Washer DIN 125 A 8.4 A Comprehensive Guide
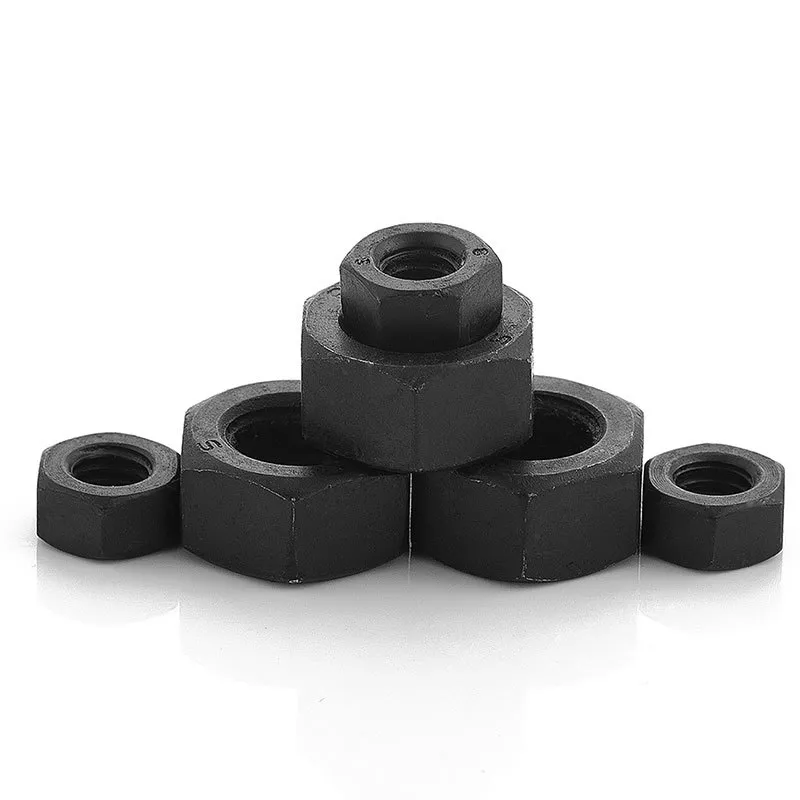
Washers are essential components in fastening applications, providing stability, distributing load, and preventing wear and damage to surfaces. Among various standards, the DIN 125 A 8.4 washer stands out due to its specific attributes and applications in industries. This article delves into the intricacies of the DIN 125 A 8.4 washer, offering insights based on real-world experiences, expert knowledge, and an authoritative understanding of its applications.
Understanding DIN 125 A 8.4 Specification
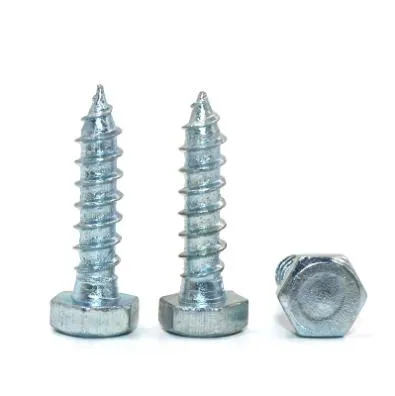
DIN, short for 'Deutsches Institut für Normung', sets the national standards in Germany. DIN 125 is a standard for flat washers, with the 'A' designation indicating a specific type of flat washer without chamfer. The number '8.4' refers to the internal diameter, indicating that these washers are ideally suited for M8 bolts and screws. Their standardized specifications ensure compatibility and interchangeability in manufacturing and assembly processes across the globe.
Material and Manufacturing
Typically crafted from stainless steel or zinc-plated steel, the choice of material for DIN 125 A 8.4 washers depends on the environmental conditions of the application. Stainless steel provides excellent corrosion resistance, making it suitable for outdoor or marine applications where exposure to moisture is prevalent. In contrast, zinc-plated steel offers sufficient protection against rust for general indoor applications, often at a lower cost.
The manufacturing process ensures precision and adherence to dimensional tolerances, crucial for any component integrated into engineering applications. With advancements in CNC machining and automated stamping, manufacturers produce these washers with high consistency and quality.
Applications and Benefits
When used correctly, the DIN 125 A 8.4 washer enhances the lifespan of mechanical assemblies. Real-world applications span automotive, aerospace, construction, and machinery industries. Their primary function is to increase the surface area in contact with the fastener, thereby distributing the applied load more evenly. This not only prevents damage to the assembly surface but also minimizes the risk of fastener loosening due to vibrations – a critical factor in machinery and automotive applications.
washer din 125 a 8.4
From an expert perspective, the strategic placement of these washers can effectively mitigate issues related to thermal expansion and contraction in various materials, further solidifying their role in high-stress environments like engines and heavy machinery.
Installation Insights
Trustworthiness in installation comes from proper technique and understanding the dynamics of washer use. It is pivotal to ensure that the washer's diameter matches the bolt diameter to prevent unnecessary play that could compromise the assembly integrity. Additionally, using a torque wrench during installation helps achieve the right amount of pressure, safeguarding against over-tightening that can lead to material deformation or washer failure.
Expert installers recommend a torque value slightly lower than the maximum capacity of the fastener to maintain structural integrity over prolonged periods. Applying thread locking compounds can further enhance secure fastening in high-vibration environments, complementing the function of the washer.
Maintenance and Longevity
Based on collective experience, regular maintenance checks that include washers can preemptively identify early signs of wear or corrosion, ensuring longevity and reliability of the overall structure. Especially in harsh environments, periodic inspection and timely replacement of worn washers prevent escalation of minor issues into major mechanical failures.
In situations involving exposure to corrosive elements or extreme temperature variations, selecting the right materials and conducting frequent assessments can greatly enhance durability. Proper documentation of maintenance checks provides a trustworthy account of equipment history, aiding in predictive maintenance schedules and operational safety.
Conclusion
DIN 125 A 8.4 washers, while seemingly simple components, play a crucial role in enhancing the stability and durability of assemblies across various industrial applications. A deep understanding of their specifications, backed by expert knowledge and authentic experience, ensures their effective utilization. By focusing on material selection, precise installation, and regular maintenance, users can significantly extend the life of assemblies and equipment, maintaining structural integrity and operational efficiency. Through this comprehensive guide, the importance of these washers is underscored not just in their function, but in their contribution to the broader scheme of engineering solutions.