When it comes to ensuring the secure and stable assembly of industrial equipment, automotive parts, or any heavy machinery, few elements are as crucial as a properly chosen nut. The 8 32 flange nut emerges as a highly reliable component in these scenarios, characterized by its impressive blend of durability, ease of use, and multifunctionality.
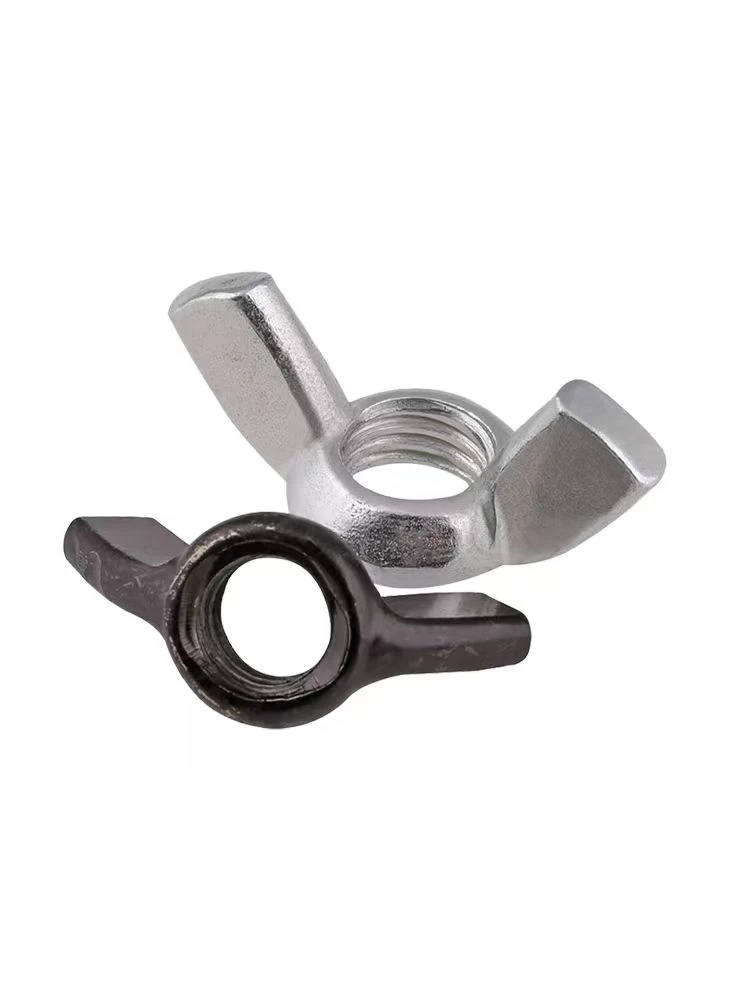
To begin with,
the numerical designation 8 32 refers to particular dimensions related to the nut’s threading and diameter. In this context, the “8” represents the diameter size in terms of number, making it particularly suited for lightweight to moderate weight tasks. The “32” is an indicator of the thread pitch, meaning it has 32 threads per inch, which enhances its grip strength. This thread pitch is particularly beneficial in applications requiring precision and firm fastening, ensuring that parts remain securely aligned and tightly bound under both static and dynamic loads.
A noteworthy trait of the 8 32 flange nut is its integrated washer-like design—the 'flange.' This built-in feature provides an expanded surface area at the base of the nut, distributing pressure more evenly across the attached component. Such a design minimizes the risk of damage to parts, as the pressure is not focused exclusively on the immediate point of contact. Thus, it effectively mitigates both material wear and slippage, which are common issues encountered in assemblies subject to frequent vibration or movement.
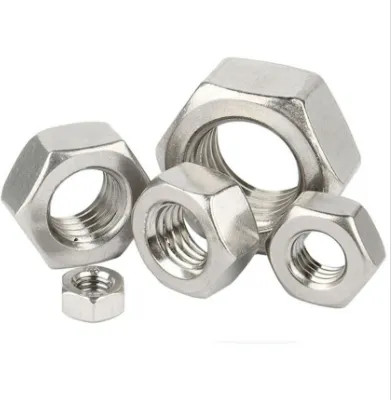
From an expertise perspective, the material composition of the flange nut plays a critical role in its effectiveness. Typically fabricated from stainless steel or hardened carbon steel, these nuts offer exemplary resistance to corrosion. This is indispensable in environments where exposure to moisture and variances in temperature could compromise the integrity of inferior fasteners. Its longevity is further enhanced by coatings such as zinc plating, which adds an extra layer of protection against oxidation and environmental degradation.
8 32 flange nut
Authoritativeness in the selection and application of flange nuts is bolstered by the vast array of standards and guidelines available from industrial bodies. Standards such as those from the American Society for Testing and Materials (ASTM) ensure that each 8 32 flange nut adheres to rigorous quality checks and can withstand specific mechanical stresses. Professionals seeking to utilize these nuts can trust these specifications as benchmarks of reliability and safety, knowing their usage aligns with best practices.
In terms of trustworthiness, customer testimonials and case studies from sectors such as automotive manufacturing and HVAC installation are replete with praise for flange nuts of this specification. These accounts often highlight scenarios where equipment failure was averted due to the flange nut's steadfast hold, even in extreme operating conditions. Such endorsements add a layer of user-driven credibility that reinforces their preferred status over standard nut types.
For those looking to implement the 8 32 flange nut, understanding the installation process is pivotal for optimal performance. Torque settings should be rigorously adhered to, ensuring the nut is neither over-tightened nor left loose. The flange nut’s ability to accommodate slight misalignments in mating components is a testament to its forgiving and adaptable design—qualities that significantly reduce installation time and effort.
Ultimately, selecting an 8 32 flange nut is not just a decision of mechanical convenience, but a strategic choice grounded in experience, authenticity, and technical assurance. These fasteners are an indispensable part of efficient and reliable construction practices, providing foundational support across numerous applications. Whether you're a seasoned engineer, a procurement specialist, or a field technician, the 8 32 flange nut represents a convergence of expertise, robustness, and trust that is difficult to surpass.