When it comes to crafting durable and reliable fixtures in metal, small self-tapping screws are indispensable tools for both professionals and DIY enthusiasts. These screws are not just fasteners; they are precision-engineered components designed to cut their threads as they penetrate the material, offering a secure and lasting grip. Their design and functionality make them ideal for applications in electronics, machinery, and even home improvement projects.
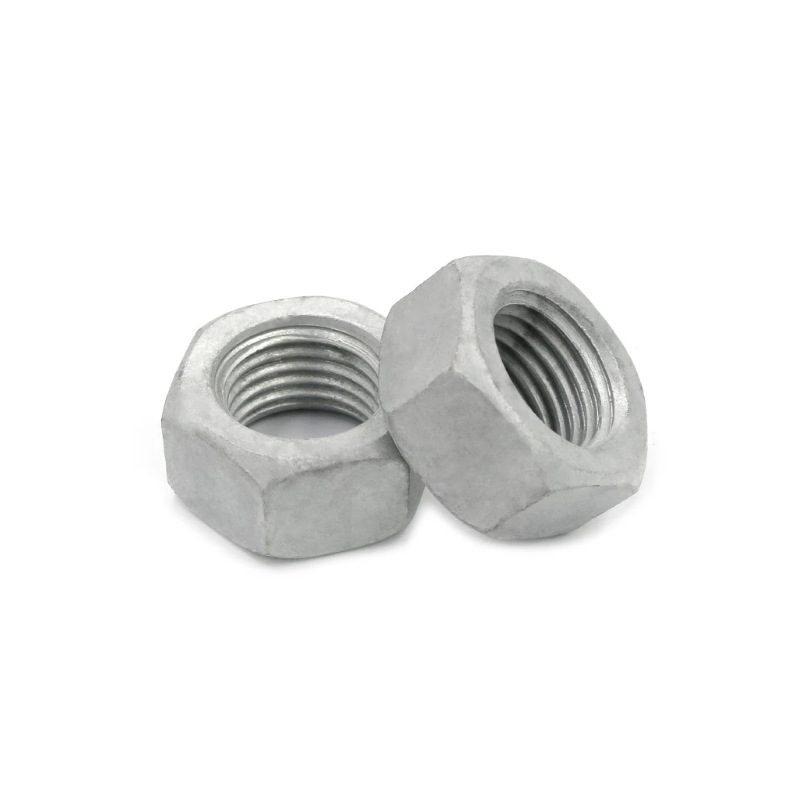
Understanding the true value of self-tapping screws begins with appreciating their design intricacies. Unlike ordinary screws, self-tapping screws do not require pre-drilled pilot holes. This feature is vital for projects where speed and efficiency are paramount. The sharp, robust threads and pointed tip are engineered to tap their paths through metal surfaces, making them a cornerstone in metalworking. This eliminates additional preparatory steps, thus reducing labor time and potential errors.
When handling metal surfaces, ensuring joint stability is crucial. Manufacturers have advanced the design of self-tapping screws to include variations such as thread-cutting and thread-forming screws. Thread-cutting screws are equipped with cutting flutes that remove material from the metal, while thread-forming screws displace material to create the internal thread. Selecting the correct type is essential depending on the material's hardness and thickness, contributing to the fixture's overall reliability.
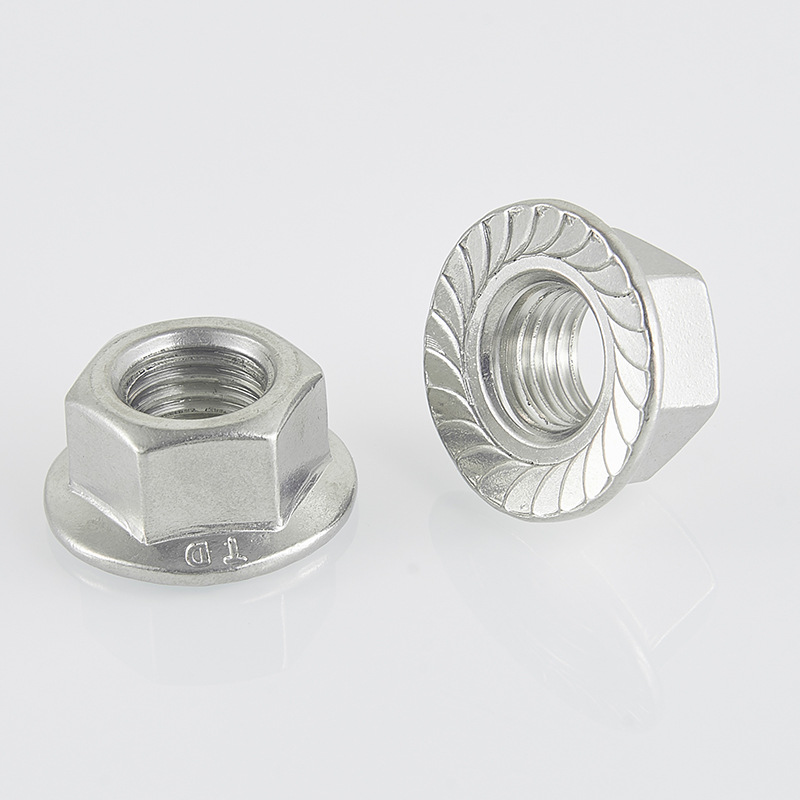
Experienced professionals understand that material selection for screws can significantly impact performance. Stainless steel, carbon steel, and alloy steel are commonly used due to their superior tensile strength and resistance to corrosion. Stainless steel screws are particularly favored in environments susceptible to moisture or chemical exposure because of their innate ability to resist corrosion, thus prolonging the life of the fixture.
The versatility of small self-tapping screws extends to their head designs. Flathead, pan head, and hex head are popular choices, each serving a specific purpose. Flathead screws are ideal for flush finishes, ensuring that the screw head does not protrude from the surface. Pan head screws offer a broader bearing surface, useful in affixing thin materials or where a low profile is required. Meanwhile, hex head screws provide grip and torque advantages, especially when using power tools.
small self tapping screws for metal
Optimal usage also involves torque control. Over-tightening a self-tapping screw in metal can strip the threads or even break the screw. Employing torque wrenches or screwdrivers with adjustable torque settings ensures that the screws are fastened to the correct tightness, maintaining structural integrity without compromising the material.
In terms of expertise, it's important to recognize the types of projects that benefit most from small self-tapping screws for metal. In aerospace manufacturing, for instance, they are crucial for assembling lightweight, yet strong components. Similarly, in electronics, they secure parts without requiring heavy-duty tools or excessive preparatory work, which can be crucial for delicate assemblies.
Moreover, maintaining stocks of these screws in various sizes can be a testament to a workshop's preparedness. Different projects will inherently require different screw sizes, and having a range from M1.6 to M8 sizes ensures that one is always ready to meet diverse project needs without delay.
Trustworthiness comes from the consistent application of best practices when using self-tapping screws. Acknowledge the importance of quality in the screws' manufacturing. Selecting screws from reputable manufacturers guarantees adherence to product standards and material quality, as verifiable through international quality assurance certifications.
In conclusion, the integration of small self-tapping screws into metalworking projects is more than just a matter of mechanical fastening. It involves an understanding of design principles, material compatibility, and application techniques. By balancing these elements, one can not only achieve optimal results in terms of functionality and aesthetic appeal but also command authority and trust within professional circles. Therefore, these small but mighty components play a pivotal role in creating enduring, professional-grade metal assemblies.