When considering the construction and maintenance of complex assemblies, the often-overlooked component that can significantly influence the performance and durability is the extra-large flat washer. These seemingly simple yet crucial devices play a pivotal role in a wide array of applications, from automotive to aerospace industries. The expertise and experience drawn from using these washers can shed light on their critical attributes, benefits, and the necessity of choosing the right specifications tailored to specific projects.
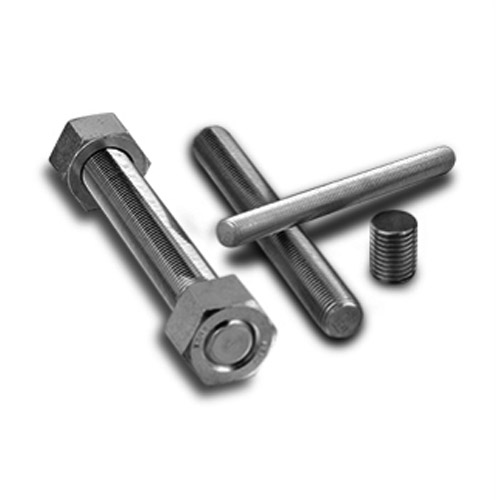
Extra-large flat washers serve as critical load distributors, a fact that underscores their importance in high-stress environments. They provide a broad surface area that helps prevent the embedding of the fastener head or nut into the substrate. In scenarios where large bolts or nuts are used to secure components, the load they exert can be immense. An extra-large flat washer effectively distributes this load uniformly, thereby protecting the structural integrity of the material. This is especially crucial in applications involving softer materials, such as aluminum or wood, which are susceptible to deformation under concentrated stress.
The specificity needed in choosing extra-large flat washers can't be overlooked. Industry experts emphasize that the material, thickness, and diameter of the washer are all pivotal in ensuring optimal performance. Stainless steel, for example, is a preferred material in environments prone to corrosion, while hardened steel might be chosen for applications requiring extreme strength. The determination of these factors should align with the detailed requirements of the intended application to ensure reliability and safety.
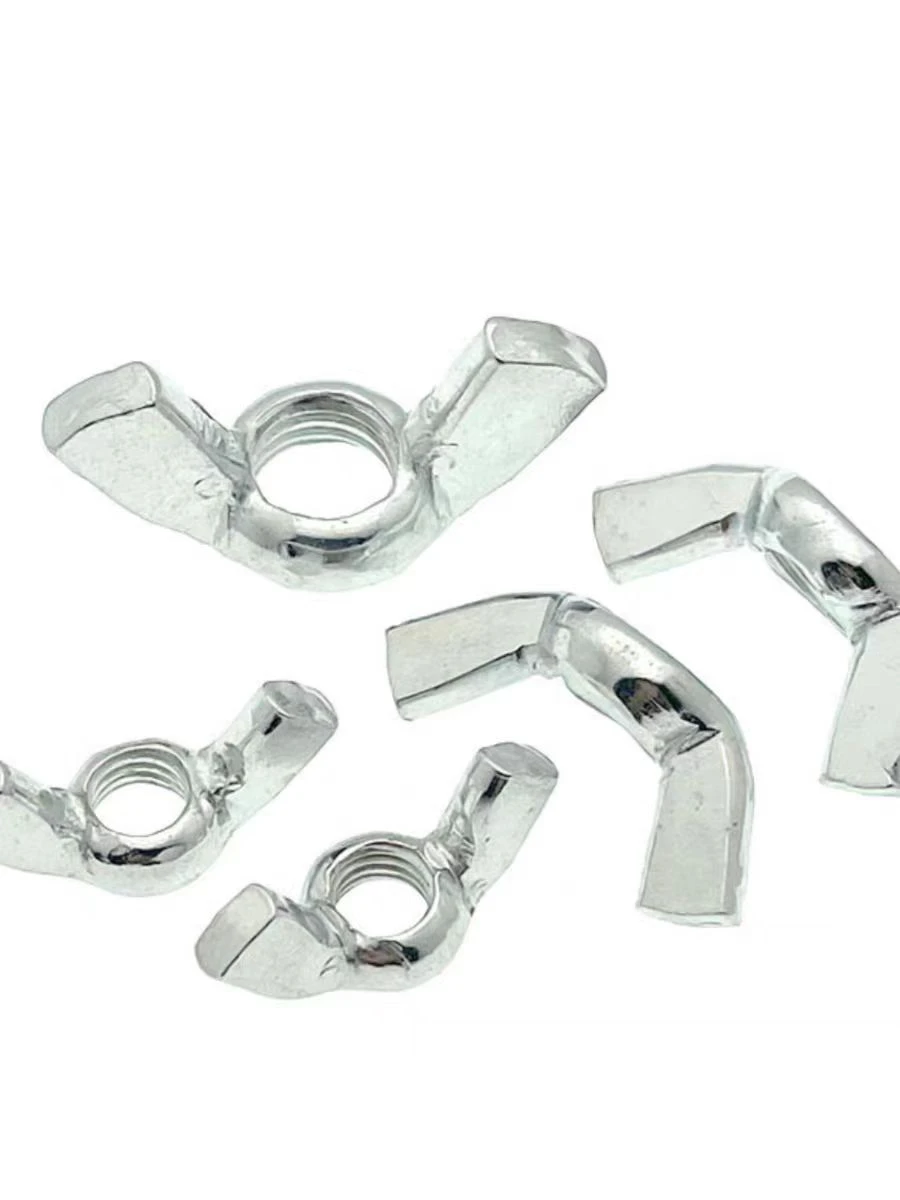
The authoritative standing of extra-large flat washers in industrial applications primarily stems from their versatility and reliability. In manufacturing, facilities often continue to rely on these washers to mitigate the risk of kinetic imbalances in machinery, acting as shock absorbers. Furthermore, their application in construction helps adhere to safety standards by securing structural elements and ensuring stability over time. In the automotive industry, extra-large flat washers provide foundational support in systems subject to persistent vibrations and pressure changes. Trusted manufacturers of these washers often provide detailed specifications and certifications, asserting their quality and compliance with industry standards.
extra large flat washers
When delving into the real-world experiences of using extra-large flat washers, numerous case studies exemplify their indispensable role. For instance, a leading aerospace company implementing these washers reported not just improved performance in their assemblies, but also a significant extension in the lifespan of their components. The real takeaway here is the tangible reliability and longevity these washers offer when chosen and applied correctly.
Credibility in the selection process of extra-large flat washers interconnects with the idea of trustworthiness in product descriptions and vendor transparency. Customers benefit significantly when manufacturers provide precise dimension details, weight tolerances, and material compositions. Information transparency bridges the gap between product efficacy and consumer trust, ensuring that the chosen washers meet or exceed the prevalent engineering and safety benchmarks.
As the technological landscape evolves, so too do the materials and designs of extra-large flat washers. Innovations in metallurgical processes contribute to developing washers with enhanced strength and anti-corrosive properties, beneficial in extreme conditions like offshore drilling and deep-sea exploration. This continual advancement underscores a critical aspect of expertise—staying abreast with the latest enhancements in mechanical fastening technology can lead to selecting a washer that not only meets but anticipates future application demands.
In summary, the decision-making process regarding extra-large flat washers should integrate deep technical knowledge, experience-based understanding, and a commitment to quality standards. When these elements align, the result is an assembly that upholds excellence in every phase of its lifecycle. Those responsible for the procurement and application of these washers should constantly engage with updates in technology and material science to ensure they leverage the best possible components for their projects.