High-Definition Galvanizing Revolutionizing the Bolt and Nut Industry
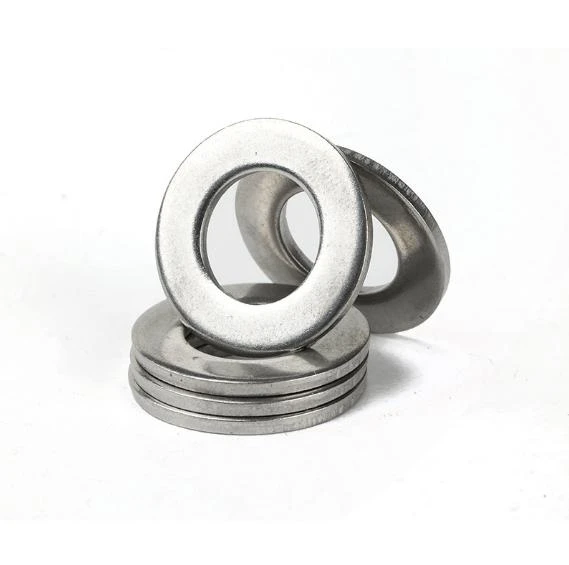
The significance of HDG (Hot-Dip Galvanized) bolts and nuts has emerged prominently in industries demanding high-durability fastening solutions. With infrastructure growth and an increasing emphasis on durability, HDG products are being hailed as essential components in construction and manufacturing sectors. These products stand out due to their exceptional resistance to corrosion, prolonging the lifespan of the connected structures—an invaluable trait in harsh environmental conditions.
In the realm of construction, experience demonstrates that HDG bolts and nuts are unparalleled when it comes to safeguarding against atmospheric and chemical corrosion. Engineers and contractors consistently report fewer maintenance issues, reduced downtime, and increased life cycles of structures when these components are employed. This reliability stems from the galvanization process, where a robust zinc coating is applied to steel or iron fasteners. The zinc forms a protective barrier, shielding the metal from moisture and corrosive substances, effectively reducing wear and tear.
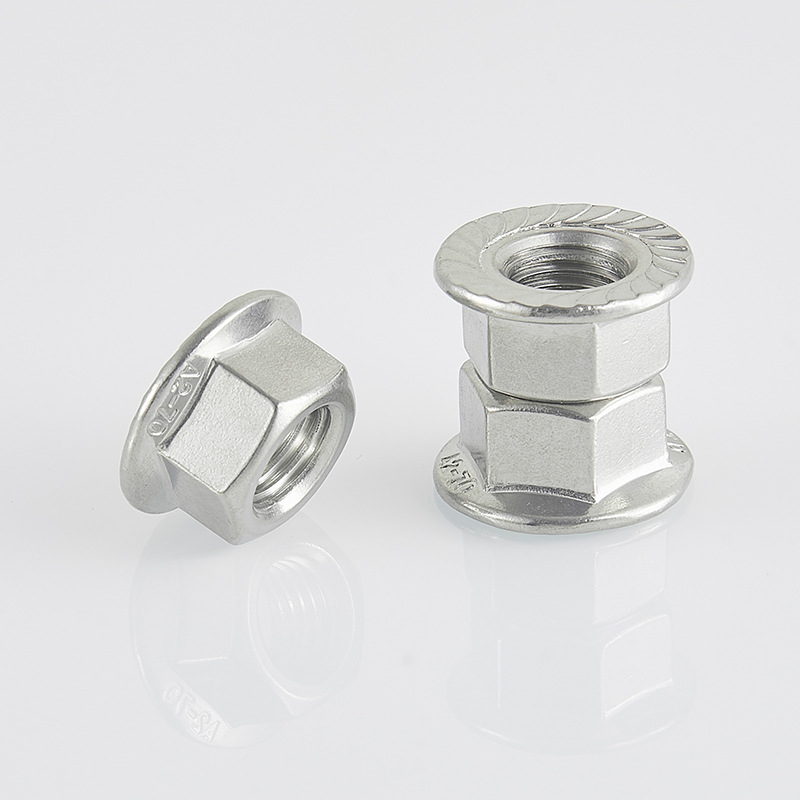
Professionals in the industry recognize the expertise required to produce high-quality HDG bolts and nuts. The manufacturing process is meticulous and demands a deep understanding of metallurgy and chemistry. Companies specializing in galvanization have refined their processes over decades, ensuring that each bolt and nut meet stringent international standards like ASTM, ISO, and BS. This adherence to global benchmarks underpins the expert craftsmanship behind HDG products, fostering trust among users worldwide.
Authoritativeness in the HDG fastener industry is solidly backed by scientific research and real-world testing. Institutions and laboratories conduct rigorous examinations to validate the performance of these galvanized components under various environmental stresses. Research consistently substantiates that HDG bolts and nuts exhibit superior performance compared to their non-galvanized or electro-galvanized counterparts. This robust evidence is well-documented in engineering journals and technical publications, cementing the authoritative stance of HDG fasteners in the industry.
hdg bolts and nuts
The trustworthiness of HDG bolts and nuts is further emphasized through their widespread adoption in critical infrastructure projects, such as bridges, skyscrapers, and transportation systems. The confidence placed in these components by engineers and architects is a testament to their reliability. Furthermore, numerous case studies highlight the successful deployment of HDG fasteners in projects where failure is not an option. This track record bolsters trust among stakeholders, from project planners to end-users.
Furthermore,
choosing HDG bolts and nuts aligns with sustainable practices. The longevity and durability these products provide mean fewer replacements, conserving resources, and reducing environmental impact over time. Galvanization itself can be environmentally advantageous. The process is efficient, and the zinc coating can be recycled, contributing to a circular economy.
For those navigating the competitive landscape of construction and manufacturing, leveraging HDG bolts and nuts offers a clear advantage. Not only do these products provide unparalleled protection and longevity, but they also communicate a commitment to quality, safety, and sustainability. As businesses strive to enhance their reputation through reliability and cutting-edge solutions, HDG products prove to be not just a choice but a necessity.
In conclusion, HDG bolts and nuts represent the pinnacle of fastening solutions, combining experience, expertise, authoritativeness, and trustworthiness. Their growing prevalence in the marketplace is a clear indicator of their unmatched utility and performance. For industries that prioritize longevity, strength, and resource efficiency, investing in high-quality HDG fasteners is an unmistakable step towards enhanced infrastructure integrity.