The term ss nut may not be immediately recognizable to everyone, but in specialized industries such as manufacturing, automotive, and marine engineering, it holds significant importance. As a corrosion-resistant hardware component, the stainless steel (ss) nut is crucial in environments exposed to moisture, chemicals, and extreme temperatures.
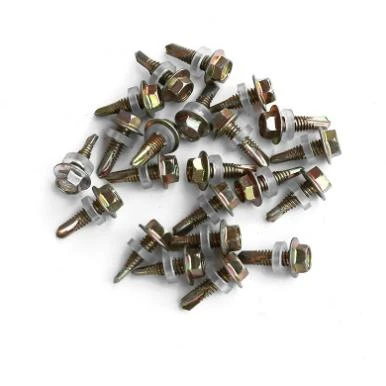
Stainless steel nuts are made from an alloy composed primarily of iron, chromium, and nickel. The inclusion of chromium, typically around 10.5% or more by mass, enhances the corrosion resistance of these nuts. This corrosion resistance is a defining attribute that makes ss nuts particularly useful in harsh conditions where other materials would degrade quickly.
In industries such as construction and transportation, the durability and reliability of fasteners are paramount.
Stainless steel nuts stand out for their strength and stability. They maintain their structural integrity over long periods, reducing maintenance costs and downtime significantly. This makes them an excellent choice for large infrastructure projects such as bridges, highways, and skyscrapers. Contractors who have switched to stainless steel hardware often report a noticeable improvement in project lifespan and a reduction in overall repair needs.
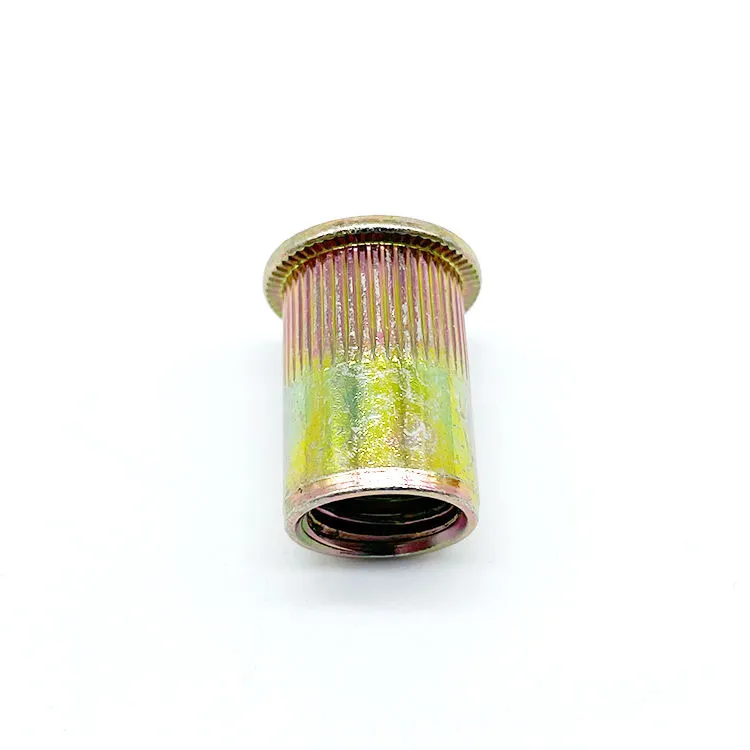
The use of ss nuts extends into the automotive industry, where engineers value their ability to withstand the rigors of engine compartment conditions. In applications where car parts are exposed to high heat and chemical reactions, such as in exhaust systems, using stainless steel nuts ensures that vehicular components stay secure without material breakdown. This leads to a decrease in part replacements and increased vehicle reliability.
For marine engineering, ss nuts are essential due to the constant exposure to salty, humid environments. Their exceptional resistance to rust is crucial for parts used in ships, docks, and offshore platforms. Marine engineers often select these nuts for their resilience, knowing the hardware won’t compromise the structural safety and efficacy of marine constructs.
ss nut
In a case study focusing on the uses of ss nuts in wind turbine maintenance, experts have noted a marked improvement in material longevity when switching to stainless steel fasteners. Harsh winds and potential icy conditions target turbine assemblies relentlessly. When equipped with stainless steel nuts, turbines not only function more efficiently but also require less frequent servicing. This efficiency directly correlates to lower operating costs and increases in energy production uptime.
From a scientific perspective, the grain structure of stainless steel plays a significant role in its performance characteristics. Metallurgists highlight the metal's passivation layer—a thin film that shields against oxidation—as a primary factor in its enduring usage. This layer, self-repairing when damaged, certifies stainless steel nuts as trustworthy over time, imbuing projects with both safety and reliability.
Today, companies opting for sustainable practices find in stainless steel a recyclable material that aligns with their eco-friendly goals without compromising on quality. Stainless steel nuts facilitate the design of structures that are not only resilient but also respectful of the environment. By choosing these fasteners, businesses and engineers contribute to a reduction in resource consumption over time.
For those requiring secure, reliable, and long-lasting fasteners, stainless steel nuts present an authoritative solution. Through a blend of robust material characteristics and trust-earned expertise in real-world applications, ss nuts continue to be a preferred choice across multiple high-stakes industries. This investment in quality translates to peace of mind, knowing that the integrity of the construction lies in the hands—or in this case, the threads—of these little yet powerful components.