Cone washers play a crucial role in a wide range of mechanical and structural applications, providing essential load distribution and alignment functions that contribute significantly to the longevity and performance of various systems. Despite their seemingly simple design, cone washers are engineered components that demand a thorough understanding of their properties and applications to utilize them effectively.
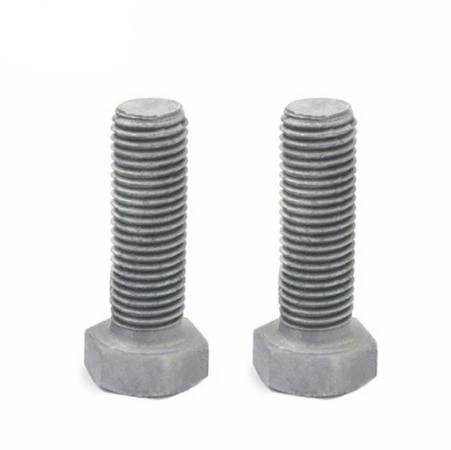
Cone washers, also known as conical washers, are characterized by their unique shape which resembles a truncated cone.
This design is particularly beneficial when it comes to distributing loads over a wider area compared to flat washers. The conical design ensures that the washer can absorb impacts, vibrations, and thermal expansions in applications, thus enhancing the stability and performance of the assembled structure. Made from a variety of materials, including stainless steel, carbon steel, and various alloys, cone washers are well-suited for both standard and high-stress applications.
A critical application of cone washers is in the aerospace and aviation industry. Here, these components are often employed in fastening systems where thermal and mechanical stresses are frequent. For instance, when used in jet engines, cone washers accommodate thermal expansion and contraction due to fluctuating temperatures and pressures, preventing hardware failure that could lead to catastrophic outcomes. Their ability to manage such stresses underscores their importance in providing reliability and safety in high-stakes environments.
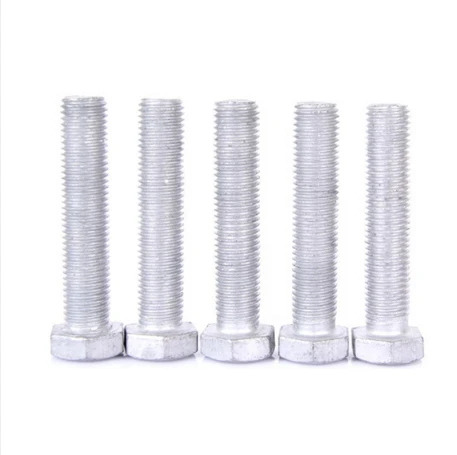
In the automotive industry, cone washers play an instrumental role in ensuring the longevity and performance of vehicles. They are utilized in suspension systems, engine assemblies, and braking mechanisms. For instance, in a vehicle's suspension system, cone washers help in damping vibrations and absorbing shocks from uneven road surfaces. This not only enhances passenger comfort but also prolongs the lifespan of the vehicle by reducing wear and tear on vital components.
From a construction perspective, cone washers are invaluable in steel structures, particularly in seismic zones where buildings and bridges are subjected to dynamic forces. The washers facilitate controlled deformation, helping to absorb energy during seismic activities and preventing structural failures. In such applications, the quality and specification of cone washers are critical, often necessitating stringent testing and compliance with industry standards to ensure maximum reliability and safety.
cone washers
Material choice for cone washers is another vital consideration that impacts their performance. Stainless steel is a prevalent choice due to its excellent corrosion resistance and strength, making it suitable for marine and outdoor applications where environmental conditions can lead to premature failure of lesser materials. Alloy steels, with added elements like chromium and molybdenum, provide enhanced strength and fatigue resistance, making them ideal for high-load applications such as automotive and aerospace sectors.
Installation practices and maintenance routines are equally important in maximizing the efficacy of cone washers. Proper alignment and torque during installation prevent undue stress and potential failure. Regular inspections ensure that washers remain in good condition, maintaining the integrity of the assemblies they support. Routine maintenance can prevent costly downtime and repairs, further demonstrating the significance of these small yet mighty components.
With advancements in material science and engineering, newer versions of cone washers are being designed to withstand even more strenuous conditions. Innovations such as premium coatings and treatments can offer additional resistance against corrosion and wear, creating opportunities for their use in ever more demanding applications. The development and utilization of these advanced cone washers are backed by extensive research and testing, often involving simulations and real-world testing to validate their performance under extreme conditions.
Overall, the versatility and reliability of cone washers make them an indispensable component across numerous industries. Whether it’s enhancing the safety of an aircraft, improving the performance of an automobile, or reinforcing the stability of a skyscraper, cone washers continue to be a silent yet vital player in the performance and reliability of modern infrastructure and technology. Their continued evolution and application not only demonstrate the importance of these components but also highlight the ongoing need for expertise and innovation in their design and utilization.