Zinc coated galvanized washers have become an essential component in various industries, offering both functionality and reliability. These small but crucial elements are often overlooked, yet they play a pivotal role in ensuring the stability and longevity of numerous structures and devices. Drawing from years of experience in the field of metal fasteners, this article will delve into the intricacies of zinc coated galvanized washers, highlighting their applications, benefits, and the science behind their corrosion resistance.
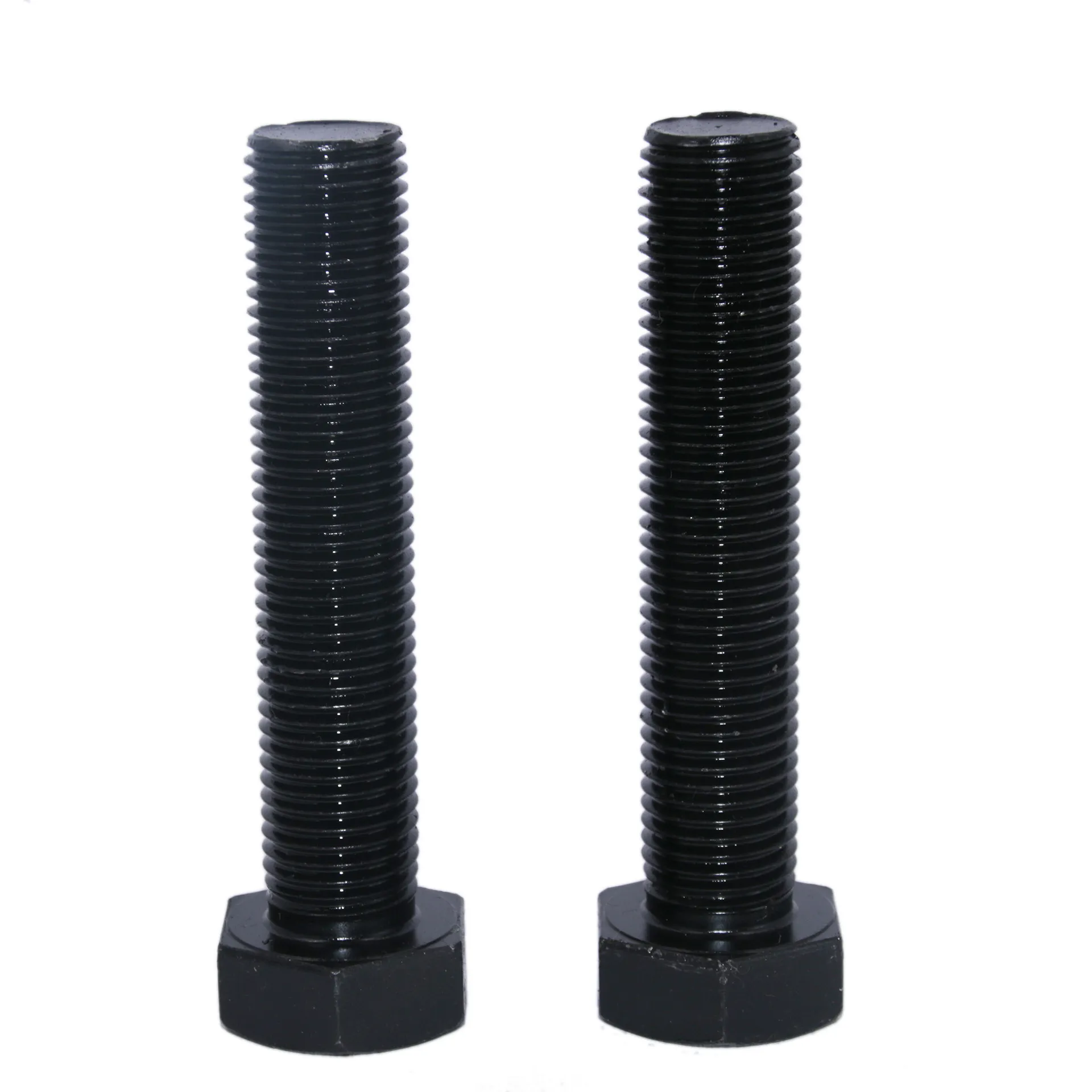
Understanding the unique attributes of zinc coated galvanized washers is imperative for anyone involved in construction, automotive, or manufacturing industries. Galvanization, a process developed over a century ago, involves the application of a protective zinc layer to steel or iron to prevent rusting. The resulting product offers enhanced durability and resilience against the elements, essential qualities for fasteners exposed to harsh or variable environments.
One of the standout features of zinc coated galvanized washers is their excellent corrosion resistance. This is achieved through the sacrificial protection mechanism, where the zinc coating corrodes preferentially to the steel substrate. Experts in material science explain that this sacrificial nature of zinc not only protects the base metal but also prevents the spread of corrosion if the coating is damaged. This property makes these washers an authoritative choice in environments prone to moisture and salt exposure, such as coastal regions or industrial areas.
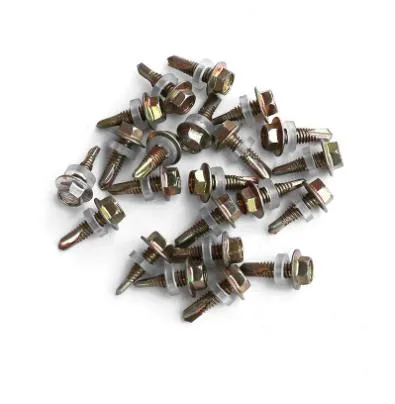
Professionals working with zinc coated galvanized washers often praise their versatility. These washers are used in conjunction with bolts and nuts to distribute the load of the fastener, prevent wear, and reduce vibration. Their adaptability makes them suitable for a wide range of applications, from securing heavy structures to delicate electronic assemblies. In industries where trustworth reliability is non-negotiable, such as aerospace or construction, the adherence to standards and regulations surrounding galvanized washers ensures their continued preeminence.
zinc coated galvanized washer
From a product standpoint, selecting the right type of zinc coated galvanized washer can significantly impact performance. Variations in thickness, diameter, and coating grade afford tailored solutions to specific needs. Experts advise consulting with manufacturers or suppliers who have a proven track record of enforcing quality control measures. This due diligence ensures the washers employed meet the stringent criteria demanded by safety and operational protocols.
Notably, the perceived simplicity of washers belies the complex technological advancements involved in their production. Modern galvanization techniques have evolved, granting a cleaner application and a more consistent coating thickness. And while the industry offers myriad options, the choice to favor zinc coated galvanized washers speaks volumes about the commitment to both efficacy and longevity in any given project.
Incorporating zinc coated galvanized washers into a project underscores a strategic decision to prioritize both structural integrity and economic efficiency. The upfront investment in choosing high-quality washers is offset by their extended service life and reduced maintenance costs. Over time, this translates to savings and peace of mind, reinforcing their position as a smart investment for any forward-thinking enterprise.
In conclusion, zinc coated galvanized washers encapsulate the intersection of simple utility and advanced engineering. Experts in the field continuously advocate for their use, citing the blend of strength, reliability, and resistance to environmental factors. For those in industries where even the most minor components make monumental differences, understanding the full scope of benefits provided by zinc coated galvanized washers ensures informed decision-making and sustained operational success.