resistance.
While the upfront cost of these screws may be slightly higher than standard screws, the investment is offset by the savings acquired from reduced maintenance and longevity of the structures they are used in. Over their extended life cycle, galvanized screws more than pay for themselves, while also offering peace of mind when it comes to structural safety.
Adhering to the best practices of construction, these screws offer an added layer of assurance in reliability and quality. For those seeking evidence of their effectiveness, extensive industry testing and user feedback consistently highlight their commendable performance. Trustworthiness in construction materials cannot be overstated, and galvanized screws meet and often exceed expectations.
In conclusion, hot dipped galvanized screws are a top choice for those who value durability, safety, and cost-efficiency in their construction and DIY projects. Thanks to their corrosion-resistant properties and long-term reliability, they represent an intelligent investment in the integrity and longevity of any build. Whether you're a construction expert or a weekend warrior, choosing these screws ensures that your projects withstand the tests of time and elements alike.