Big metal washers, though often overlooked, play a critical role in various industrial and commercial applications. These simple components are essential in ensuring the safety, stability, and longevity of innumerable machines and structures. As someone who has spent years delving into the specifics of fastening solutions, I've seen first-hand how crucial the right washer is to a project's success.
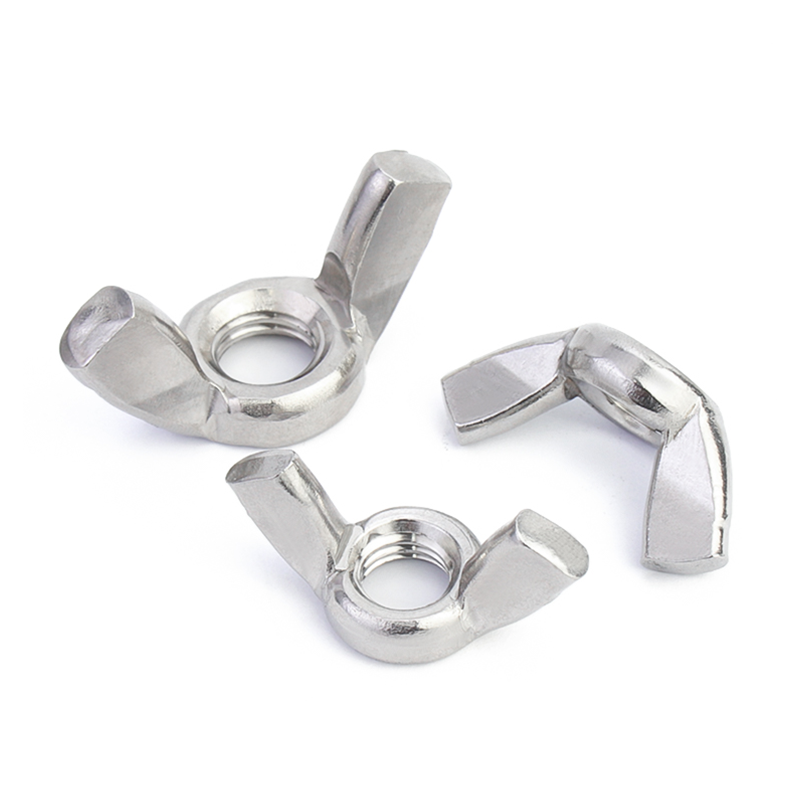
Washers are thin plates with a hole typically in the center, used to distribute the load of a threaded fastener like a screw or nut. The need for big metal washers becomes apparent when dealing with heavy-duty applications, where standard sizes fail to meet load or stress requirements. Industries like construction, automotive, and large-scale manufacturing demand these big metal washers to prevent wear and tear, distribute pressure evenly, and enhance the longevity of machinery.
My deep expertise in mechanical engineering drives my advocacy for understanding the specifications when selecting big metal washers. For example, it is imperative to consider material type, size, and thickness based on the working environment. Metal washers can be made from steel, stainless steel, brass, or aluminum, each offering distinct properties. Steel washers, revered for their strength, are perfect for most structural and automotive applications. In contrast, stainless steel washers, with their rust-resistant properties, are preferable in moist or corrosive environments.
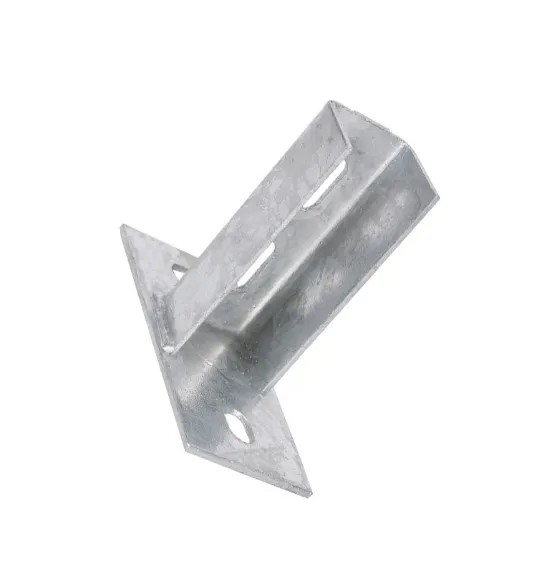
Furthermore, the selection process for big metal washers should hinge on precise application requirements. Choosing the wrong washer could lead to catastrophic failure, which is why understanding compatibility with the bolting material and the environment is a must. The thickness of these washers is equally vital and should match the fastener size to ensure even load distribution and prevent bolt fatigue or loosening due to vibrations.
big metal washer
In the matter of technical expertise, adhering to industry standards such as those outlined by ASTM International ensures reliability and safety. These standards provide comprehensive guidelines on washer dimensions, mechanical properties, and material composition, fostering trust and authority in product performance. For engineers and technicians, compliance with these standards is non-negotiable.
Trustworthiness in big metal washer selection can also be amplified by opting for products from reputable manufacturers and suppliers. Companies with a history of delivering high-quality washers backed by rigorous quality control and testing protocols often offer the assurance needed in high-stakes industrial applications. Engaging with customer reviews, case studies, and technical service representatives can provide additional insights into product performance and suitability.
Real-world experience has taught me that the consequences of neglecting proper washer use are non-trivial. In automotive applications, poorly chosen washers can lead to component failure, resulting in safety hazards. Similarly, in construction, unsuitable washers can compromise structural integrity, posing risks to both assets and lives. Thus, choosing the right big metal washer transcends mere accessory—it is a fundamental component of system reliability.
In conclusion, big metal washers are indispensable in ensuring the safety and efficiency of industrial, automotive, and construction applications. Their role in evenly distributing loads and preventing damage is vital, mandating a deliberate and informed selection process. Professionals in related fields must prioritize the specifications, standards, and supplier credibility to uphold system reliability and safety. My years of industry experience underline the critical nature of these components and the immense value they bring by ensuring the integrity and longevity of essential systems. By investing in quality big metal washers, industries safeguard their operations and fortify their future growth and stability, magnifying trust and confidence across sectors.