When selecting washers for 3/8 bolts, one often encounters a variety of options in terms of materials, sizes, and types, each tailored to specific applications and environments. As a professional with extensive experience in the fastener industry, I understand the critical role that the right washer can play—not only in ensuring the longevity of a bolted connection but also in optimizing its performance under various conditions.
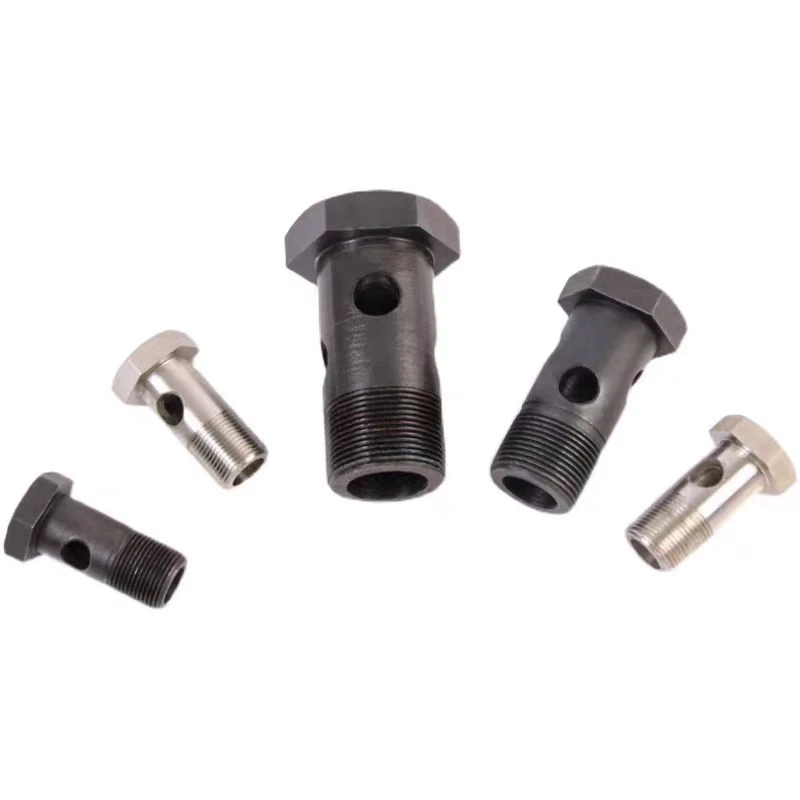
The primary function of a washer is to distribute the load of the bolt or fastener over a larger area, thereby minimizing the risk of damage or deformation to the workpiece. With 3/8 bolts, commonly used in both light and heavy-duty applications, choosing the appropriate washer can impact the safety, efficiency, and reliability of the structure or machinery involved.
Material Matters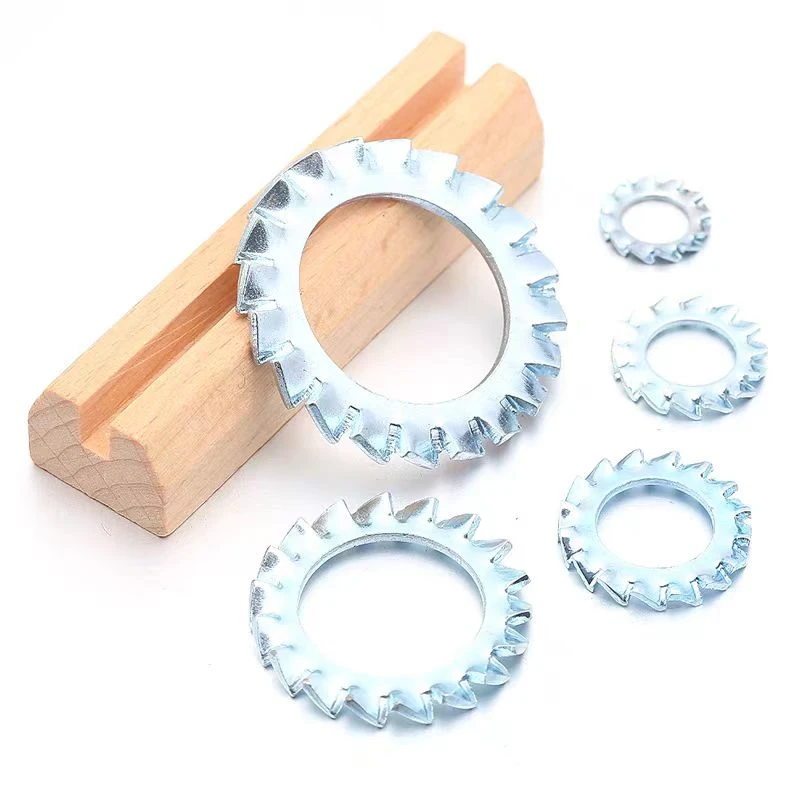
The choice of material for washers is typically influenced by the working environment and the materials of the bolt and application. Stainless steel washers, for example, are an excellent choice for environments prone to corrosion due to their resistance to rust and their excellent strength-to-weight ratio. They're particularly useful in marine and outdoor applications where weathering is an everyday challenge. For high-temperature environments, a more specialized alloy like Inconel might be advisable due to its ability to maintain integrity under extreme heat.
For applications where electrical conductivity is a priority, copper washers are often utilized. They provide excellent thermal management capabilities and ensure a stable and reliable conductive path. Though they may be softer than steel, which might not be ideal for environments requiring the utmost structural integrity, their thermal and conductive properties make them indispensable in electronic and automotive applications.
Comprehensive Understanding of Washer Types
Three primary types of washers are relevant to 3/8 bolts flat washers, lock washers, and fender washers. Each serves a distinct purpose and should be selected based on specific needs
1. Flat Washers Often used in general applications, flat washers are designed to increase the load-bearing surface under the fastener head, thereby preventing loosening through vibration or wear of the surface over time. They are the go-to choice for applications where surface protection and load distribution are key concerns.
washer for 3 8 bolt
2. Lock Washers Designed to prevent loosening through vibration, lock washers are invaluable in dynamic environments with frequent motion or exposure to vibrations. Split-ring lock washers and toothed lock washers are common varieties, each providing a level of mechanical locking.
3. Fender Washers With larger diameters compared to their hole sizes, fender washers are perfect where a larger surface area for load distribution is necessary, such as with softer materials or oversized holes.
Expertise in Installation
Installation technique is a cornerstone of washer performance. Precision during installation is essential. Washers must always be placed on the side receiving the nut, unless specified otherwise, to maximize their load distribution capability. Additionally, it is vital to ensure the washer is perfectly flat during installation to prevent angular loads on the bolt, which could lead to premature failure.
Utilizing a torque wrench can ensure the bolt is tightened to the correct specifications. Over or under-tightening can impede the washer's performance, either by yielding unnecessary stress on the materials or allowing for movement that could lead to loosening.
The Trust Factor
Establishing trust in the selection of washers for 3/8 bolts involves not only choosing materials and types wisely but also sourcing from reputable manufacturers. Always opt for washers that meet industry-standard certifications and have undergone rigorous testing. Suppliers who can provide documentation and verification increase the trustworthiness of the washers they provide, an essential factor for both safety and performance in critical applications.
In conclusion, washers for 3/8 bolts, though seeming like minor components, are vital in ensuring the integrity, reliability, and durability of bolted connections. By leveraging knowledge of materials, understanding different washer types, and adhering to best practices in installation, one can fully optimize their application. As experts and consumers, the emphasis should always be on informed purchasing decisions and meticulous installation processes to guarantee optimal outcomes.