Hot-dipped screws have become indispensable in various industrial and construction applications due to their unparalleled durability and anti-corrosive properties. These screws are particularly renowned for their resilience in external environments where exposure to humidity, harsh weather conditions, and salt air can rapidly deteriorate standard fasteners. This article delves into the significant aspects of hot-dipped screws, shedding light on their utility, manufacturing process, and benefits within specific industries.

Utilizing zinc as a protective barrier, hot-dip galvanization involves immersing the screws in molten zinc, creating a thick, adherent coating that provides long-lasting protection against corrosion. This process not only strengthens the screw but also extends its life span considerably, making it the preferred choice for many who seek reliability in structural applications.
For professionals in the construction industry, the choice of fasteners can make or break a project. Hot-dipped screws offer an extra level of safety compared to their non-galvanized counterparts. The protective zinc coating acts as a barrier to corrosion, thus preserving the metal underneath and ensuring structural integrity over time. This is particularly important in coastal construction projects, where exposure to marine humidity can severely impact the longevity of building materials. In such settings, using hot-dipped screws can significantly reduce maintenance costs and ensure that infrastructures remain safe and durable over the years.
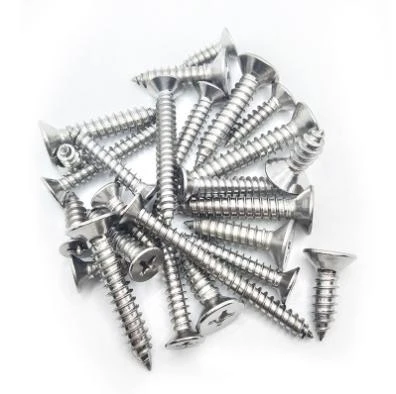
Moreover, in the automotive industry, hot-dipped screws are increasingly becoming integral due to their superior resistance against harsh environmental conditions, such as road salt and moisture. These screws are utilized in various components of a vehicle's build, ensuring that the relentless exposure to various elements does not lead to the premature failure of parts. Manufacturers favor these screws not only for their durability but also because they contribute to overall vehicle safety, providing peace of mind to both manufacturers and end-users.
Hot-dipped screws also find their worth in the energy sector, particularly within solar panel installations. The extended lifespan of these fasteners means that solar arrays can be expected to perform optimally without frequent maintenance or replacements due to rusting bolts and screws. Given that solar panels are often installed in open fields, rooftops, or other exposed locations, the use of hot-dipped screws ensures that the mounting structures remain reliably intact, safeguarding the investment and efficiency of the solar array.
hot dipped screws
The forestry and agriculture sectors are other prime areas where hot-dipped screws show their mettle. In these environments, equipment and structures frequently encounter moisture, fluctuating temperatures, and other challenging conditions that could quickly degrade lesser-quality materials. Whether it involves constructing barns, machinery repair, or building robust fencing solutions, hot-dipped screws demonstrate unmatched performance, securing parts and structures from the devastating effects of rust and corrosion.
From a professional standpoint, understanding the manufacturing process and benefits of hot-dipped screws can place experts at the forefront of their fields. By specifying the use of these screws in projects, professionals can assure clients and stakeholders of a commitment to quality and long-term value. For engineers, architects, and contractors, an in-depth knowledge of how these screws work and how best to implement them within various frameworks can enhance not only the durability of their projects but also their credibility in delivering technically sound and sustainable solutions.
As industry trends move towards sustainability and long-lasting building solutions, hot-dipped screws emerge as a pivotal component in construction and manufacturing strategies focused on reducing environmental impact through extended product life cycles.
In conclusion, hot-dipped screws symbolize reliability and longevity across a multitude of applications. Their role in ensuring structural stability and reducing the frequency of replacement makes them a cost-effective choice for industries looking to maintain high safety standards while minimizing maintenance. Adopting such solutions manifests an organization's commitment to employing best practices in construction and manufacturing, ultimately leading to enhanced trust and authority in their respective fields. Understanding the intricacies and advantages of these screws enables experts to streamline operations, ensure public safety, and establish a professional reputation of unmatched expertise and reliability in the marketplace.