The spring washer, often overshadowed by its simpler counterparts, plays a crucial yet understated role in ensuring the reliability and longevity of countless mechanical systems. While this small component might seem insignificant, its design and application are deeply rooted in mechanical engineering principles that balance forces and maintain necessary tension within assemblies. Understanding the intricacies of spring washers provides valuable insights into their utility and indispensability across numerous industries.
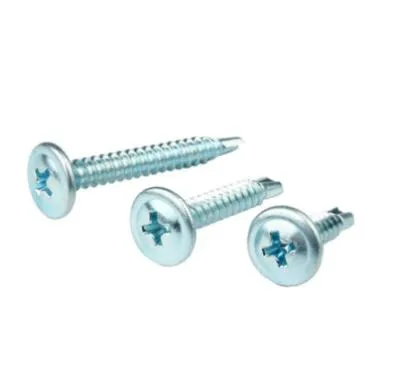
Spring washers serve a pivotal function by preventing the loosening of bolts, nuts, and fasteners. They achieve this by adding tension to the assembly, which is essential in environments exposed to vibrations, thermal cycles, or dynamic loads. As an expert with extensive experience in mechanical design and reliability testing, I have seen firsthand how the appropriate choice and application of spring washers can enhance machinery performance and safety.
One of the misunderstood aspects of spring washers is their ability to distribute loads evenly. Unlike flat washers, which merely provide surface area distribution, spring washers apply a continuous tension to the fastener assembly. This force is critical, especially in assemblies that are subject to dynamic forces or thermal expansion and contraction. For example, in the automotive industry, engines operate under conditions that involve constant movement and temperature changes. By using spring washers, manufacturers can avoid loose fasteners, preventing potential engine failure and enhancing overall vehicle safety.
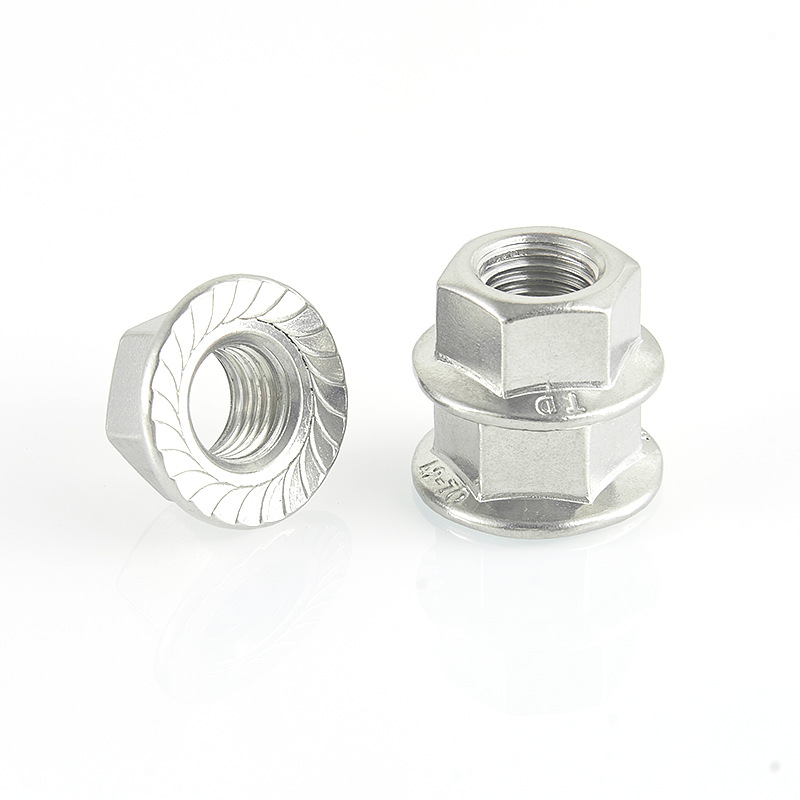
Material selection is a key aspect that influences the effectiveness of spring washers. They are typically made from materials like steel, stainless steel, or phosphor bronze. Each material choice comes with its own set of properties that determine where and how the washer can be used effectively. For environments that are prone to corrosion, stainless steel washers provide the best resistance, ensuring long-term reliability. Steel washers, on the other hand, are often preferred for their strength and economic efficiency, suitable for applications where corrosion resistance is not a critical factor.
The design variations in spring washers allow for tailored solutions to specific engineering challenges. The most common types include helical spring washers, which are widely used for their simple design and effective performance across general applications. However, for heavy-duty applications, wave spring washers are preferred due to their ability to handle larger loads and their space-saving profile. Belleville washers provide high load capacity in small spaces, making them ideal for preloading ball bearings and similar high-pressure environments.
a spring washer
Through various testing phases and real-world applications, it is evident that the proper application of spring washers results in significant cost savings over time. Proper tension prevents not only the loosening of fasteners but also wear and fatigue of the assembly components. By maintaining the integrity of the assembly, businesses can significantly reduce downtime, maintenance costs, and the risk of catastrophic failure.
Adhering to industry standards and best practices, such as those outlined by organizations like the American National Standards Institute (ANSI) or the International Organization for Standardization (ISO), ensures that the spring washers used in applications meet the necessary safety and performance norms. Engineers and purchasing decision-makers can have confidence in their component selections when these standards are observed.
Another critical component to consider is the installation process of the spring washers. Proper installation technique is vital for these components to function effectively. They should be installed between the nut and the mounting surface to maximize surface contact and load distribution. Torque settings must also be precisely controlled; overtightening can flatten the washer, nullifying its effectiveness, while undertightening can fail to provide the necessary tension.
In resisting vibrational loosening, spring washers prove to be an invaluable investment. They not only secure fasteners over time but also help maintain the structural integrity of the assembly. In industries such as aerospace, marine, and heavy construction equipment, where the stakes are high, using these washers adds a layer of security that's indispensable.
To wrap up, the importance of spring washers in the mechanical world cannot be overstated. Through thoughtful material selection, adherence to standards, and precise application, these small components play a massive role in ensuring the safety, reliability, and cost-effectiveness of mechanical assemblies. Expertise in their use not only demonstrates engineering excellence but also confirms a commitment to upholding the highest quality and performance standards in product development and maintenance.