Galvanized bolts, an integral component across various industries, are often heralded for their robustness and longevity. They are crafted from steel and given a coating of zinc to deter corrosion, making them particularly vital in outdoor and industrial applications where rust and weather exposure can be significant concerns. A comprehensive understanding of galvanized bolts can empower informed choices, ensuring reliability and safety for structural innovations.
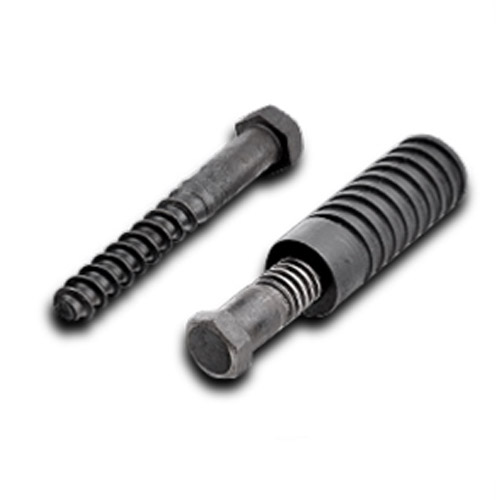
Venturing into the realm of galvanized bolts begins with an appreciation of their manufacturing process. The process of galvanization involves immersing steel bolts into molten zinc, which creates a metallurgical bond between zinc and the steel. This step forms a protective layer of zinc oxide that guards the bolt against moisture and corrosive elements. This is a crucial factor in applications where durability and integrity of the bolt are paramount, such as in building smog-prone urban structures or coastal facilities exposed to saline air.
In-depth knowledge about the types of galvanized bolts reveals significant variations that cater to specific needs. Hot-dip galvanized bolts, known for their thick zinc coating, provide exceptional corrosion resistance, making them suitable for extreme environments. Their counterpart, the electro-galvanized bolt, offers a thinner coating but with a smooth, aesthetic finish, favored in aesthetic-concerned and less corrosive settings. Selecting the right type depends on the specific environmental challenges expected, balancing between aesthetics and endurance.
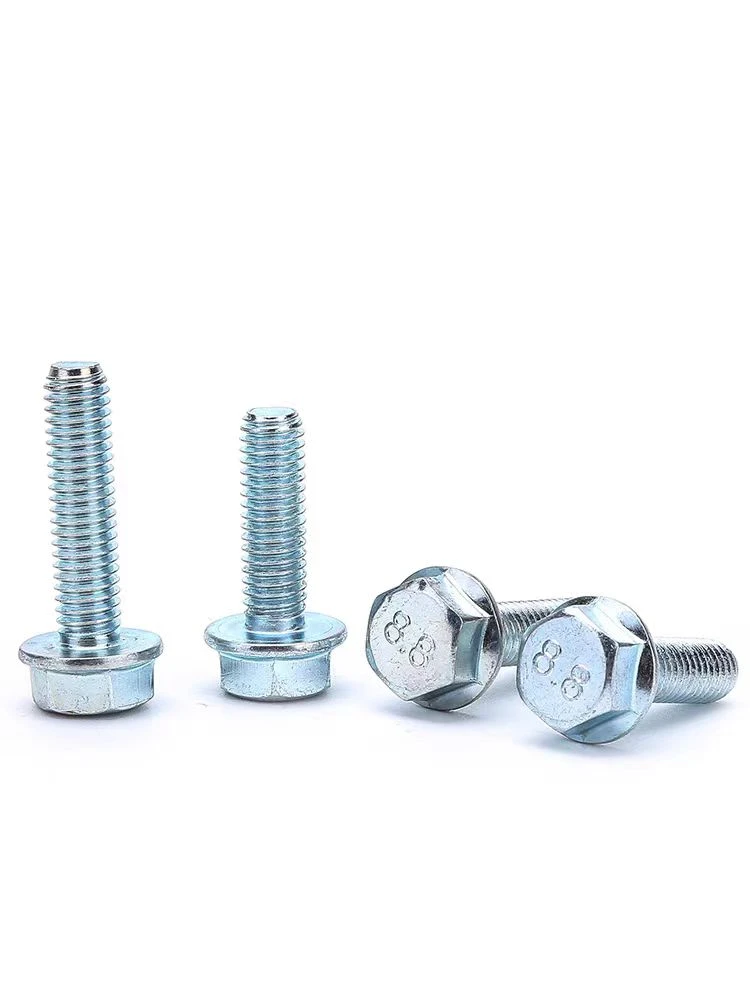
Experts in construction and engineering often go beyond just selecting bolts; they count on specific technical standards to guide their choices. Galvanized bolts adhere to strict industry standards such as ASTM A153, A193, or A307, ensuring these components meet rigorous performance and safety measures. Such standards not only define the bolt's physical properties and construction but guarantee quality assurance in demanding applications. Professionals in the field are encouraged to constantly update their knowledge of evolving standards to ensure compliance and optimal performance.
The endurance of galvanized bolts is further enhanced by their versatility in various applications. From securing massive bridge structures to assembling delicate electronics, these components are trusted for their dependability. Their resistance to corrosion means less maintenance is required over time, reducing long-term cost investment - an attractive feature for large-scale projects focusing on sustainability.
galvanized bolts
When weighing the decision to use galvanized bolts, professionals often consider the project lifecycle costs. While initial expenses might be higher compared to non-galvanized alternatives, their longevity and low maintenance make them cost-effective in the long run. Trust in galvanized bolts is well-placed; countless bridges, towers, and vehicles rely daily on these meticulously crafted components to maintain safety and stability.
Authoritative sources like industry journals and collaboration with galvanization experts have continuously emphasized the impressive rate of return galvanized bolts offer. The equipment and technology used in galvanizing processes have evolved, enabling higher precision and efficiency, further enhancing product quality.
Real-world applications serve as testament to galvanized bolts' efficacy, especially where safety is non-negotiable. Maritime structures, for instance, face relentless abrasion from water and air; galvanized fasteners here are critical. Similarly, they are indispensable in agriculture, where structures are persistently exposed to fertilizers and seasonal changes, underscoring these bolts' unmatched protective prowess.
To achieve optimal results from galvanized bolts, proper installation techniques must be followed. Torque specifications, attention to material compatibilities, and comprehensive post-installation checks are crucial steps that experienced professionals advocate. Missteps in installation can compromise the structural integrity, regardless of the bolt's quality.
In synthesizing expertise and varied technical insights, the primacy of galvanized bolts in industry and construction is unequivocally established. With ongoing advancements and commitment to quality assurance, this component remains an indefatigable choice for those seeking resilience and precision in demanding applications. While every project is unique, galvanized bolts provide a reliable backbone that industry professionals can consistently rely upon for excellence and safety in their undertakings.