Hot dipped bolts are a staple in the hardware industry, renowned for their superior durability and corrosion resistance, making them an excellent choice for various applications ranging from construction to machinery. These bolts undergo a hot-dip galvanization process, where they are submerged in molten zinc, creating a robust and long-lasting protective layer. This process enhances their resistance to harsh weather conditions and corrosive environments, ensuring structural integrity over time.
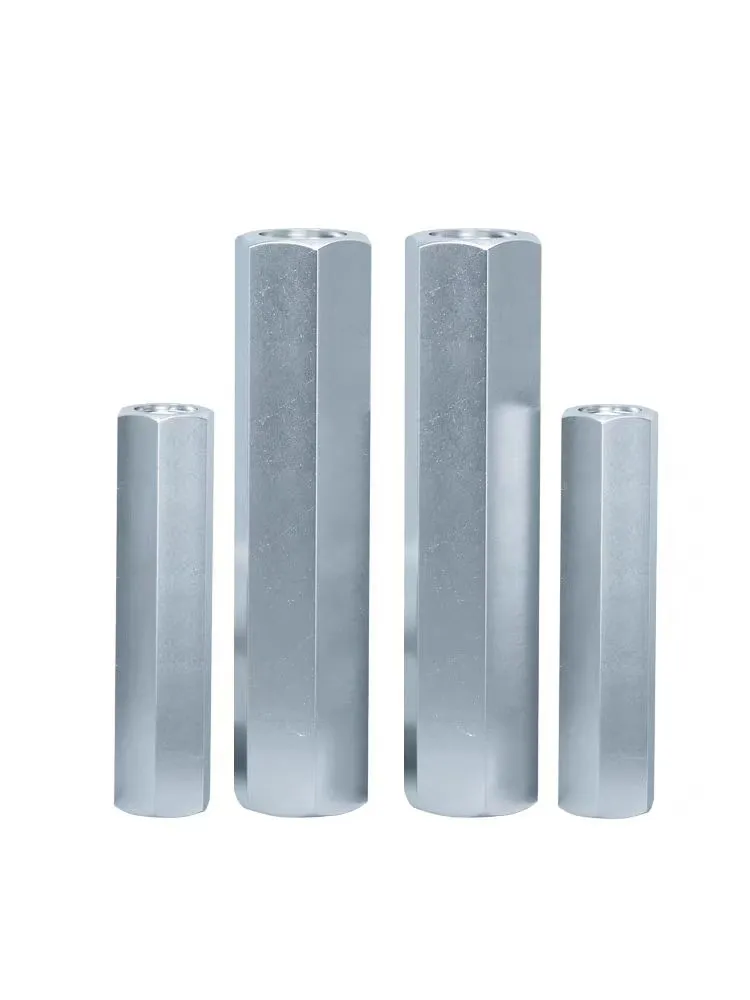
Expertise with hot dipped bolts begins with understanding their construction and mechanical attributes. Manufactured using high-quality steel, these bolts are designed to bear heavy loads and withstand significant stress, making them indispensable in infrastructural projects. Their exceptional tensile strength is a result of meticulous engineering, where precision and material quality play crucial roles. Engineers and builders often opt for hot dipped bolts in structural applications such as bridges, high-rise buildings, and industrial facilities.
From an authoritativeness perspective, hot dipped bolts are often specified in building codes and standards worldwide due to their proven track record. They meet and often exceed international safety and performance standards, including those set by the American Society for Testing and Materials (ASTM). Their adoption in critical and large-scale projects underscores their reliability and performance efficacy.
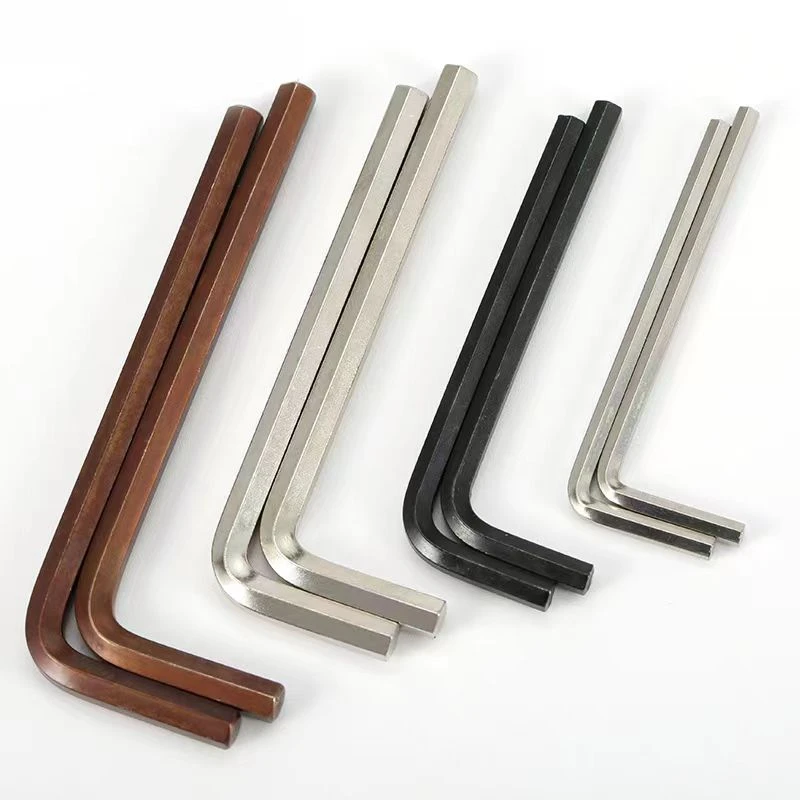
Real-world experience in using hot dipped bolts highlights their adaptability and resilience. For instance, in coastal regions where structures are constantly exposed to saltwater, the anticorrosive nature of these bolts prevents rust, a common issue with standard fasteners. Engineers have observed that using hot dipped bolts significantly minimizes maintenance costs over the life of a structure. Similarly, in industrial settings like chemical plants, where exposure to harsh substances is common, these bolts maintain their integrity, offering peace of mind and ensuring safety.
hot dipped bolts
The trustworthiness of hot dipped bolts can be illustrated through multiple case studies demonstrating their longevity and dependability. In one notable instance, a major infrastructure project replaced standard bolts with hot dipped variants during a retrofit, observing a marked improvement in durability and reduced instances of joint failure. This reinforced the importance of investing in quality materials upfront for long-term benefits.
While selecting hot dipped bolts, it is crucial to consider factors such as bolt size, thread pattern, and the specific requirements of the application.
Collaborating with reputable suppliers ensures the supply of bolts that meet stringent quality controls. Additionally, utilizing proper installation techniques further enhances the performance of these fasteners, ensuring their optimal function in any setting.
For industries focused on sustainability and environmental impact, hot dipped bolts present an eco-friendly option. The galvanization layer not only extends the life of the bolts but also minimizes the need for frequent replacements, reducing material wastage and environmental strain.
In conclusion, hot dipped bolts represent a blend of strength, durability, and economic viability, making them an essential component in modern engineering and construction. Their widespread utility across diverse sectors is a testament to their unparalleled performance and the confidence they inspire among professionals. As infrastructures continue to evolve and adapt to new challenges, hot dipped bolts remain a steadfast solution, ensuring safety, reliability, and structural soundness in every endeavor.