In the world of mechanical assemblies and fastening challenges, the humble flat round washer emerges as an unsung hero, bringing a blend of simplicity and functionality to various projects and industries. Despite its unassuming appearance, this tiny component bears a significant load, playing a pivotal role in distributing pressure and securing connections across a wide array of applications.
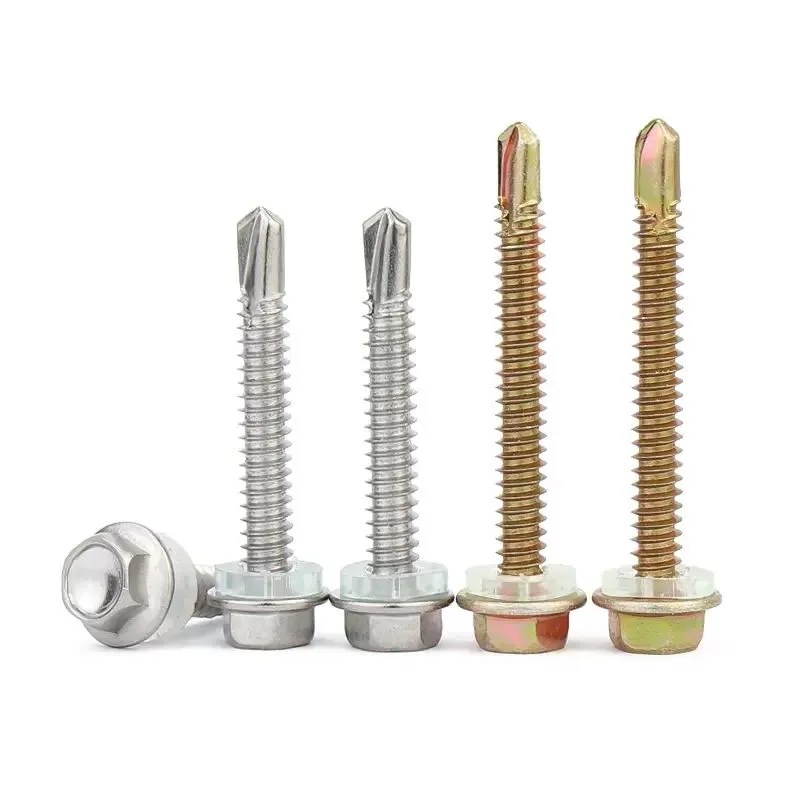
A flat round washer, typically crafted from metals like steel, stainless steel, or brass, is a thin, flat disk with a centrally located hole used to create a soft barrier between a bolt or nut, and the connecting object. This function is vital in preventing wear and tear, reducing friction, and averting unnecessary damage to surfaces. In essence, flat round washers safeguard the longevity and performance of diverse assemblies, making them indispensable in construction, automotive, aerospace, and home improvement fields.
The historical significance of washers can be traced back to innovations in fastener technology. Their development is intertwined with advancements in engineering and precision mechanics, underscoring their longstanding importance. Engineers and craftsmen have long recognized the necessity of distributing clamping forces more evenly—a task adeptly handled by flat round washers.
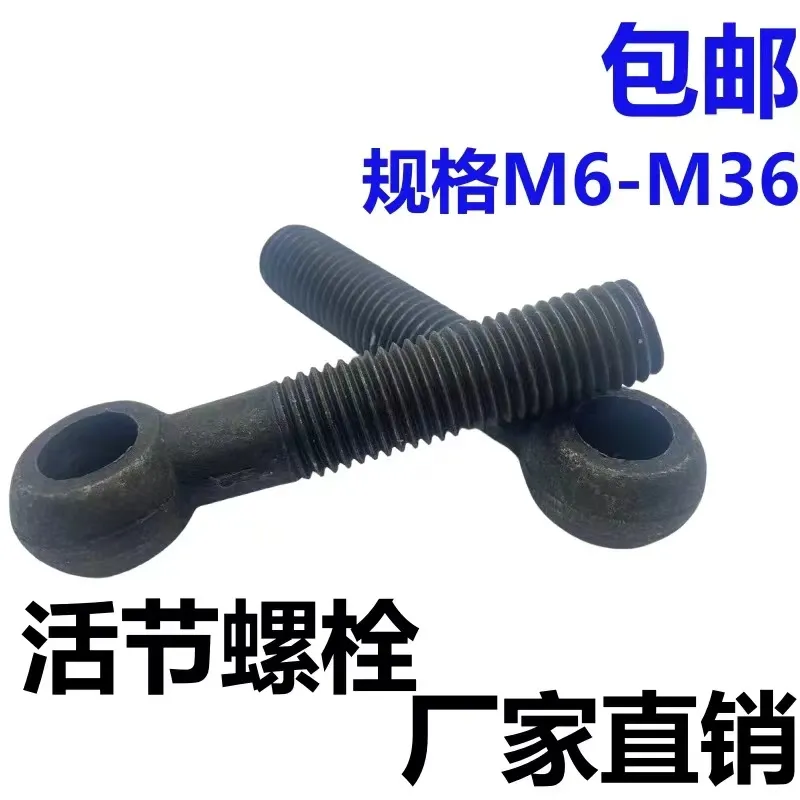
Experience dictates that selecting the appropriate flat round washer is as crucial as choosing the correct bolt or nut. Comprehending the material compatibility, load distribution requirements, and environmental factors ensures that washers perform optimally. For instance, stainless steel washers are favored in marine environments for their resistance to corrosion, while brass offers superior conductivity and is often employed in electronic assemblies. This nuanced understanding can dramatically enhance the effectiveness and durability of any project.
flat round washer
From an expert's perspective, the installation of flat round washers might appear straightforward, yet it demands precision. Proper alignment is critical; washers should be positioned to distribute loads evenly and avoid skewed pressure that could compromise joint integrity. Over-tightening can deform washers, diminishing their protective function and leading to premature failure of the joint. Thus, torque specifications should be meticulously followed to maintain structural integrity and extend the lifespan of both the washer and the assembly as a whole.
Authoritative voices in the engineering field often emphasize the economic efficiency of incorporating flat round washers in product design. By mitigating the risk of damage through wear and corrosion, washers can significantly reduce maintenance costs and extend the life of machinery components. This perspective gains particular traction in large-scale manufacturing, where the longevity of parts directly correlates with production efficiency and cost management.
Trustworthiness in flat round washers is further enhanced through adherence to stringent manufacturing standards. Reputable manufacturers comply with established industry standards, such as those set by the American Society for Testing and Materials (ASTM) or the International Organization for Standardization (ISO). These standards ensure consistency in quality, performance, and compatibility with various fasteners.
In conclusion, the flat round washer, though frequently overlooked, is a cornerstone of reliable and efficient mechanical assemblies. With a rich history rooted in engineering ingenuity and continuing relevance across a multitude of industries, selecting and utilizing these washers effectively is a testament to one’s expertise and commitment to quality. By appreciating the nuanced roles washers play in our fastener systems, we bolster the durability and reliability of everything from household appliances to complex aerospace machinery, reinforcing their unyielding significance in a rapidly evolving technological landscape.