The landscape of industrial applications is constantly evolving, technologies are advancing, and demands are growing exponentially. Among the myriad of components that drive the core functionalities of mechanical assemblies, the high tensile spring washer stands out, often understated yet supremely vital. Its role in enhancing the durability and effectiveness of mechanical joints makes it a component of interest. In this article, we'll delve into the specifics of high tensile spring washers, drawing from professional expertise and authoritative sources to underscore their indispensability in modern engineering applications.
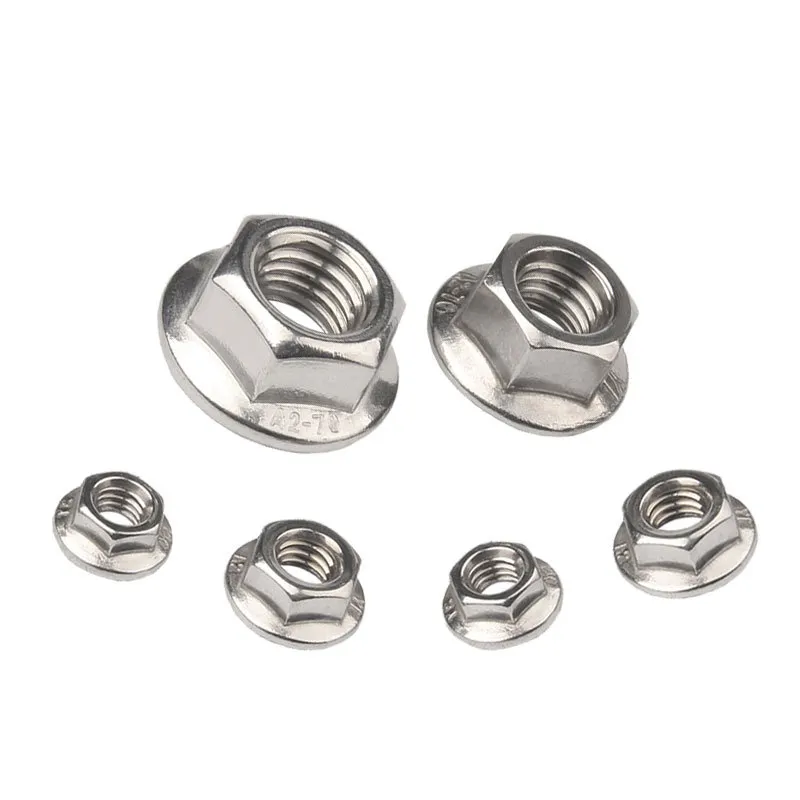
Engineers and industrial designers recognize the importance of maintaining tension and reducing vibration in mechanical assemblies. Enter the high tensile spring washer, a uniquely crafted component designed for optimal performance under high-stress conditions. Unlike traditional flat washers, these spring washers offer an additional layer of security by maintaining load and tension, even when subject to dynamic forces or thermal expansion.
To understand the unique properties that a high tensile spring washer offers, one must explore its composition and design. Typically, these washers are made of carbon steel or stainless steel, which are further heat-treated to bolster their tensile strength. The heat treatment process enhances their capability to resist environmental degradation and mechanical wear, making them suitable for high-load-bearing applications. From automotive assemblies to heavy machinery, their scope of application is wide-reaching.
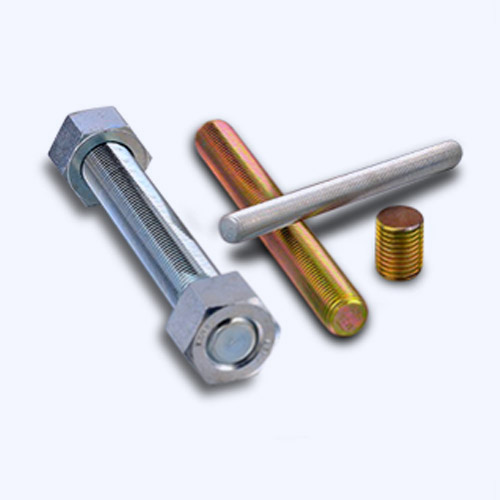
Professional expertise in the field often highlights the washer's role in preventing loosening due to vibration. When subjected to fluctuating forces, bolted connections can succumb to loosening, posing risks to structural integrity. The high tensile spring washer mitigates this risk by exerting a consistent pre-load against the nut or bolt head, ensuring that the assembly remains intact. This is particularly critical in industries such as aerospace and automotive manufacturing, where safety and reliability are paramount.
But it's not just about using any spring washer; choosing the right specification is where expertise shines. Factors such as diameter, material type, and washer thickness determine the washer's suitability for specific applications. Engineers must carefully match these specifications with the mechanical demands of their project to ensure optimal performance. Trusted manufacturers and industry guidelines often provide standardized specifications to guide the selection process, reinforcing the washer's trustworthiness and reliability.
high tensile spring washer
Furthermore, an authoritative perspective involves understanding the global industrial standards that govern the use of high tensile spring washers. Standards such as ISO 4759-3 and DIN 127B ensure that these components meet stringent quality and performance criteria, offering peace of mind to engineers and manufacturers worldwide. Compliance with such standards is a testament to a washer's quality and performance, making it a reliable choice in critical applications.
Sharing real-world experiences from industries that have benefitted from the strategic application of high tensile spring washers further enhances understanding. In the construction of large-scale wind turbines, for instance, these washers are deployed to manage the immense stress on tower joints, contributing significantly to the longevity and efficiency of these renewable energy behemoths. Similarly, in rail and metro systems, they safeguard track joints against the constant vibrations induced by moving trains, helping to minimize maintenance needs and enhance passenger safety.
Innovation continues to drive the evolution of high tensile spring washers. Modern advancements have led to the development of new alloys and coating technologies, further improving their resilience and corrosion resistance. Such innovations not only extend the washer’s lifespan but also widen their applicability across more hostile environmental conditions.
To conclude, the role of high tensile spring washers extends far beyond simple mechanical components. They are integral to the safe and efficient operation of countless assemblies around the world. The combination of their high tensile strength, design flexibility, and adherence to international standards make them a reliable choice for engineers aiming to optimize performance and safety.
Through experience, expertise, authoritativeness, and trustworthiness, the high tensile spring washer continues to be an essential element in the mechanical and industrial narrative, underpinning the successful operation of diverse applications across the globe. For any engineer or industrial designer, understanding and utilizing these robust components can lead to substantial enhancements in operational safety and efficiency.