Flat washers and lock washers are two essential components in the toolbox of any tradesperson, builder, or DIY enthusiast. While they might seem small and inconspicuous, their roles are crucial in ensuring the stability and integrity of assembled structures. To fully appreciate their importance, it’s necessary to delve into their unique characteristics, applications, and benefits.
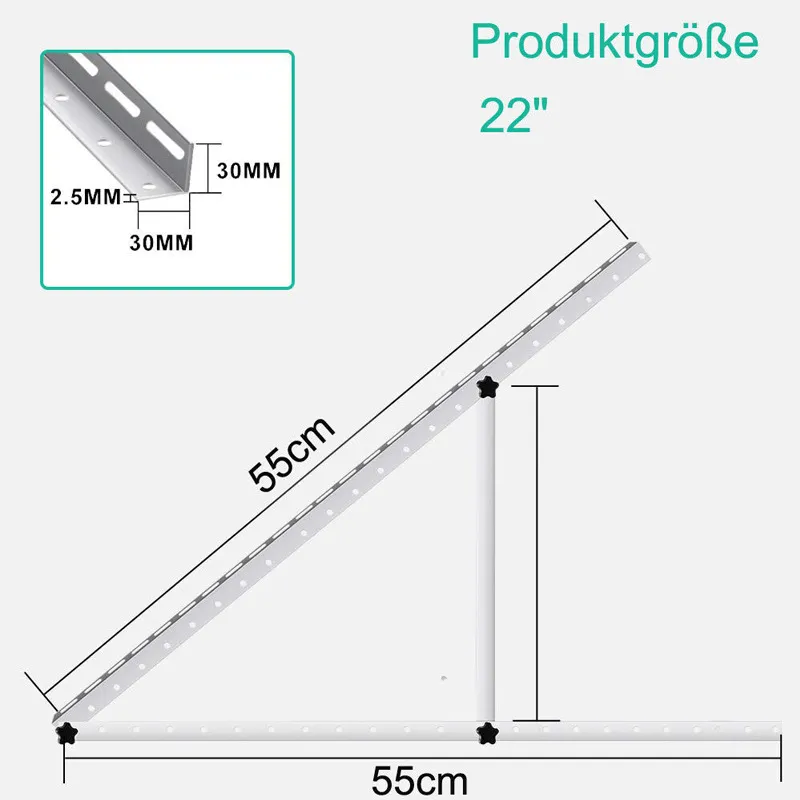
Flat washers, sometimes referred to as plain washers, serve the primary purpose of distributing the load of a threaded fastener, such as a bolt or a screw. Made typically from metal or plastic, flat washers protect the surface of the assembled material from damage while also reducing the risk of the fastener loosening due to surface friction. These washers are particularly beneficial in applications involving softer materials like wood or plastic, which could be damaged by the direct pressure of a bolt head or nut. Furthermore, using flat washers helps in reducing the likelihood of fastener pull-through, providing a more stable and durable assembly.
On the other hand, lock washers have a very different function centered around securing fasteners to prevent them from loosening in environments subject to vibrations or dynamic loads. Lock washers are designed in various shapes, such as split, tooth, or wave, each offering unique locking mechanisms. For instance, split lock washers utilize their helical shape to exert tension against the nut or bolt, effectively preventing rotational movement. Tooth lock washers, whether internal or external, use their serrated surfaces to bite into the nut and material surface, securing the fastener in place.
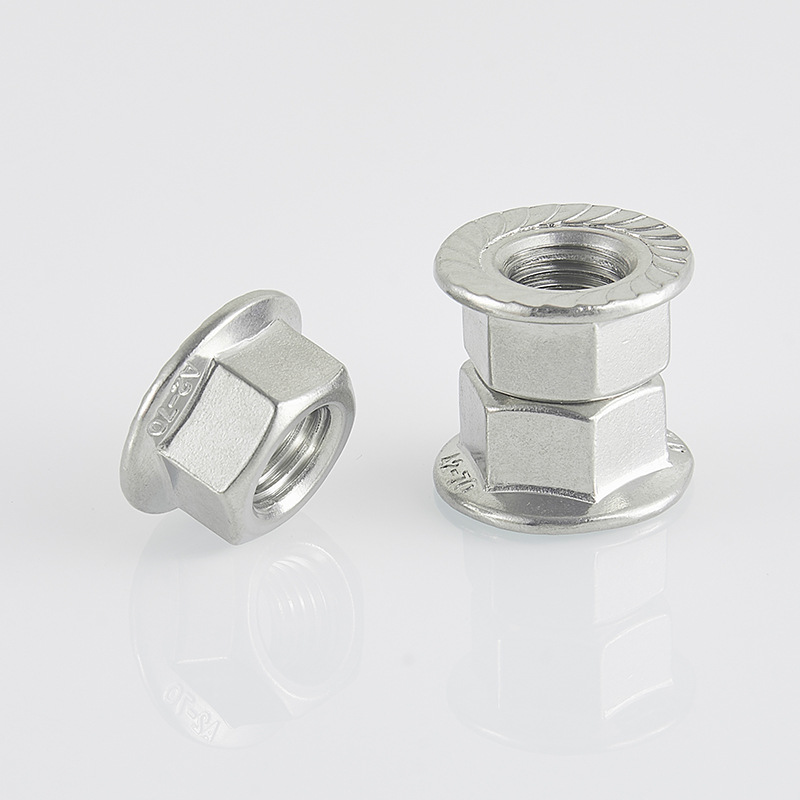
The expertise required in choosing between flat and lock washers involves understanding the specific demands of the application. For stationary assemblies, where the paramount concern is protecting the material surface, flat washers are usually the go-to solution. They provide a broader surface area in contact with the material, ensuring even load distribution. Meanwhile, in scenarios where the assembly is susceptible to vibrations—such as in automotive or machinery applications—lock washers offer added security by maintaining tension on fasteners, thereby inhibiting them from loosening over time.
flat washer lock washer
Nothing emphasizes the authoritativeness of these washers more than their extensive range of materials and finishes, each catering to different environmental and mechanical needs. Stainless steel washers, for example, offer excellent corrosion resistance, making them ideal for marine or outdoor applications. In contrast, brass washers are often preferred in environments where conductivity and low friction are desired, such as in certain electrical assembly applications.
Trust in the use of flat and lock washers has been established through decades of successful application in critical industries such as aerospace, automotive manufacturing, and construction. These washers have become a staple in these sectors not only because of their reliability but also due to the ease with which they can be installed and maintained. Moreover, their ability to meet various industrial standards ensures that they comply with rigorous safety and quality requirements.
In conclusion, the role of flat and lock washers in ensuring the integrity and reliability of mechanical assemblies cannot be overstated. Their unique properties cater to different application needs, providing solutions that enhance the life expectancy and performance of products. By understanding their distinct characteristics and recognizing the scenarios in which they excel, users can make informed decisions, enhancing the effectiveness and safety of their projects. With a commitment to quality and performance, these small components continue to underscore their importance in the broader context of engineering and assembly.