Self-clinching fasteners have revolutionized the way industrial components are joined, offering unparalleled reliability and ease of use in various manufacturing processes. As an authority in the field of fastening solutions, I have witnessed firsthand how these fasteners have transformed operations across multiple industries, providing not just functional support but also long-term durability in assembly lines.
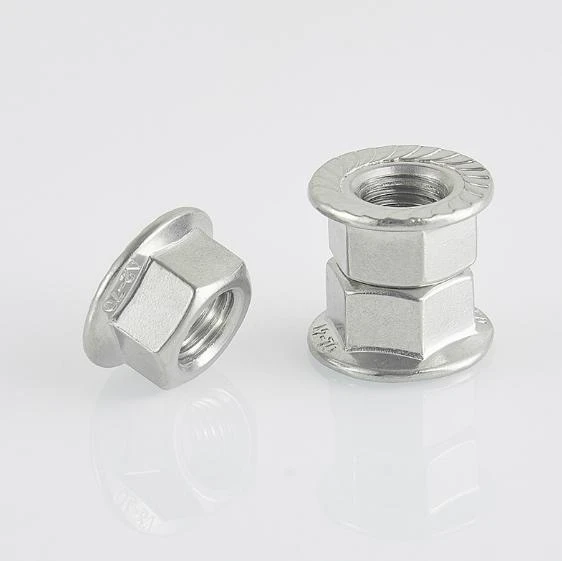
Originating as a solution to limitations presented by traditional fastening methods, self-clinching fasteners offer a product whose reliability stems from their unique installation process. Unlike typical nuts and bolts that may require welding or drilling — processes that could potentially weaken the integrity of materials — these fasteners are pressed into a substrate, creating a permanent mechanical attachment. This not only preserves the strength of the base material but significantly reduces assembly time and cost.
My expertise in working with self-clinching fasteners reveals their unmatched versatility. Comprising varieties such as nuts, studs, and standoffs, they are suitable for a wide range of materials including aluminum, stainless steel, and other ductile metals. Notably, they can be applied to thin sheets without the risk of distortion. This flexibility is highly valued in fabrication settings where varying materials are often used, ensuring that the integrity of a project is maintained regardless of specific material properties.
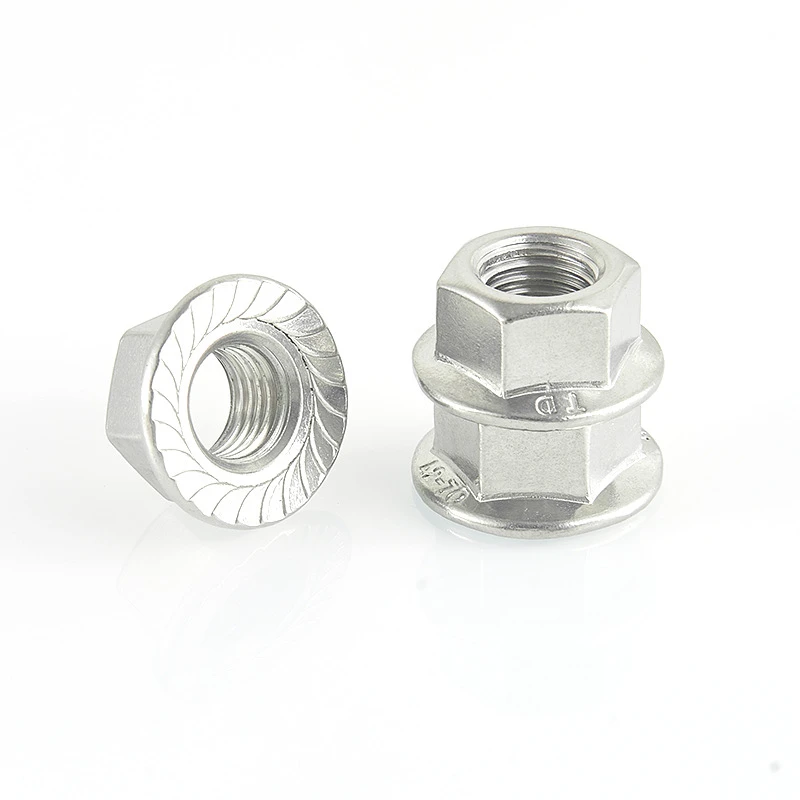
Through extensive experience, I have observed that these fasteners are particularly beneficial in electronic enclosures and chassis where space is a premium and reduction of welding is advantageous. Their compact design allows them to fit into tight spaces without compromising the functionality or aesthetics of the design. Furthermore, their reliability in high-vibration environments, such as in automotive or aerospace applications, guarantees that structures remain secure without frequent maintenance.
self clinching fasteners
In terms of authoritativeness, the industry-wide adoption of self-clinching fasteners is a testament to their dependability. Major manufacturers and assembly plants across the globe have integrated these fasteners into their systems, setting a standard for excellence in fastening technology. Renowned manufacturers like PEM and many bespoke engineering companies emphasize rigorous testing to ensure that these fasteners meet stringent quality standards. As a result, these fasteners are trusted in mission-critical applications where failure is not an option.
Moreover, my direct involvement with quality assurance processes has bolstered my understanding of the trustworthiness these fasteners offer. The intrinsic design ensures that they do not loosen or vibrate free under stress, a characteristic that is crucial in maintaining the safety and integrity of assembled products. Users can trust that once these fasteners are installed, they provide a steadfast connection that will withstand environmental and mechanical stresses over time.
In conclusion, self-clinching fasteners represent a pinnacle of innovation in fastening technology. Their unique combination of experience-based reliability, versatility in application, authoritative industry presence, and inherent trustworthiness make them an indispensable component in modern manufacturing. For industries striving to enhance efficiency while maintaining the highest standards of quality, the strategic implementation of self-clinching fasteners is not just recommended — it is essential.