Zinc washers are a crucial component in various mechanical and structural applications, prized for their durability and corrosion resistance. However, the effectiveness of these washers can be compromised by rust, a common issue that both novices and professionals encounter. This article seeks to provide valuable insights into the properties of zinc washers, their susceptibility to rust, and strategies to mitigate corrosion effectively.
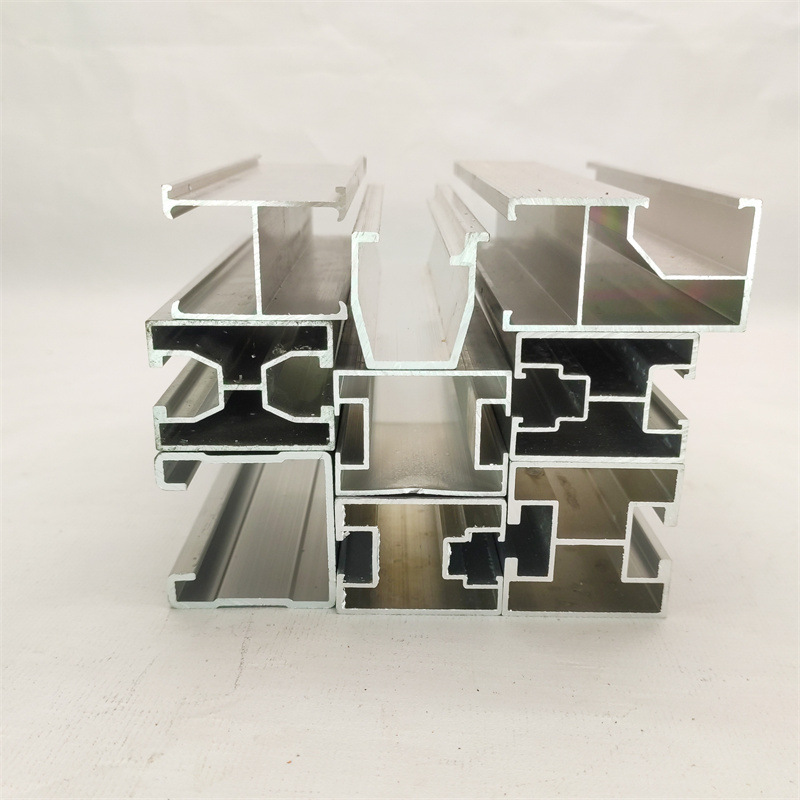
Understanding the Basics of Zinc Washers
Zinc washers are typically used to distribute the load of threaded fasteners like screws and bolts. They function as a buffer to prevent damage to the connected surfaces and ensure a more secure assembly. The primary advantage of using zinc lies in its resistance to corrosion. When zinc is exposed to air, it reacts with oxygen to form zinc oxide, which further reacts with water to create zinc hydroxide. This compound eventually forms a stable, protective layer of zinc carbonate, preventing further oxidation.
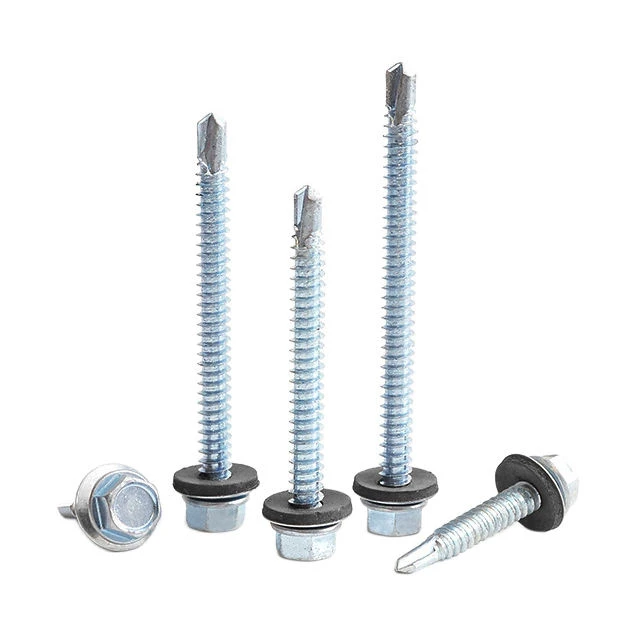
Analyzing the Susceptibility to Rust
Despite zinc's inherent resistance to rust, there are conditions where corrosion can still occur.
Understanding these conditions is crucial for anyone using zinc washers in their projects. One primary factor is the pH level of the environment. Highly acidic or basic environments can accelerate the corrosion process even on zinc-coated surfaces. Furthermore, the presence of salts, particularly in coastal or marine applications, can lead to rapid degradation through processes like galvanic corrosion.
Another notable factor is mechanical wear. Zinc coatings can degrade over time due to friction and pressure, exposing the underlying metal to the elements. This exposure can initiate rust, especially in environments with high humidity or heat.
Proactive Measures to Prevent Rust
For experts looking to maintain the integrity of zinc washers in their applications, several preventative strategies can be employed. The first method is selecting the right type of zinc coating. Galvanized zinc washers, for example, provide a thicker layer of protection compared to electroplated zinc washers. This added thickness can significantly enhance durability and rust resistance in harsh environments.
zinc washer rust
Using additional protective coatings, such as chromate or phosphate treatments, can further bolster the resistance of zinc washers against rust. These coatings act as additional barriers, reducing the risk of corrosion.
It is also critical to ensure proper installation practices. Over-tightening washers can damage the zinc coating, leaving metal exposed to potential rust. Utilizing torque specifications as recommended by manufacturers ensures an even distribution of force and preserves the integrity of the zinc layer.
Regular Maintenance and Inspection
Consistent maintenance is essential in extending the lifespan of zinc washers. Regular inspections can identify the early signs of rust or corrosion, allowing for timely intervention. Cleaning the washers to remove any accumulated dirt, grime, or chemicals can mitigate the risk of corrosion. Employing rust inhibitors or anti-corrosive sprays can also serve as a preventative measure when applied periodically.
Innovations and Future Trends
As technology advances, innovations in material science are paving the way for more robust solutions to combat rust effectively. Researchers are exploring nanocoatings and other advanced materials that promise to enhance the corrosion resistance of zinc washers exponentially. These developments hold the potential to revolutionize industries reliant on secure, long-lasting fasteners.
Conclusion
While zinc washers offer substantial benefits in terms of corrosion resistance, understanding the conditions under which rust can occur and implementing proactive measures is crucial. Whether for construction, automotive, or industrial applications, the longevity and reliability of zinc washers largely depend on combining the right materials, coatings, and maintenance practices. By staying informed and adapting to emerging technologies, professionals can ensure the optimal performance of zinc washers in any environment.