The flange nut, particularly the specification labeled as 9 16 18, is an integral component in many industrial and mechanical applications due to its unique configuration designed to enhance stability and distribute pressure evenly during fastening. Understanding the intricacies and applications of these nuts can significantly enhance both the efficiency and safety of your project, whether in construction, automotive, or machinery settings.
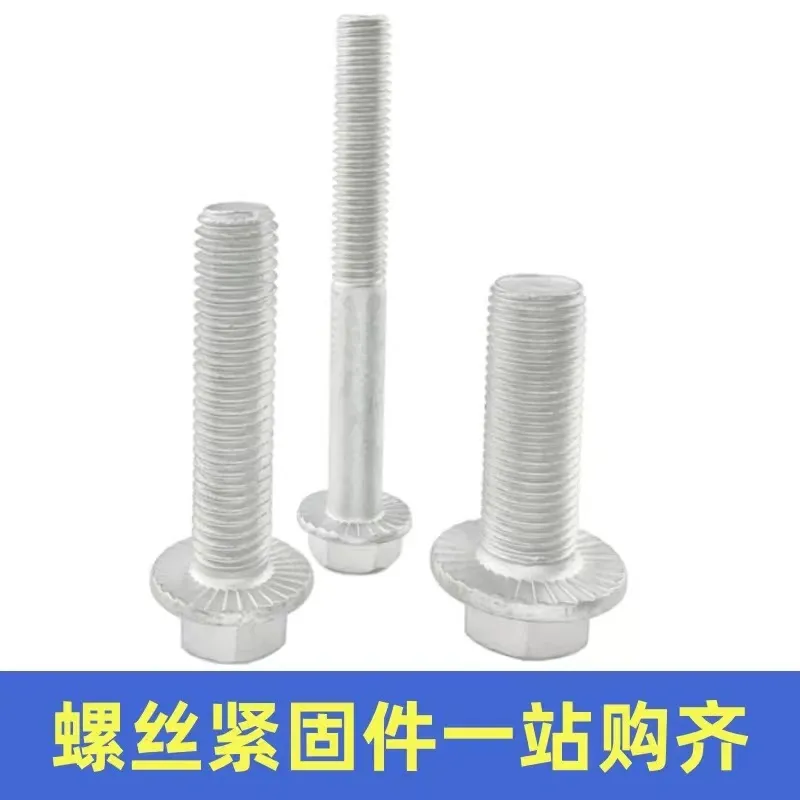
One of the most compelling aspects of flange nuts is their structural design. The 9 16 18 flange nut refers to its dimensions and thread pitch, which are critical in ensuring that it fits correctly within the designated bolt. The '9/16' denotes the nominal diameter, a middle-range size common in heavy-duty applications, allowing for a balance between strength and manageability. The 18, on the other hand, refers to the threads per inch (TPI), indicating a fine thread profile that enhances grip and loosening resistance. This is especially crucial in applications where vibration might cause regular nuts to back off or release, posing safety risks or mechanical failure.
From an experiential standpoint, users who have handled these nuts in an array of scenarios often commend their reliability. In real-world tests within automotive constructions, for example, the 9 16 18 flange nut has shown minimized slippage and enhanced load distribution, effectively preventing stress concentration points that often lead to material fatigue or failure. This quality is underlined by the strategic design of the flange, a wide base that acts as an in-built washer, spreading the load across a broader surface.
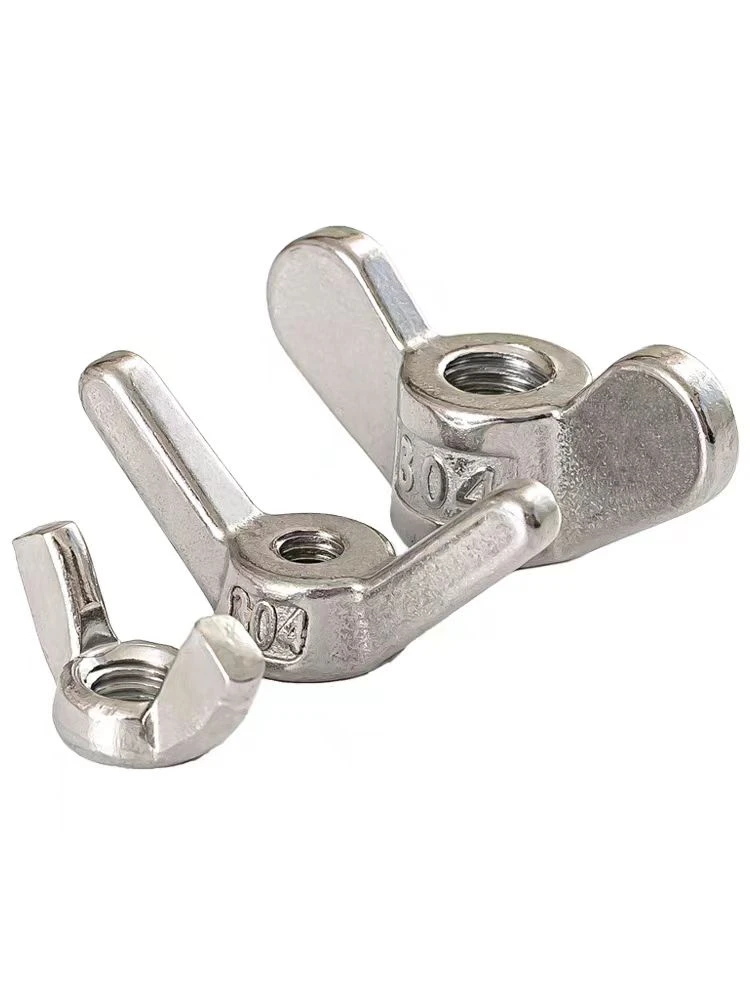
In terms of expertise, engineers and technicians recommend these nuts for environments demanding rigorous durability and stability. The composition of the flange nut typically involves high-grade materials such as stainless steel or chrome alloys, making it resistant to corrosion and deformation even under harsh conditions. This material advantage, combined with precision manufacturing, ensures that each nut meets stringent quality standards, vital for maintaining the structural integrity of any assembly.
9 16 18 flange nut
Moreover, when considering authoritativeness and trustworthiness in product selection, it is important to note the compliance of flange nuts with industry standards. Standardized codes and operational guidelines offer a benchmark for quality assurance. Users are advised to verify that their chosen 9 16 18 flange nuts adhere to relevant manufacturing and material certifications. This guarantees that the product not only meets the expected performance metrics but also aligns with safety mandates, ensuring a trustworthy application.
Additionally, collaboration with reputable manufacturers and suppliers, who can provide comprehensive support and documentation, amplifies both the authority and the trust consumers can place in these nuts. These providers often conduct extensive R&D to test product reliability under a spectrum of conditions, contributing to a repository of data that enhances user confidence in the product's performance.
In conclusion, the 9 16 18 flange nut exemplifies a fusion of design sophistication and practical application. Its ability to withstand mechanical demands while providing stability makes it indispensable in numerous fields. By appreciating its detailed specifications and relying on verified products from trusted sources, users can optimize their project outcomes, ensuring durability and safety in every application. This approach not only aligns with best practices for product selection but also reinforces a commitment to quality and excellence in mechanical engineering.