In the world of engineering and construction, components that seem basic often play crucial roles in the stability and reliability of complex systems. The DIN 125 washer is one such component, embodying a seemingly simple design yet offering immense benefits across various applications. Understanding its advantages, applications, and differentiating factors will elevate your appreciation for this essential hardware.
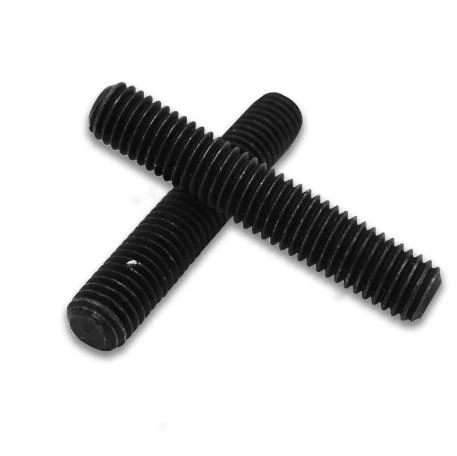
The DIN 125 washer is a highly respected element in mechanical and civil engineering sectors due to its simple yet effective design. This flat washer, standardized by the Deutsches Institut für Normung (DIN), is typically employed to distribute the load of a threaded fastener, such as a screw or nut, effectively reducing thread damage while providing a smooth surface to prevent loosening over time.
Manufactured mainly from a variety of materials such as stainless steel, brass, and galvanized steel, the DIN 125 washer ensures appropriate resistance to corrosion and environmental wear and tear, making it suitable for indoor and outdoor applications. The material choice is critical for determining its use in specific environments, thus underscoring its versatility and reliability.
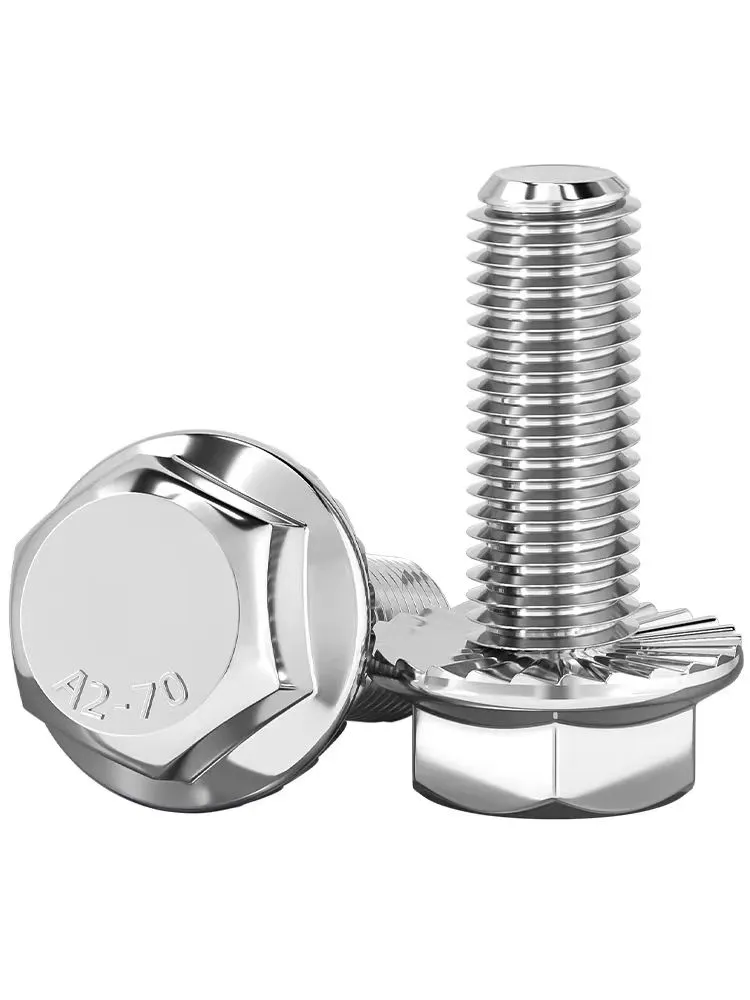
Experts in the industry emphasize the importance of choosing the right washer not only based on material but also on size and compatibility with corresponding fasteners. DIN 125 washers are known for their precise dimensions, critical for applications requiring exact load-carrying capability and stability. The washers come in a range of sizes, correlating with different bolt diameters, to ensure a perfect fit and optimal functionality.
The use of DIN 125 washers spans a multitude of sectors beyond engineering and construction. They are vital in automotive industries for creating secure configurations that withstand vibrations and dynamic forces. In electrical systems, these washers play a protective role by ensuring electrical insulation and preventing damage from excessive current or heat.
din 125 washer
Handling equipment with great expertise, professionals stress the ease of installation as a significant advantage of utilizing DIN 125 washers. Their seamless integration with existing hardware and minimal requirement for maintenance contribute significantly to efficiency and cost-effectiveness over product lifecycles.
Authoritative perspectives highlight the crucial advancements in washer technologies, emphasizing that, while DIN 125 washers follow international standards, ongoing refinements in design and material composition continue to attract specialists who are cognizant of preventing system failures in specialized and highly sensitive installations.
Trust in DIN 125 washers is further solidified by their consistent track record in upholding safety standards and reliability in critical infrastructure projects. Organizations count on these washers to perform under pressure, often literally, in demanding conditions. Quality assurance assessments are rigorous, ensuring each washer meets the stringent requirements laid down by international standards.
For maintaining a high standard of trustworthiness, consulting with suppliers and manufacturers with a solid reputation is recommended to ensure that the DIN 125 washers procured for any project meet specific requirements and deliver on their promise of quality and durability.
In summary, the DIN 125 washer exemplifies the perfect blend of simplicity and effectiveness. It stands as a testament to the power of well-designed tools in enhancing overall mechanical performance. Whether your application demands resistance to harsh environments or dependable load distribution, this small yet mighty component remains a staple of reliability, backed by robust international standards and industry expertise. Whether you’re an engineer, a manufacturer, or a procurement officer, acknowledging the nuanced excellence of DIN 125 washers will invariably contribute to the smooth functioning of technological systems.