M5 flange nuts may appear as mere hardware components to the untrained eye, but for industry professionals, they are indispensable in ensuring secure and stable connections in a plethora of applications. A flange nut is characterized by its large flange at one end, which acts as an integrated washer. The design serves multiple purposes distributing the pressure of the nut over the part being secured, reducing the chance of damage, and ensuring that the nut stays put.
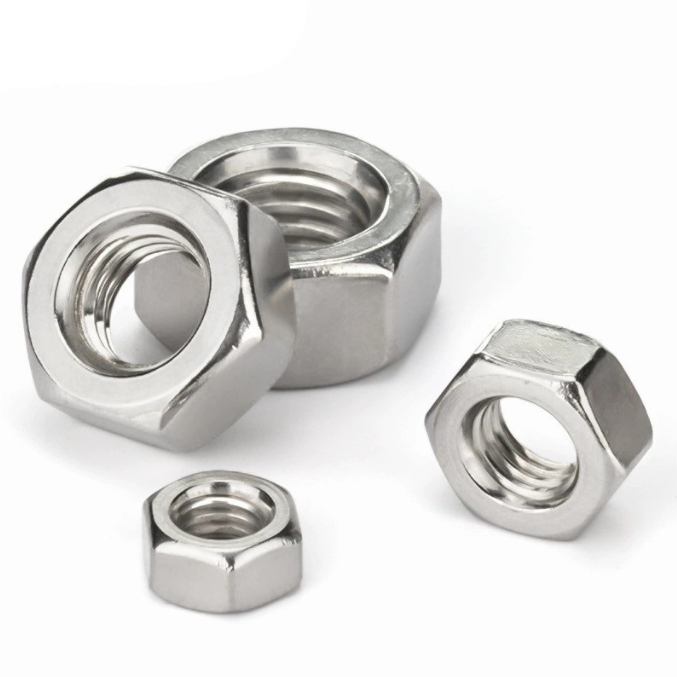
The M5 flange nut is particularly popular in automotive repairs, machinery, and complex engineered structures, where precision and reliability are paramount. Designed for an M5 bolt, this flange nut guarantees a snug fit, ensuring that vibrations or dynamic forces do not compromise the structure’s integrity. Experienced engineers emphasize the importance of using the correct size and type of flange nut, as selecting the wrong specification can lead to assembly failures or system malfunctions.
One key aspect of the M5 flange nut's value is its material composition. Typically manufactured from steel or stainless steel, M5 flange nuts offer exceptional resistance to corrosion and wear, making them suitable for challenging environments. The plating or coating, often zinc or black oxide, further enhances their durability by providing a layer of protection against rust and environmental stressors. Professionals in metallurgical fields can attest to the benefits of these protective layers in extending the lifespan of components.
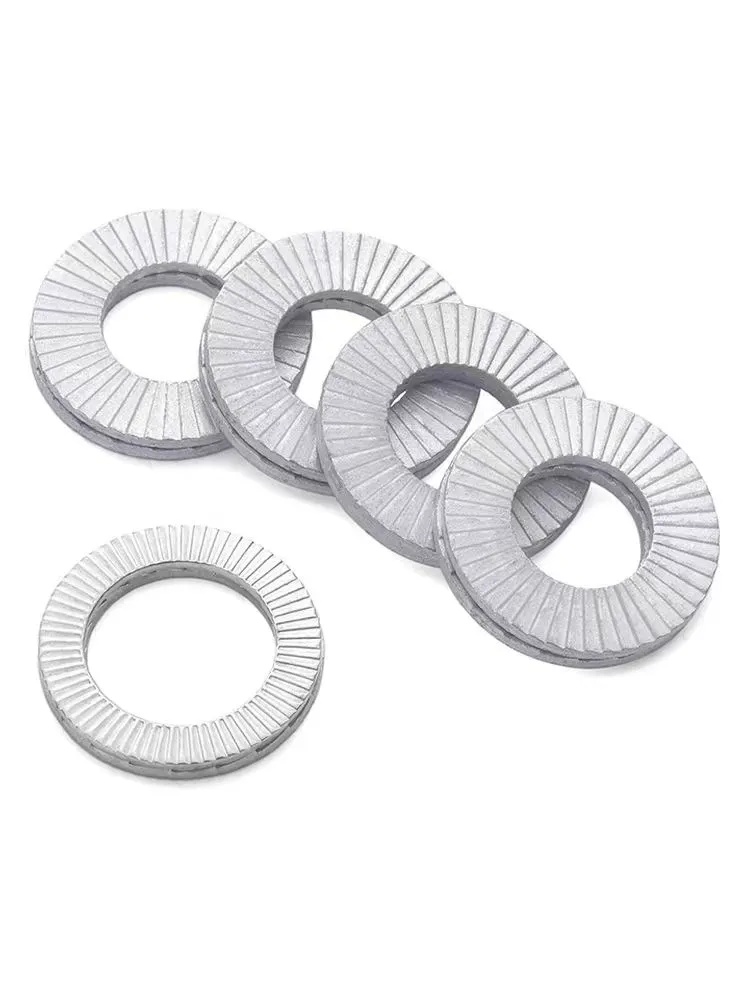
Moreover, the M5 size is particularly relevant in precision engineering. The reason lies in its compatibility with a wide range of components and its capability to provide robust holding power without excessive bulk. This makes it ideal for use in electronics and fine instruments where weight and space constraints are critical. Expert technicians and engineers who are familiar with the intricacies of such sensitive assemblies often opt for the M5 flange nut due to its versatility and reliability.
m5 flange nut
From a design perspective, the flange provides a larger surface area which is crucial in load distribution. This characteristic prevents localized stress points that could lead to material fatigue or cracking. In structural applications, especially in areas subject to dynamic stresses, this feature becomes critical. Seasoned mechanical engineers understand that the overall durability of a structure can be as dependent on the choice of a nut size as on the primary material choice.
Authoritative figures in quality assurance and standards often remind us of the compliance benefits of using standardized components like the M5 flange nut. Always meeting international and industry regulations, these nuts ensure that assemblies remain consistent, reliable, and safe. It is not uncommon for industry veterans to rely on a catalog of standard components, such as the M5 flange nut, not only to ensure compliance but also to streamline manufacturing processes and cost management.
In terms of trustworthiness, the M5 flange nut shines in its quality assurance aspect. Reputable manufacturers subject these nuts to stringent testing, ensuring that every piece conforms to high standards of quality. This rigorous approach guarantees engineers and end-users peace of mind in knowing that each nut will perform as expected, even in the most demanding conditions.
In conclusion, an M5 flange nut is more than just a simple fastener—it's a crucial element in constructing safe and efficient mechanical systems. Expertise in material science, engineering design, and manufacturing standards all contribute to understanding and utilizing these components effectively. Trusted by professionals worldwide, the M5 flange nut embodies reliability, made possible through carefully chosen materials, precise engineering, and stringent quality control. Therefore, when selecting a fastener, considering the M5 flange nut could be the key to achieving both operational excellence and structural integrity.