The hexagon head bolt, a seemingly modest component, plays an essential role across various industries. Its importance is undeniable when considering the mechanics of bolted joints and the structural integrity they facilitate. Navigating the intricacies of hexagon head bolts requires understanding their design, application, and quality considerations.
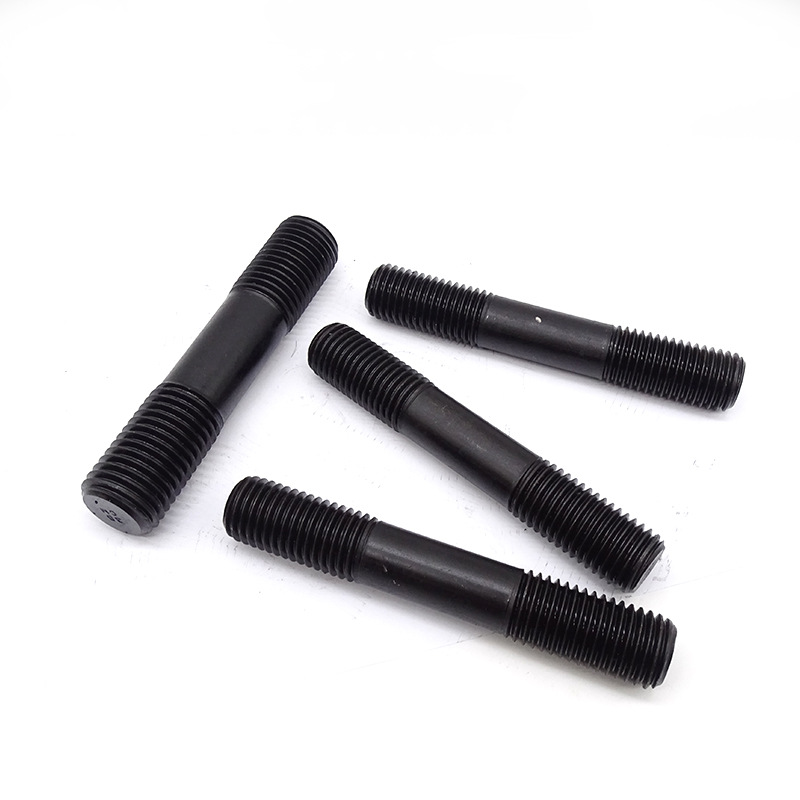
At the core of a hexagon head bolt's design is its six-sided, or hexagonal, head. This geometric feature is not merely for aesthetics. The hexagon's structure allows for easy gripping and turning by wrenches and spanners, providing the leverage necessary to tighten or loosen the bolt in complex environments. In automotive and construction scenarios where precision, ease of access, and tool compatibility are crucial, the hexagon head shines.
Diving deeper into materials, hexagon head bolts are typically manufactured from stainless steel, carbon steel, or galvanized steel. Each material offers distinct advantages stainless steel ensures resistance to corrosion and is ideal for marine or outdoor applications, carbon steel provides strength and durability for heavier loads, and galvanized steel offers an economical choice with a protective zinc coating to combat rust. Engineers must weigh these material properties against environmental stresses to ensure the longevity and safety of the application they support.
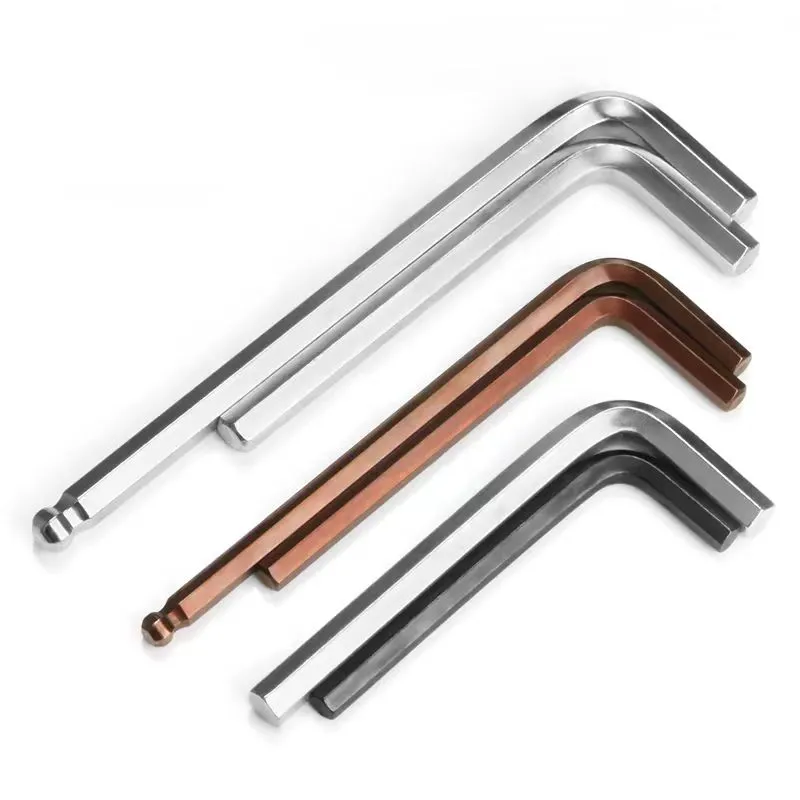
Another technical aspect lies in understanding the significance of bolt grades and threads. Hexagon head bolts are categorized by grades that denote their tensile strength and adaptability to stress. Grades 2, 5, and 8 are commonly encountered, with each offering varying levels of resilience. Choosing the appropriate grade directly correlates to the anticipated load and conditions, thus ensuring safety and performance.
Hexagon head bolts also feature different thread types coarse and fine. Coarse threads offer rapid assembly with better resistance to debris accumulation, whereas fine threads provide superior grip strength due to higher thread engagement. Selecting the correct thread type is pivotal, particularly in high-vibration applications like machinery, where a secure fastener ensures operational safety.
hexagon head bolt
For industries like aerospace, automotive, and construction, adherence to standards is paramount. Organizations such as ASTM, ISO, and SAE have established strict guidelines ensuring that hexagon head bolts meet specified mechanical properties and dimensional standards. This not only ensures component reliability but also fortifies trust in the manufacturers who consistently adhere to these benchmarks.
Furthermore, advances in manufacturing technologies have introduced innovations in production processes of hexagon head bolts. Cold forming and hot forging are two prevalent manufacturing techniques. Cold forming maintains superior structural integrity, reducing the risk of future deformations, while hot forging allows for the production of larger bolt dimensions capable of handling increased stresses.
Quality assurance remains an integral component in the production and application of hexagon head bolts. Rigorous testing methodologies—ranging from tensile strength assessments to ultrasound inspection—are implemented to detect material inconsistencies and defects. These protocols play a crucial role in validating the bolt's capabilities, providing peace of mind and bolstering the trust of engineers and quality inspectors alike.
In terms of application, real-world experience underscores the adaptability of hexagon head bolts. In automotive assembly lines, their ease of installation and removal accelerates production timetables while maintaining alignment integrity. In construction, they provide vital connectivity in skeletal frameworks and bridge infrastructures, proving indispensable by reliably transmitting loads and withstanding harsh environmental conditions.
The trusted role of hexagon head bolts is undeniably linked to the comprehensive expertise applied during their design, manufacture, and utilization. By drawing upon authentic user experiences and leveraging rigorous quality control practices in line with industry standards, these bolts continue to uphold their reputation as a vital component across numerous applications. The convergence of engineering excellence, material science, and compliance with regulatory standards ensure that hexagon head bolts not only meet current demands but are poised to adapt to future industry challenges.