The 7/8 flange nut is more than just a functional piece of hardware; it's an engineering marvel that combines innovation, efficiency, and reliability. Understanding the intricacies of this particular component can significantly enhance its application in various fields.
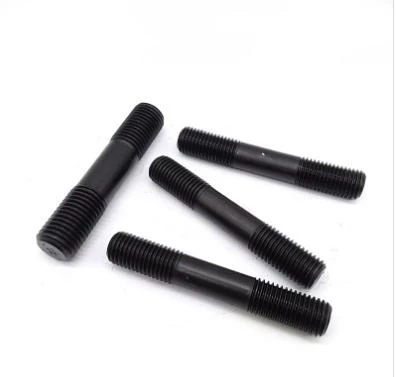
When it comes to real-world application, the 7/8 flange nut is a cornerstone of mechanical assemblies requiring secure and reliable fastening. Flange nuts are particularly advantageous due to their built-in washer surface, which allows for an even distribution of pressure, reducing the risk of damage to the connected parts. This feature is a testament to its engineering excellence, ensuring long-term stability and performance.
The expertise behind flange nuts involves metallurgy, precision engineering, and a keen understanding of the demands placed upon fasteners in dynamic environments. Typically crafted from high-grade steel due to its strength and durability, these nuts undergo rigorous testing to ensure they meet industry standards. This guarantees that they can withstand immense pressure and torque without deforming or losing grip — a critical consideration in automotive and industrial applications where safety is paramount.
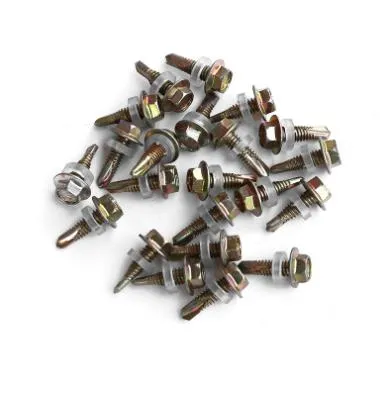
Authoritative insights into the use of 7/8 flange nuts reveal their versatility and essential role in ensuring the integrity of mechanical systems. Experts in the field advocate for their use in applications where vibration is a concern. The flange design permits the nut to lock in place more effectively than standard nuts, reducing the chance of loosening under stress. This makes them indispensable in the construction of vehicles, machinery, and infrastructure, where reliability is crucial.
7 8 flange nut
Trustworthiness in using flange nuts is reinforced by a proven track record of performance. Manufacturers who adhere to strict quality control measures ensure that these fasteners perform under harsh conditions, providing peace of mind to engineers and end-users alike. Certification to ISO standards and other industry benchmarks further validates their reliability, making them a trusted choice for professionals worldwide.
In the realm of product applications, understanding the nuances of selecting the right 7/8 flange nut is crucial. Factors such as the material of the connecting components, the environmental conditions, and the specific load requirements must be considered. Flange nuts can be found in various finishes, including zinc-plated and stainless steel options, each offering unique benefits in terms of corrosion resistance and aesthetics. Consulting with engineers or tapping into manufacturer expertise can provide additional guidance tailored to specific needs.
Moreover,
the application process of a flange nut demands a certain level of skill. Proper torque application is crucial to optimize the performance of the nut in its assembly. Over-tightening or under-tightening can lead to complications such as component failure or disassembly. Therefore, using calibrated tools and following manufacturer guidelines is essential to uphold the performance and longevity of the fastening system.
In conclusion, the 7/8 flange nut stands out as a model of reliability and efficiency in the fastener industry. Its design, backed by engineering expertise and quality manufacturing processes, positions it as an indispensable component in various technical and industrial applications. By emphasizing the importance of expertise, reliability, and precision in its use, professionals can leverage the full potential of the 7/8 flange nut, enhancing the safety and integrity of their projects.