Hot dipped galvanized anchor bolts stand as a pivotal element in the construction and manufacturing industry, offering unparalleled durability and reliability. Their production process involves coating steel bolts with a layer of zinc, through a method known as hot-dipping. This results in an anchor bolt with enhanced corrosion resistance, making it suitable for a variety of applications, especially in environments exposed to moisture and harsh weather conditions.
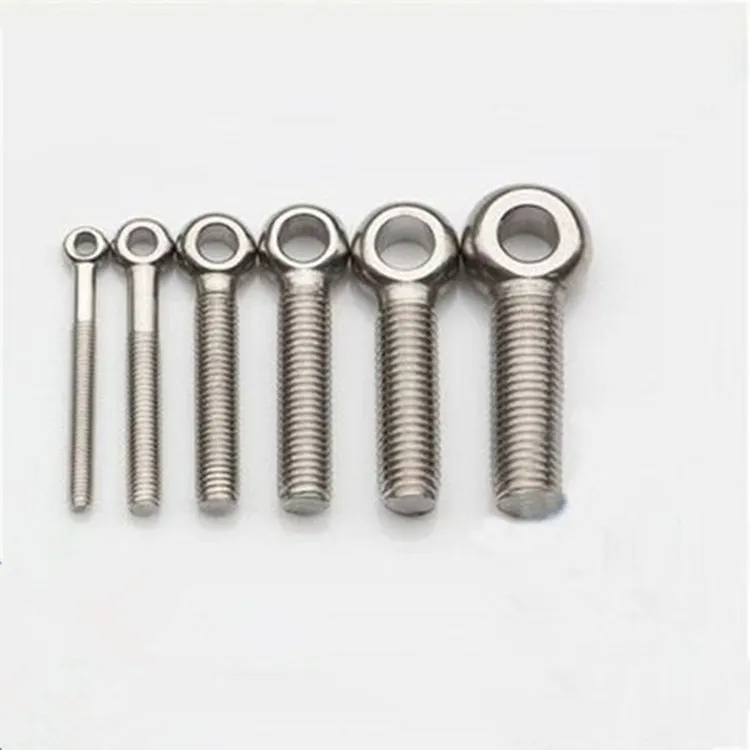
The expertise required to produce hot dipped galvanized anchor bolts is indicative of their crucial role in structural integrity. These bolts are a preferred choice across numerous industries including construction, marine, and automotive sectors. Their ability to resist rust and corrosion prolongs the lifespan of critical infrastructures such as bridges, buildings, and roadways. Often buried underground or submerged in water, these bolts provide stability and ensure safety in adverse conditions.
Professionals in the construction industry often select hot dipped galvanized anchor bolts due to their superior performance as compared to other types of fasteners. The galvanizing process begins with cleaning the steel surface, which is then dipped into a molten zinc bath. This results in a metallurgical reaction that forms a robust bond between the zinc and the steel. Unlike electroplating, this method ensures a uniform coating, granting the bolts an extended lifecycle and reducing maintenance costs over time.
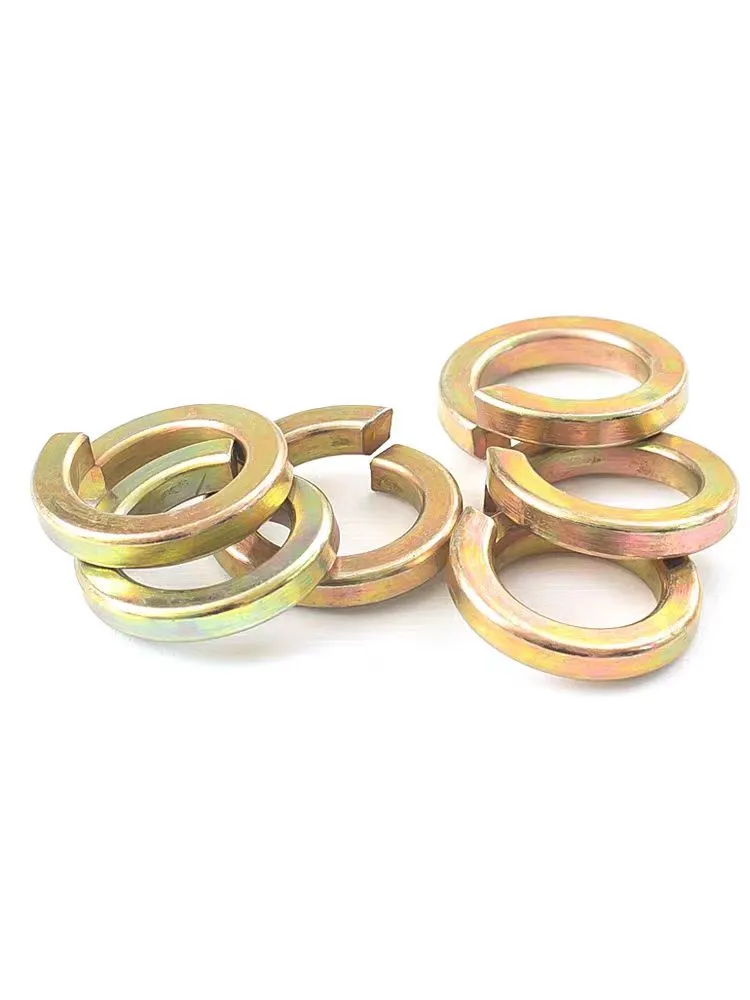
Authoritative sources within the engineering community emphasize the importance of using high-quality anchor bolts to prevent structural failures. Standards and certifications such as ASTM and ISO are often referenced to ensure that these bolts comply with international safety and quality regulations. Adherence to these standards guarantees that the hot dipped galvanized anchor bolts maintain their mechanical properties and performance metrics, even under significant load-bearing scenarios.
hot dipped galvanized anchor bolts
When considering trustworthiness, it is essential to acquire anchor bolts from reputable manufacturers who have established a track record of producing consistent and reliable products. Manufacturers usually employ rigorous quality assurance methods, including tensile testing and salt spray tests, to verify the bolts' resistance to environmental factors and mechanical stress. These tests simulate real-world conditions, providing end-users with confidence in the product's capability.
Real-world experience serves as one of the strongest testimonials to the effectiveness of hot dipped galvanized anchor bolts. Engineers and contractors have witnessed firsthand how these bolts contribute to the longevity and safety of their projects. In coastal areas where saltwater corrosion is prevalent, or in industrial zones where chemical exposure is frequent, these bolts withstand aggressive conditions, maintaining their integrity where other materials might fail.
Besides their functional benefits,
these anchor bolts offer economic advantages. By reducing the need for frequent replacements and repairs, they contribute to cost savings in project management. Furthermore, their robust nature means that there is less downtime for maintenance, ensuring that infrastructures remain operational and society benefits from uninterrupted services.
In conclusion, hot dipped galvanized anchor bolts are an integral component that combines technical expertise, reliability, and economic efficiency. Their resilience in challenging environments makes them indispensable for ensuring the longevity and safety of modern infrastructures. As technologies evolve, so do manufacturing processes, continually improving the quality and performance of these bolts. It's crucial for stakeholders to prioritize sourcing from credible suppliers who uphold industry standards, ensuring that every bolt fulfills its intended purpose with precision and reliability.