When diving into the realm of hardware components, the flange nut often emerges as a versatile and indispensable element. Despite its nondescript presence in the world of manufacturing and construction, the flange nut can be a pivotal factor in determining the robustness and reliability of a project. With its built-in washer-like flange that distributes pressure and reduces the risk of damage to the assembly, this nut is particularly essential in applications where reliability and stability are paramount.
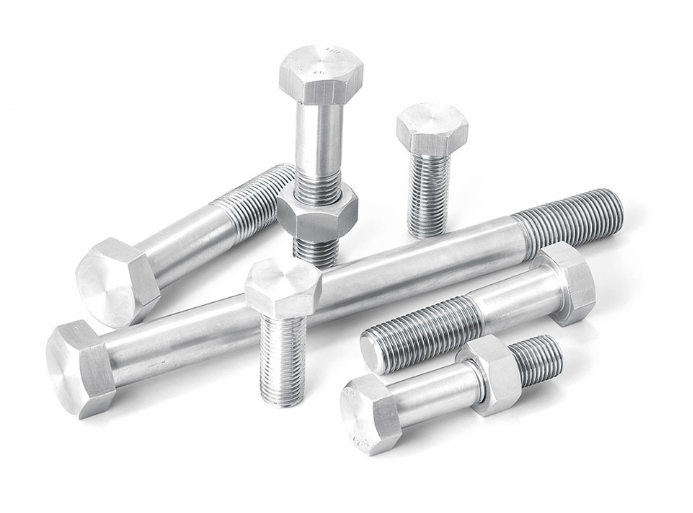
Experience in the field shows that one of the primary concerns for professionals is the variation in flange nut prices. This fluctuation is influenced by several factors, each playing a crucial role in cost assessment. Understanding these variables is vital for project managers and procurement officers to make informed decisions, ensuring both quality and budgetary compliance.
Firstly, material composition is a key determinant of flange nut pricing. Stainless steel, for example, is often preferred for its corrosion resistance and strength, particularly in applications prone to moisture or extreme environmental conditions. However, stainless steel flange nuts typically come at a higher price than those made from carbon steel or zinc-plated alternatives. In industries where durability and longevity are critical, such as aerospace or marine, the investment in higher-quality materials proves worthwhile, reinforcing the concept of long-term cost efficiency over immediate cost savings.
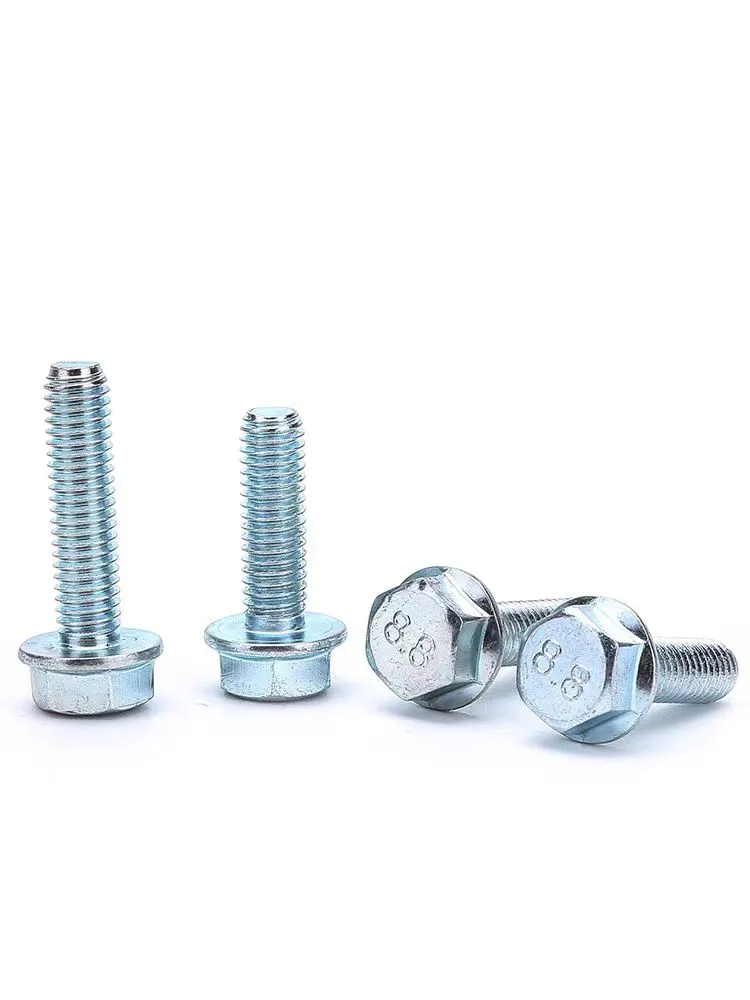
Furthermore, the manufacturing process can significantly impact flange nut costs. Techniques such as hot forging, cold forging, and machining each influence the final price. Hot forging generally allows for stronger, more resilient nuts, capable of withstanding higher stress levels. However, this method is more expensive than cold forging or machining. Understanding the specific requirements of a project allows professionals to balance these production methods with economic constraints, ensuring that the chosen flange nuts meet both performance and financial criteria.
flange nut price
When assessing flange nut pricing, it's also critical to consider the effect of quantity on cost. Bulk purchasing often leads to reduced unit prices, an advantage widely recognized within procurement strategies. Supply chain experts emphasize negotiating with manufacturers for bulk orders, not only to procure favorable pricing but also to ensure the consistency and availability of stock, thereby avoiding potential project delays.
The geographical origin of the flange nuts also bears impact on their price. Nuts manufactured locally might command a higher price due to stricter regulations and labor costs, but also offer reduced shipping costs and faster delivery times. On the other hand, importing flange nuts might initially seem more economical; however, when including taxes, tariffs, and longer wait times, the apparent savings can quickly diminish. As such, a thorough cost-benefit analysis considering all variables—including shipping logistics and potential geopolitical influences—is essential for accurate budgeting.
Evidently, selecting the right flange nut for any project is not just a question of finding the lowest price. It involves a nuanced understanding of the interplay between quality, material, manufacturing process, purchase volume, and source location. Professionals with expertise in these areas are best positioned to make informed decisions that support both the structural integrity and financial feasibility of their projects.
To conclude, the comprehensive understanding of flange nut pricing is integral to successful project management. By accounting for the myriad factors that influence cost, from material selection and manufacturing method to order volume and sourcing, professionals can assure that their choices are both economical and performance-driven. This approach not only strengthens the outcome of projects but also consolidates the trustworthiness of a business in delivering quality solutions within budgetary confines.